Coreless and cored induction furnaces are both used for melting metals, but they differ significantly in design, operation, and application. Coreless induction furnaces rely on a water-cooled copper coil to induce currents directly into the metal charge, offering precise temperature control, even heat distribution, and flexibility for alloy changes. However, they have lower power efficiency (around 75%) and may require frequent refractory lining replacements. Cored induction furnaces, on the other hand, use a magnetic core to enhance efficiency and are better suited for continuous operations with fewer alloy changes. The choice between the two depends on specific operational needs, such as power efficiency, alloy flexibility, and maintenance requirements.
Key Points Explained:
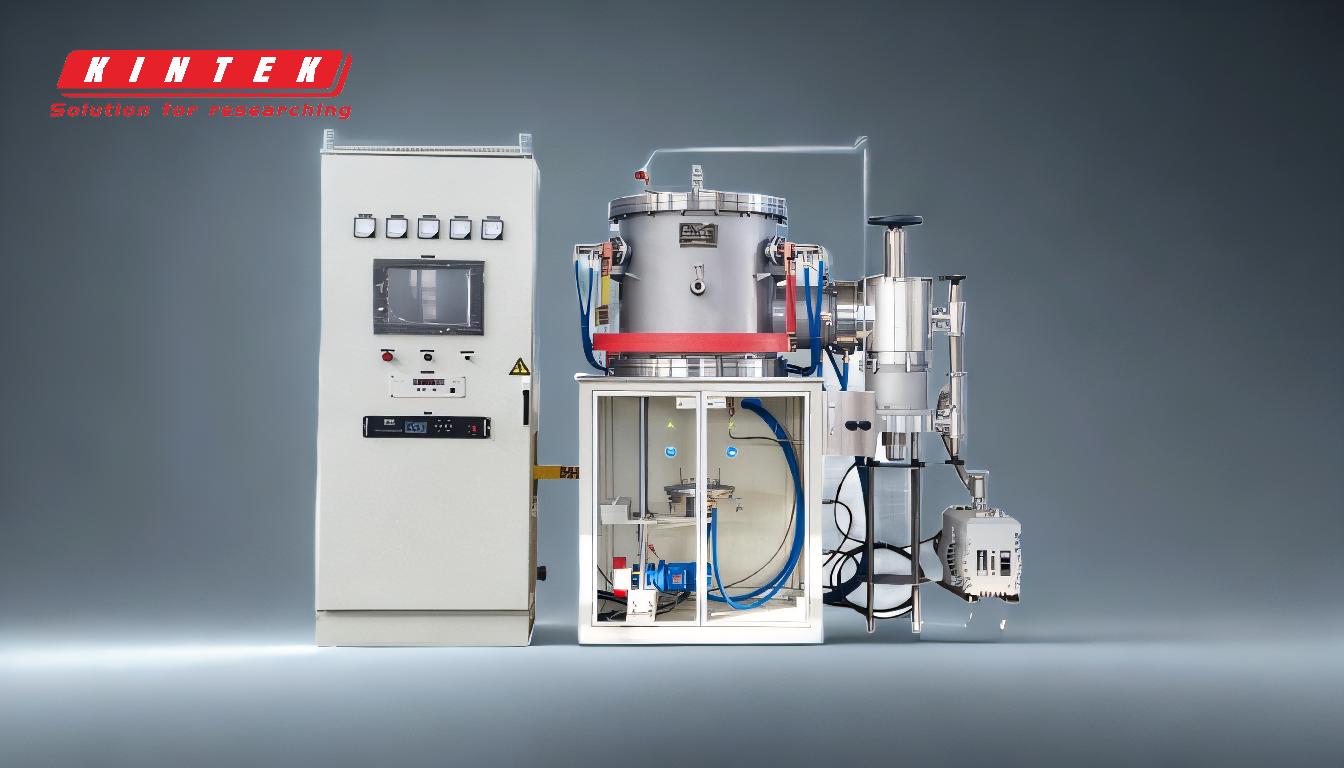
-
Design and Construction:
-
Coreless Induction Furnace:
- The primary component is a water-cooled copper coil wound into a helical shape, housed within a steel shell.
