The difference between a retort furnace and a muffle furnace primarily lies in their design, functionality, and applications. A retort furnace refers to an airtight vessel used for processing materials, often in chemical or industrial settings, while a muffle furnace is designed to heat materials indirectly by isolating them from the heating elements. Both are used for high-temperature applications, but their specific uses, temperature ranges, and structural features differ significantly. A retort furnace is ideal for processes requiring controlled atmospheres, whereas a muffle furnace excels in applications like annealing, incineration, and material testing.
Key Points Explained:
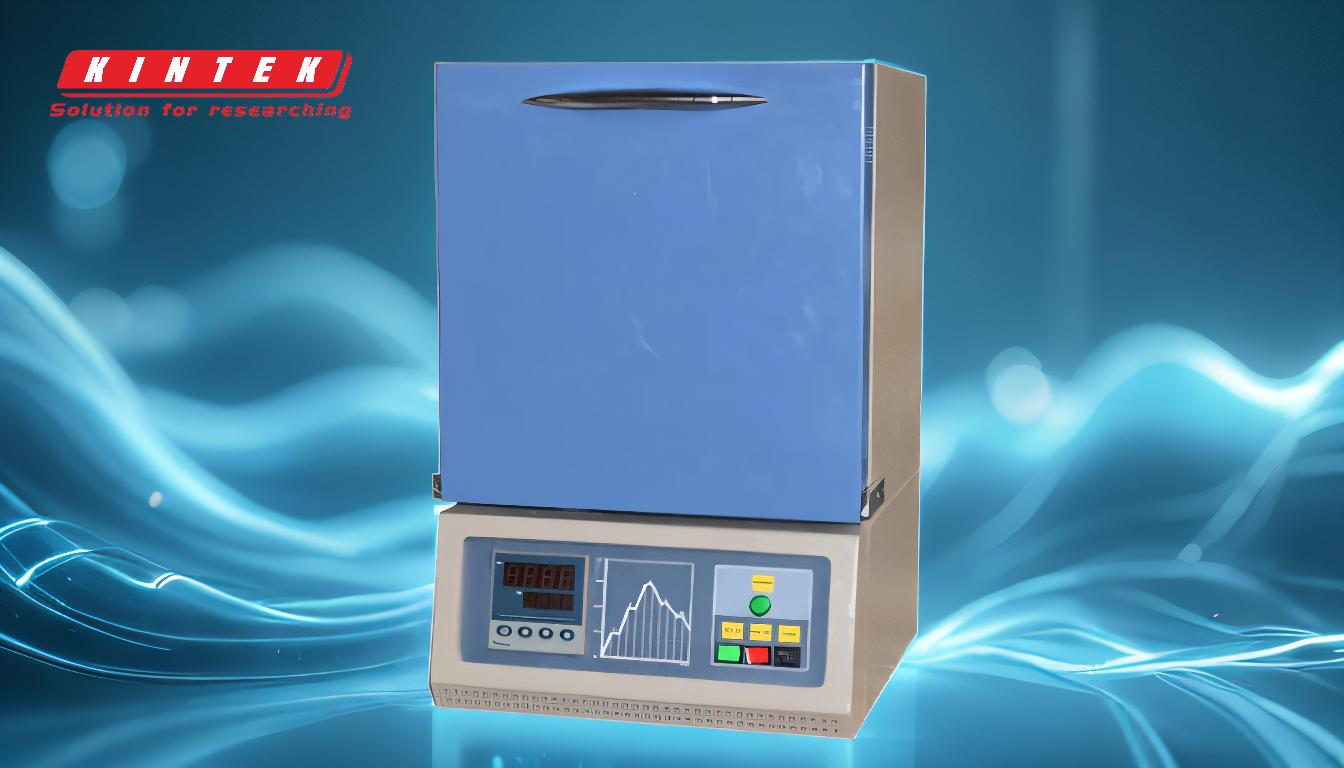
-
Definition and Design:
- Retort Furnace: A retort furnace is characterized by an airtight vessel or chamber where materials are processed. This design is particularly useful in chemical processes where controlled atmospheres or specific gases are required. The retort ensures that the material is isolated from external contaminants and allows for precise control over the processing environment.
