An induction melting furnace is a sophisticated piece of equipment designed to melt metals using electromagnetic induction. Its design primarily revolves around key components such as the power supply, induction coil, crucible, cooling system, and control mechanisms. These components work in harmony to ensure efficient melting, precise temperature control, and operational safety. The furnace's design is tailored to meet specific industrial needs, such as high melting rates, energy efficiency, and the ability to handle various types of metals and alloys. Below, we break down the design elements and their functionalities in detail.
Key Points Explained:
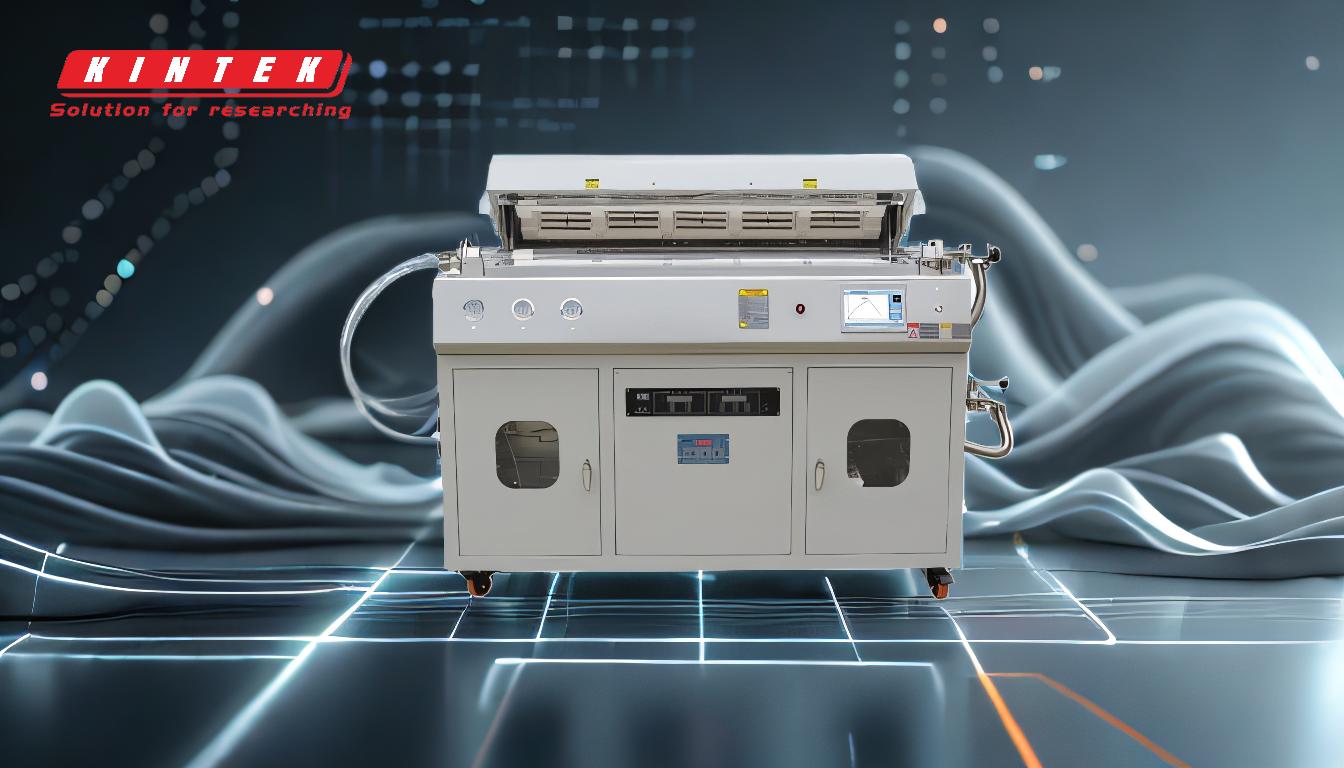
-
Power Supply:
- The power supply is the heart of the induction melting furnace, providing the necessary electrical energy to generate the electromagnetic field.
- It typically operates at medium or high frequencies, depending on the application and the type of metal being melted.
- The power supply's configuration and efficiency directly impact the melting rate and energy consumption.
-
Induction Coil (Induction Ring):
- The induction coil, often made of copper, is responsible for generating the alternating magnetic field that induces eddy currents in the metal charge.
- These eddy currents generate heat, which melts the metal.
- The coil is usually water-cooled to prevent overheating and maintain operational stability.
-
Crucible:
- The crucible is a refractory container that holds the metal charge during the melting process.
- It is designed to withstand high temperatures and chemical reactions with molten metals.
- The choice of crucible material (e.g., quartz, graphite, or ceramic) depends on the type of metal being melted and the desired melting efficiency.
-
Cooling System:
- A cooling system, often water-based, is essential to maintain the temperature of the induction coil and other critical components.
- It prevents overheating, ensures consistent performance, and extends the lifespan of the furnace.
-
Vacuum System (for Vacuum Induction Melting Furnaces):
- In vacuum induction melting furnaces, a vacuum system is integrated to create a low-pressure environment.
- This system is crucial for controlling the alloy chemistry and preventing contamination from atmospheric gases.
- It includes pumps, valves, and seals to maintain the desired vacuum level.
-
Furnace Shell and Auxiliary Devices:
- The furnace shell houses all the major components and provides structural integrity.
- It may include observation windows, temperature measurement devices, feeding mechanisms, and sampling tools.
- A tilting mechanism is often incorporated to pour the molten metal into molds.
-
Control System:
- The electric control system manages the operation of the furnace, including power regulation, temperature control, and safety protocols.
- Advanced systems may include automation features for precise control and monitoring.
-
Yokes and Protective Mechanisms:
- Yokes are magnetic components that protect the induction coil and enhance the magnetic field's efficiency.
- They also help in reducing electromagnetic interference and improving energy transfer.
By integrating these components, an induction melting furnace achieves high efficiency, precise control, and versatility in melting various metals and alloys. The design considerations ensure that the furnace meets industrial demands while maintaining safety and reliability.
Summary Table:
Component | Functionality |
---|---|
Power Supply | Provides electrical energy to generate the electromagnetic field, impacting melting rate and efficiency. |
Induction Coil | Generates alternating magnetic field to induce eddy currents, melting the metal. Water-cooled for stability. |
Crucible | Holds the metal charge; made of refractory materials to withstand high temperatures and chemical reactions. |
Cooling System | Maintains component temperatures, prevents overheating, and ensures consistent performance. |
Vacuum System | Creates a low-pressure environment for vacuum induction melting, controlling alloy chemistry. |
Furnace Shell | Houses components, includes observation windows, feeding mechanisms, and tilting mechanisms. |
Control System | Manages power regulation, temperature control, and safety protocols, often with automation features. |
Yokes | Protects the induction coil, enhances magnetic field efficiency, and reduces electromagnetic interference. |
Discover how an induction melting furnace can optimize your metal melting process—contact our experts today for more details!