Manual and hydraulic presses are both widely used in various industries, but they differ significantly in design, operation, and application. A manual press relies on physical effort to apply pressure, making it cost-effective but labor-intensive. In contrast, a hydraulic press uses hydraulic systems to generate force, offering precision, consistency, and reduced physical effort. The choice between the two depends on the specific requirements of the task, including the need for accuracy, repeatability, and ease of use.
Key Points Explained:
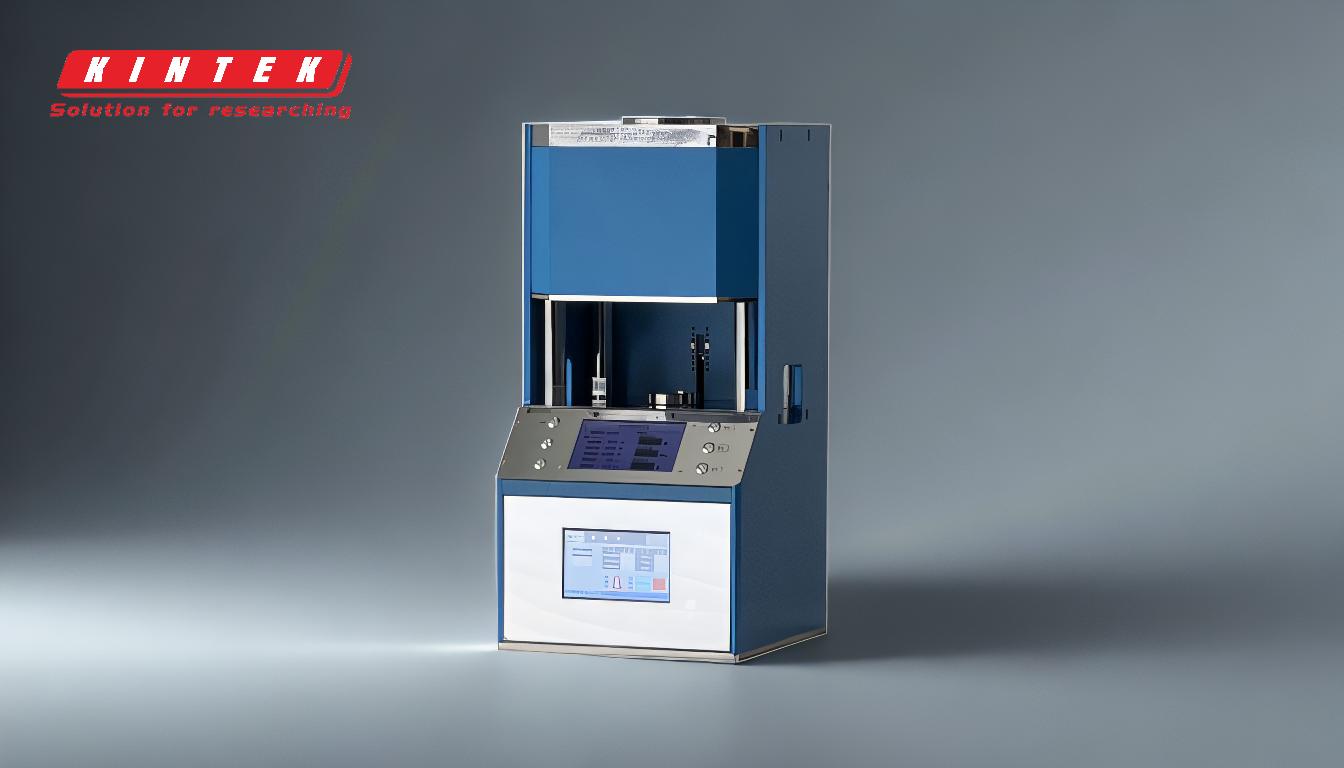
-
Mechanism of Operation:
- Manual Press: Operated by hand, typically using a lever or screw mechanism to apply pressure. This requires physical effort from the operator and limits the consistency and precision of the applied force.