- Muffle Furnace: A muffle furnace, on the other hand, uses indirect heating. The heating elements are placed outside the furnace chamber, and the material is placed inside a separate chamber called a muffle, typically made of ceramic materials like alumina. This design isolates the material from direct contact with heating elements, preventing contamination and ensuring uniform heating.
-
Temperature Range:
- Retort Furnace: The temperature range of a retort furnace can vary widely depending on the application. It is often used in processes requiring moderate to high temperatures, typically up to 1200°C or more, depending on the specific design and materials used.
- Muffle Furnace: Muffle furnaces are designed to reach extremely high temperatures, often exceeding 1700°C. This makes them suitable for applications like annealing, crystal growth, and incineration, where very high temperatures are necessary.
-
Applications:
- Retort Furnace: Retort furnaces are commonly used in industries requiring controlled atmospheres, such as chemical processing, metallurgy, and heat treatment. They are ideal for processes like carburizing, sintering, and brazing, where precise control over the atmosphere is crucial.
- Muffle Furnace: Muffle furnaces are widely used in laboratories and industrial settings for applications such as material testing, thermal treatments, and the destruction of organic and plastic elements. They are also used in the production of ceramics, metals, and glass.
-
Heating Mechanism:
- Retort Furnace: In a retort furnace, the heating mechanism can be direct or indirect, depending on the design. The primary feature is the airtight retort, which allows for controlled atmospheres and prevents contamination.
- Muffle Furnace: A muffle furnace uses indirect heating, where the heating elements are placed outside the muffle chamber. This design ensures that the material is heated uniformly and prevents contamination from the heating elements.
-
Advantages and Limitations:
- Retort Furnace: The main advantage of a retort furnace is its ability to provide a controlled atmosphere, making it ideal for processes requiring specific gases or environments. However, it may be more complex and expensive to operate due to the need for airtight seals and controlled gas flows.
- Muffle Furnace: Muffle furnaces are simpler in design and easier to operate, making them suitable for a wide range of high-temperature applications. However, they are limited to air calcination and cannot control the atmosphere within the chamber.
-
Cost and Maintenance:
- Retort Furnace: Retort furnaces are generally more expensive due to their complex design and the need for airtight seals and controlled atmospheres. Maintenance can also be more demanding, requiring regular checks on seals and gas flow systems.
- Muffle Furnace: Muffle furnaces are typically more affordable and easier to maintain. The primary maintenance tasks involve checking the heating elements and ensuring the muffle chamber is free from contaminants.
In summary, while both retort and muffle furnaces are used for high-temperature processes, they serve different purposes and have distinct designs. A retort furnace is ideal for controlled atmosphere processes, whereas a muffle furnace excels in applications requiring high temperatures and isolation from contaminants. Understanding these differences can help in selecting the right furnace for specific industrial or laboratory needs.
Summary Table:
Feature | Retort Furnace | Muffle Furnace |
---|---|---|
Design | Airtight vessel for controlled atmospheres | Indirect heating with material isolated from heating elements |
Temperature Range | Up to 1200°C or more | Exceeds 1700°C |
Applications | Chemical processing, metallurgy, heat treatment (e.g., carburizing, sintering) | Annealing, incineration, material testing, ceramics, and glass production |
Heating Mechanism | Direct or indirect heating with airtight retort | Indirect heating with external heating elements |
Advantages | Controlled atmosphere, precise environmental control | Uniform heating, contamination-free, simpler design |
Limitations | Complex and expensive, requires airtight seals and gas flow control | Limited to air calcination, no controlled atmosphere |
Cost & Maintenance | Higher cost, more demanding maintenance | More affordable, easier maintenance |
Need help choosing the right furnace for your needs? Contact our experts today for personalized advice!