Kilns and calciners are both thermal processing equipment used in various industries, but they serve different purposes and operate under distinct conditions. A kiln is primarily used for firing, drying, or hardening materials such as ceramics, cement, or bricks, often at high temperatures. It is designed to maintain consistent heat distribution and is commonly used in manufacturing and construction. On the other hand, a calciner is specifically designed for calcination, a process that involves heating materials to high temperatures to induce thermal decomposition, phase transition, or removal of volatile substances. Calciners are widely used in industries like cement production, chemical processing, and metallurgy. The key differences lie in their intended applications, temperature ranges, and the types of chemical or physical changes they facilitate.
Key Points Explained:
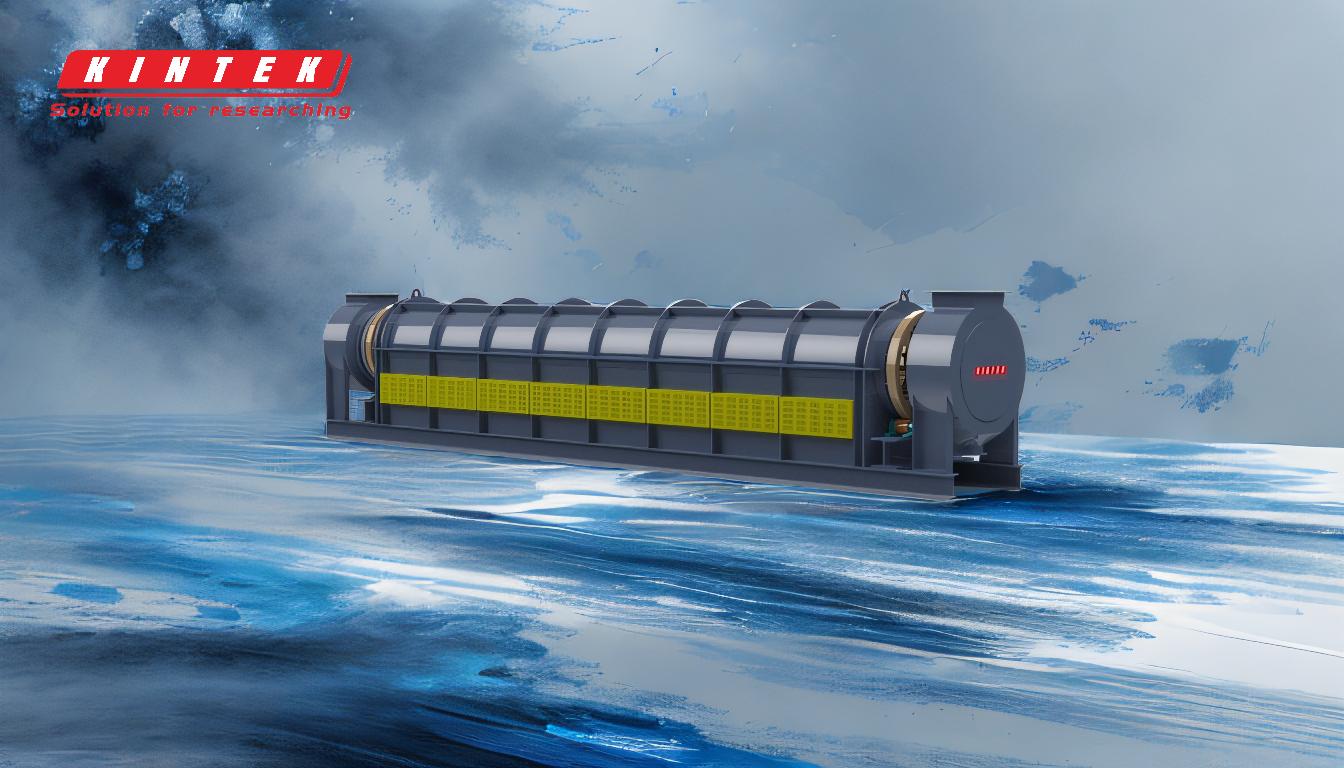
-
Primary Function and Purpose:
- Kiln: Kilns are primarily used for processes like firing ceramics, drying materials, or hardening substances such as cement or bricks. They are designed to provide consistent heat for extended periods, ensuring uniform treatment of materials.
