A furnace and a retort are both heating devices, but they serve different purposes and operate under distinct principles. A furnace is designed to reach extremely high temperatures, often used in industrial settings for processes like annealing, smelting, and heat treatment of metals. It can hold materials at high temperatures for extended periods, making it suitable for large-scale projects. On the other hand, a retort is a specialized vessel used in chemical processes, such as distillation or pyrolysis, where substances are heated in a closed system to produce gases or other byproducts. The key difference lies in their application: furnaces are primarily used for heating and altering the physical properties of materials, while retorts are used for chemical transformations in a controlled environment.
Key Points Explained:
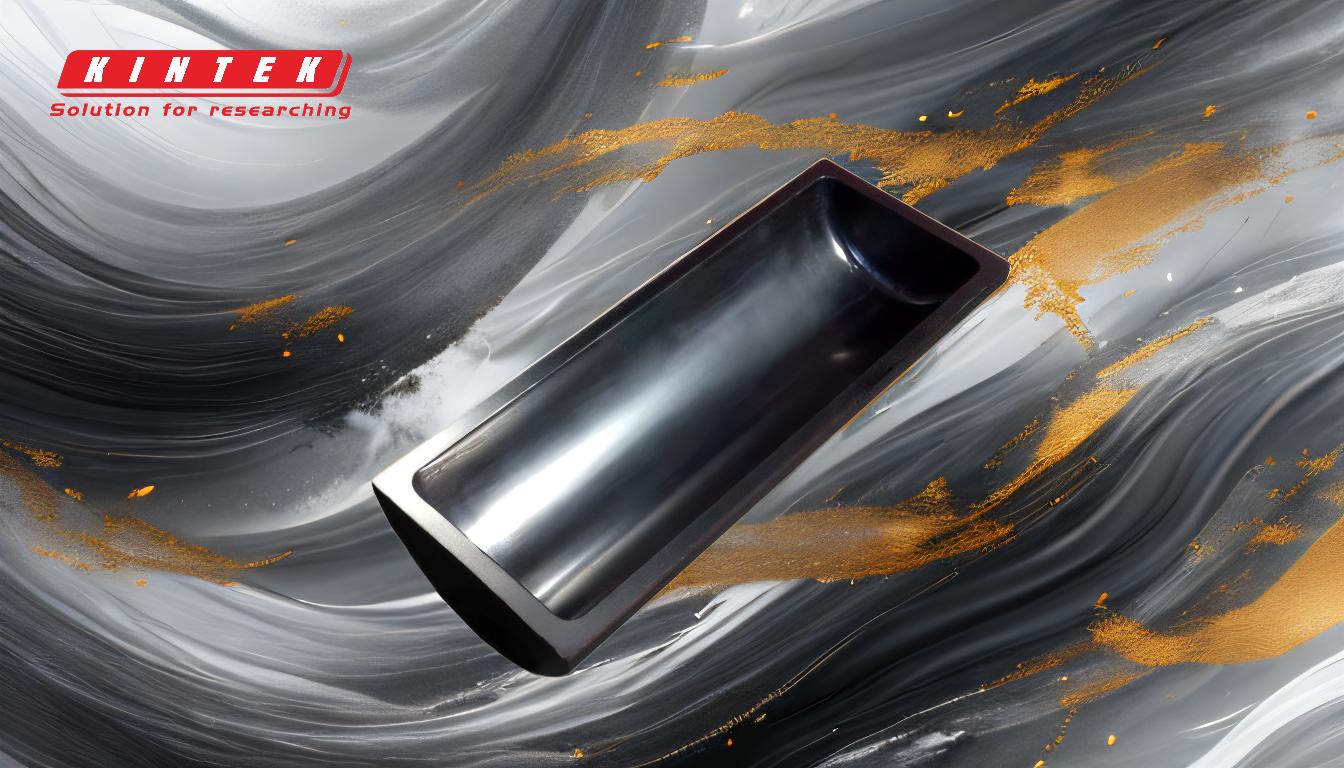
-
Purpose and Application:
- Furnace: Primarily used for heating and altering the physical properties of materials, especially metals. It is ideal for processes like annealing, smelting, and heat treatment. Furnaces are often used in industrial settings where large-scale projects require sustained high temperatures.
- Retort: Used for chemical processes such as distillation, pyrolysis, or decomposition of substances. It is designed to heat materials in a closed system, often to produce gases or other byproducts. Retorts are commonly used in laboratories and certain industrial processes where controlled chemical reactions are necessary.
-
Temperature Range:
- Furnace: Capable of reaching extremely high temperatures, often exceeding 1000°C. This makes it suitable for processes that require significant heat, such as melting metals or heat treatment.
- Retort: While retorts can also reach high temperatures, their primary function is not just to heat but to facilitate chemical reactions. The temperature range in a retort is often tailored to the specific chemical process being conducted.
-
Design and Structure:
- Furnace: Typically designed as an enclosed oven with robust insulation to maintain high temperatures. It may have multiple chambers or zones to control the heating process more precisely.
- Retort: Usually a sealed vessel with a specific design to contain and direct the flow of gases or byproducts. It may include features like condensers or collection chambers to manage the products of the chemical reaction.
-
Operational Environment:
- Furnace: Often used in industrial environments where large-scale heating is required. The focus is on maintaining consistent high temperatures over extended periods.
- Retort: More commonly found in laboratories or specialized industrial settings where precise control over chemical reactions is needed. The environment is often more controlled to ensure the integrity of the chemical process.
-
Material Compatibility:
- Furnace: Designed to handle a wide range of materials, particularly metals, that require high-temperature processing. The materials used in furnace construction must withstand extreme heat and often include refractory materials.
- Retort: Typically used with materials that undergo chemical changes when heated. The construction materials must be compatible with the chemicals involved and often include materials resistant to corrosion or chemical attack.
-
Scale of Operation:
- Furnace: Generally used for large-scale operations, capable of handling bulk materials or large metal pieces. The scale of operation is often industrial, requiring significant energy input.
- Retort: More suited to smaller-scale operations, especially in laboratory settings. While industrial retorts exist, they are often designed for specific chemical processes rather than bulk material processing.
By understanding these key differences, one can better choose the appropriate equipment for their specific needs, whether it involves high-temperature material processing or controlled chemical reactions.
Summary Table:
Feature | Furnace | Retort |
---|---|---|
Purpose | Heating and altering physical properties of materials (e.g., metals). | Chemical processes like distillation, pyrolysis, or decomposition. |
Temperature Range | Extremely high (often > 1000°C). | High, but tailored to specific chemical processes. |
Design | Enclosed oven with robust insulation. | Sealed vessel with features like condensers or collection chambers. |
Operational Environment | Industrial settings for large-scale heating. | Laboratories or specialized industrial settings for controlled reactions. |
Material Compatibility | Metals and materials requiring high-temperature processing. | Materials undergoing chemical changes; corrosion-resistant construction. |
Scale of Operation | Large-scale, industrial applications. | Smaller-scale, often laboratory-based. |
Need help choosing the right heating equipment? Contact our experts today for personalized advice!