Sintering and casting are two distinct manufacturing processes used to form solid metal parts, each with unique characteristics and applications. Sintering involves compacting powdered materials and applying heat below the melting point to bond particles through atomic diffusion, resulting in a solid structure with improved mechanical properties. This process is energy-efficient and allows for precise control over the final product's properties. In contrast, casting involves melting metal to a liquid state and pouring it into a mold, where it solidifies into the desired shape. Casting can produce complex geometries but often requires higher energy and may introduce imperfections like porosity.
Key Points Explained:
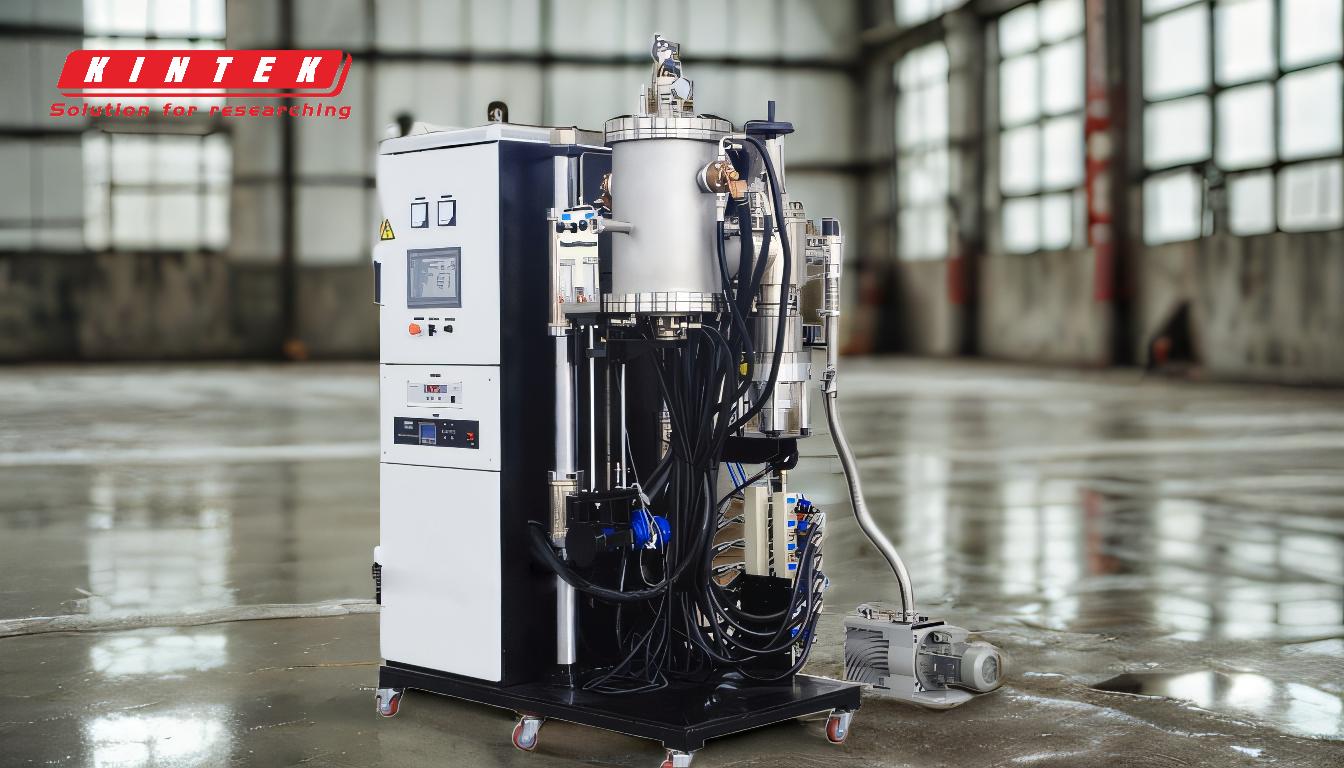
-
Definition and Process:
- Sintering: A process where powdered materials are compacted and heated below their melting point. The heat causes atoms to diffuse across particle boundaries, bonding them together and densifying the material into a solid structure.
- Casting: A process where metal is heated to its melting point, turning it into a liquid, which is then poured into a mold. The liquid metal solidifies within the mold, taking its shape.
-
Temperature Requirements:
- Sintering: Operates at temperatures below the melting point of the material, making it more energy-efficient.
- Casting: Requires temperatures high enough to completely melt the metal, consuming more energy.
-
Mechanical Properties:
- Sintering: Produces parts with consistent and improved mechanical properties due to controlled bonding and densification.
- Casting: Can result in parts with imperfections like porosity and internal stresses, which may affect mechanical properties.
-
Complexity and Precision:
- Sintering: Allows for precise control over the final product's properties and can produce complex shapes with high accuracy.
- Casting: Suitable for creating complex geometries but may require additional machining to achieve precise dimensions and surface finishes.
-
Applications:
- Sintering: Commonly used in the production of components requiring high precision and consistency, such as gears, bearings, and filters.
- Casting: Widely used for large or complex parts, such as engine blocks, turbine blades, and artistic sculptures.
-
Energy Efficiency:
- Sintering: More energy-efficient due to lower operating temperatures.
- Casting: Less energy-efficient due to the need for high temperatures to melt the metal.
-
Material Utilization:
- Sintering: Efficient use of materials with minimal waste, as the process starts with powdered metals.
- Casting: May result in more material waste, especially if additional machining is required.
Understanding these differences helps in selecting the appropriate manufacturing process based on the desired properties, complexity, and application of the final product.
Summary Table:
Aspect | Sintering | Casting |
---|---|---|
Process | Compact powdered materials, heat below melting point for bonding. | Melt metal to liquid, pour into mold, and solidify. |
Temperature | Below melting point, energy-efficient. | Above melting point, higher energy consumption. |
Mechanical Properties | Consistent and improved properties due to controlled bonding. | May have imperfections like porosity or internal stresses. |
Complexity & Precision | High precision, suitable for complex shapes. | Suitable for complex geometries but may require additional machining. |
Applications | Gears, bearings, filters (high precision). | Engine blocks, turbine blades, sculptures (large/complex parts). |
Energy Efficiency | More energy-efficient. | Less energy-efficient. |
Material Utilization | Minimal waste, efficient use of powdered metals. | May result in more material waste. |
Need help choosing between sintering and casting for your project? Contact our experts today for personalized advice!