- Hydraulic Press: Utilizes a hydraulic system, including a pump and cylinders, to generate force. This system allows for precise control over pressure and can be automated for consistent results. For example, a hydraulic hot press machine uses hydraulic power to apply heat and pressure simultaneously, making it ideal for applications like laminating or molding.
-
Force Application:
- Manual Press: The force applied depends on the operator's strength and consistency, which can vary significantly. This makes manual presses less suitable for tasks requiring high precision or repeatability.
- Hydraulic Press: Provides consistent and repeatable force application, as the hydraulic system can be calibrated to deliver specific pressures. This is particularly important in industrial applications where uniformity is critical.
-
Ease of Use:
- Manual Press: Requires significant physical effort, especially for tasks involving high pressure or repetitive operations. This can lead to operator fatigue and reduced efficiency over time.
- Hydraulic Press: Reduces the physical burden on the operator, as the hydraulic system does the heavy lifting. Automated hydraulic presses further enhance ease of use by allowing pre-programmed pressure and time settings.
-
Cost and Maintenance:
- Manual Press: Generally more affordable upfront due to its simpler design and lack of electronic components. However, it may require more frequent maintenance if used intensively, and the physical strain on operators can lead to higher long-term costs.
- Hydraulic Press: Typically more expensive initially because of its complex hydraulic system and potential automation features. However, it often requires less physical maintenance and can improve workflow efficiency, offsetting the initial investment.
-
Applications:
- Manual Press: Suitable for small-scale or low-precision tasks, such as simple assembly, pressing bearings, or light-duty forming. It is often used in workshops or small manufacturing setups where cost is a primary concern.
- Hydraulic Press: Ideal for high-precision and high-force applications, such as metal forming, laminating, and industrial molding. Its ability to deliver consistent pressure makes it indispensable in industries like automotive, aerospace, and electronics.
-
Automation Potential:
- Manual Press: Limited to manual operation, making it less adaptable to modern automated workflows. This can be a disadvantage in industries where automation is critical for productivity.
- Hydraulic Press: Can be easily integrated into automated systems, allowing for programmable pressure cycles, timing, and other parameters. This makes it a versatile choice for high-volume production environments.
-
Safety Considerations:
- Manual Press: Requires careful handling to avoid operator injury, especially when applying high force. The lack of automated controls increases the risk of human error.
- Hydraulic Press: Often includes safety features such as pressure relief valves and emergency stop buttons, reducing the risk of accidents. Automated systems further enhance safety by minimizing direct operator involvement.
In summary, while manual presses are cost-effective and suitable for simpler tasks, hydraulic presses offer superior precision, consistency, and ease of use, making them the preferred choice for demanding industrial applications. The decision between the two should be based on the specific needs of the task, including the required force, accuracy, and workflow efficiency.
Summary Table:
Aspect | Manual Press | Hydraulic Press |
---|---|---|
Mechanism of Operation | Operated by hand using a lever or screw mechanism. Requires physical effort. | Uses a hydraulic system (pump and cylinders) for precise, automated force control. |
Force Application | Depends on operator strength; less consistent and precise. | Delivers consistent, repeatable force with calibration options. |
Ease of Use | Labor-intensive; prone to operator fatigue. | Reduces physical effort; can be automated for ease of use. |
Cost and Maintenance | Lower upfront cost but higher long-term maintenance and labor costs. | Higher initial cost but lower maintenance and improved efficiency. |
Applications | Suitable for small-scale, low-precision tasks like assembly or light-duty forming. | Ideal for high-precision, high-force tasks like metal forming and industrial molding. |
Automation Potential | Limited to manual operation. | Easily integrated into automated systems for high-volume production. |
Safety Considerations | Higher risk of operator injury due to manual handling. | Includes safety features like pressure relief valves and emergency stops. |
Need help choosing the right press for your application? Contact our experts today to find the perfect solution!