- The coil induces currents directly into the metal charge, eliminating the need for a secondary coil or magnetic core.
- The steel shell is magnetically shielded to prevent heating and is supported on trunnions for easy pouring.
-
Cored Induction Furnace:
- Features a magnetic core (typically iron) that enhances the magnetic flux and improves energy efficiency.
- The core acts as a secondary circuit, allowing for higher power efficiency compared to coreless designs.
- The design is more complex and suited for continuous operations with fewer alloy changes.
-
Coreless Induction Furnace:
-
Operation and Efficiency:
-
Coreless Induction Furnace:
- Operates by transformer action without a secondary coil, inducing currents directly into the metal charge.
- Offers precise control over temperature and metal chemistry, making it ideal for melting various grades of steel, iron, and non-ferrous alloys.
- Lower power efficiency (approximately 75%) due to the absence of a magnetic core.
- Can be shut down and started cold, simplifying alloy changes but reducing refractory lining life.
-
Cored Induction Furnace:
- Utilizes a magnetic core to enhance efficiency, achieving higher power efficiency compared to coreless furnaces.
- Better suited for continuous operations with fewer alloy changes, as frequent changes can damage the core.
- Less flexible for alloy changes but more energy-efficient for consistent production runs.
-
Coreless Induction Furnace:
-
Applications and Flexibility:
-
Coreless Induction Furnace:
- Ideal for applications requiring frequent alloy changes, such as foundries producing small batches of different alloys.
- Provides even heat distribution and precise temperature control, making it suitable for re-melting and refining processes.
- Commonly used for melting steel, iron, and non-ferrous alloys.
-
Cored Induction Furnace:
- Better suited for continuous operations with fewer alloy changes, such as large-scale production of a single alloy.
- Higher efficiency makes it cost-effective for consistent, high-volume production.
- Less flexibility for alloy changes but more efficient for specific, long-term applications.
-
Coreless Induction Furnace:
-
Maintenance and Lifespan:
-
Coreless Induction Furnace:
- Frequent alloy changes and thermal cycling can reduce the lifespan of the refractory lining.
- Requires regular maintenance to replace the refractory lining and ensure proper cooling of the coil.
- Lower power efficiency may lead to higher operational costs over time.
-
Cored Induction Furnace:
- Fewer alloy changes and continuous operation reduce wear on the refractory lining and core.
- Higher power efficiency reduces operational costs, but the magnetic core may require periodic maintenance.
- Longer lifespan for refractory linings and cores in continuous operation scenarios.
-
Coreless Induction Furnace:
-
Frequency Range and Control:
-
Coreless Induction Furnace:
- Operates across a wide frequency range (50 Hz to 10 kHz), allowing for flexibility in melting different metals and alloys.
- Provides precise control over temperature and metal chemistry, making it suitable for specialized applications.
-
Cored Induction Furnace:
- Typically operates at lower frequencies, optimized for specific alloys and continuous production.
- Less flexible in terms of frequency range but more efficient for targeted applications.
-
Coreless Induction Furnace:
In summary, the choice between coreless and cored induction furnaces depends on specific operational needs, such as the frequency of alloy changes, required power efficiency, and maintenance considerations. Coreless furnaces offer greater flexibility and control, while cored furnaces provide higher efficiency and are better suited for continuous operations.
Summary Table:
Feature | Coreless Induction Furnace | Cored Induction Furnace |
---|---|---|
Design | Water-cooled copper coil, no magnetic core | Magnetic core for enhanced efficiency |
Efficiency | ~75% power efficiency | Higher power efficiency |
Applications | Frequent alloy changes, small batches | Continuous operations, single alloy |
Maintenance | Frequent refractory lining replacements | Less frequent maintenance, longer lifespan |
Frequency Range | 50 Hz to 10 kHz | Lower frequencies, optimized for specific alloys |
Still unsure which induction furnace is right for your operation? Contact our experts today for personalized advice!