- Calciner: Calciners are specialized for the calcination process, which involves heating materials to high temperatures to drive off volatile components, induce decomposition, or cause phase transitions. This is critical in industries like cement production, where limestone is calcined to produce lime.
-
Temperature Range:
- Kiln: Kilns typically operate at high temperatures, often ranging from 600°C to 1,400°C, depending on the material being processed. For example, ceramic kilns may operate at around 1,200°C to 1,400°C.
- Calciner: Calciners generally operate at even higher temperatures, often exceeding 900°C and sometimes reaching up to 1,600°C, to achieve the necessary chemical changes during calcination.
-
Chemical and Physical Changes:
- Kiln: The processes in a kiln are often physical, such as drying or sintering, where materials are fused without significant chemical alteration. For example, in cement production, the kiln is used to sinter raw materials into clinker.
- Calciner: Calciners are designed to induce chemical changes, such as thermal decomposition. For instance, in cement production, the calciner is used to decompose calcium carbonate (CaCO₃) into calcium oxide (CaO) and carbon dioxide (CO₂).
-
Design and Structure:
- Kiln: Kilns are typically designed as long, rotating cylinders (rotary kilns) or stationary chambers (e.g., tunnel kilns). They are built to ensure even heat distribution and are often lined with refractory materials to withstand high temperatures.
- Calciner: Calciners may also be rotary or stationary but are specifically designed to handle the high temperatures and chemical reactions involved in calcination. They often include features like preheaters or secondary combustion chambers to optimize efficiency.
-
Applications:
- Kiln: Kilns are widely used in industries such as ceramics, cement production, and metallurgy. They are essential for processes like firing pottery, producing clinker in cement plants, and heat-treating metals.
- Calciner: Calciners are critical in industries like cement production, chemical processing, and metallurgy. They are used for processes such as calcining limestone, decomposing gypsum, and producing alumina from bauxite.
-
Operational Differences:
- Kiln: Kilns are often operated continuously or in batches, depending on the application. They require precise temperature control to ensure the quality of the final product.
- Calciner: Calciners are typically operated continuously, especially in large-scale industrial applications. They require careful management of temperature and gas flow to achieve the desired chemical reactions.
-
Energy Efficiency:
- Kiln: Kilns are designed to maximize heat retention and minimize energy loss, often using refractory linings and insulation materials.
- Calciner: Calciners are optimized for energy efficiency by incorporating preheaters and heat recovery systems, which reduce the overall energy consumption required for calcination.
In summary, while both kilns and calciners are essential for high-temperature processing, they differ significantly in their primary functions, operating conditions, and applications. Kilns are more focused on physical changes like drying and sintering, whereas calciners are specialized for chemical processes like decomposition and phase transitions. Understanding these differences is crucial for selecting the right equipment for specific industrial needs.
Summary Table:
Aspect | Kiln | Calciner |
---|---|---|
Primary Function | Firing, drying, or hardening materials (e.g., ceramics, cement, bricks). | Inducing thermal decomposition, phase transition, or volatile removal. |
Temperature Range | 600°C to 1,400°C | 900°C to 1,600°C |
Chemical/Physical | Physical changes (e.g., drying, sintering). | Chemical changes (e.g., decomposition, phase transitions). |
Design | Rotary or stationary chambers with refractory linings. | Rotary or stationary with preheaters/combustion chambers for efficiency. |
Applications | Ceramics, cement production, metallurgy. | Cement production, chemical processing, metallurgy. |
Operational Mode | Continuous or batch processing. | Typically continuous operation. |
Energy Efficiency | Maximizes heat retention with insulation. | Optimized with preheaters and heat recovery systems. |
Need help choosing the right thermal processing equipment? Contact our experts today for personalized advice!