DC and RF magnetron sputtering are two widely used techniques in thin-film deposition, each with distinct characteristics, advantages, and applications. DC sputtering uses a direct current power source and is primarily suited for conductive materials, offering high deposition rates and cost-efficiency for large substrates. RF sputtering, on the other hand, employs an alternating current power source, typically at 13.56 MHz, making it suitable for both conductive and non-conductive materials, especially dielectric targets. While RF sputtering has a lower deposition rate and higher operational costs, it avoids issues like charge accumulation and arcing, which are common in DC sputtering when used with non-conductive materials. Both methods leverage magnetic fields to enhance plasma generation and deposition efficiency, but their differences in power supply and material compatibility make them suitable for different applications.
Key Points Explained:
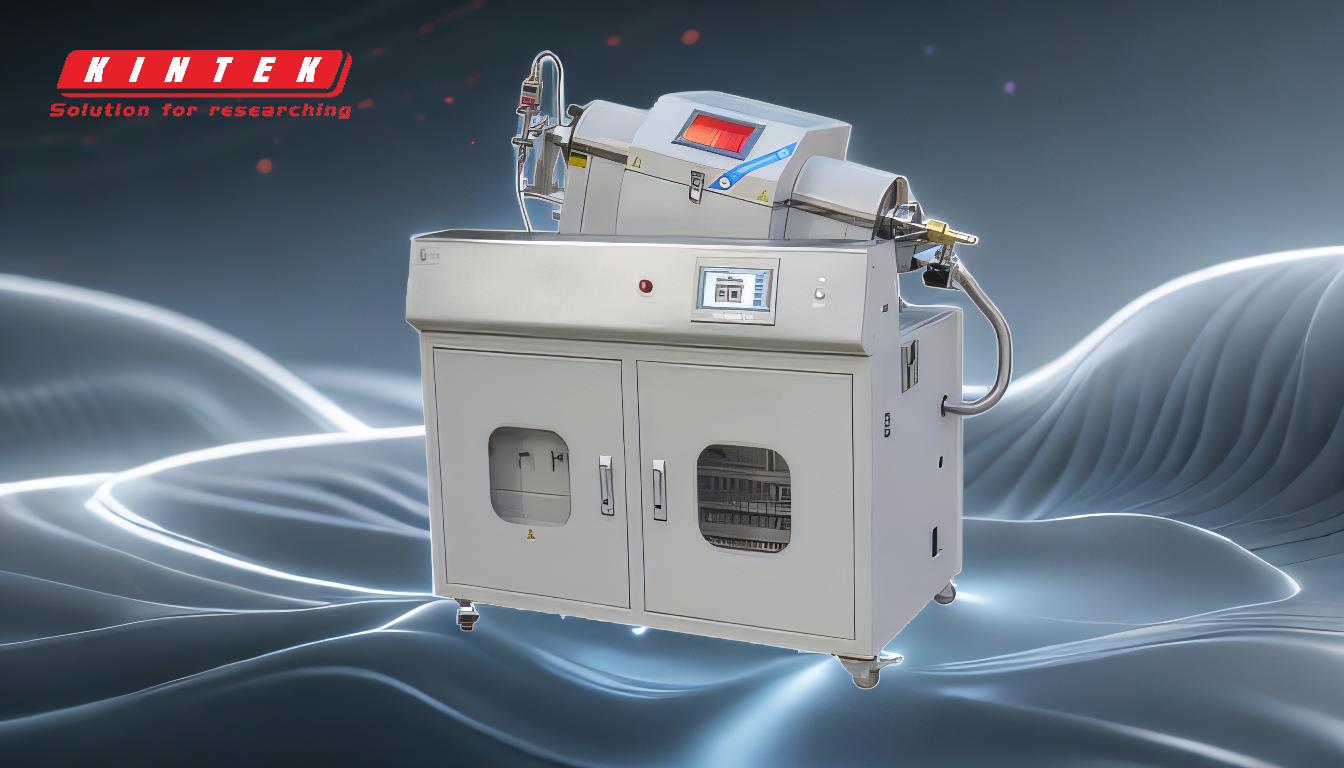
-
Power Source and Plasma Generation:
- DC Magnetron Sputtering: Uses a direct current (DC) power source to generate plasma in a low-pressure gas environment. The positively charged gas ions are accelerated toward the negatively charged target, causing sputtering of the target material.
- RF Magnetron Sputtering: Utilizes an alternating current (AC) power source, typically at 13.56 MHz, to generate plasma. The alternating charge prevents charge accumulation on the target, making it suitable for both conductive and non-conductive materials.
-
Material Compatibility:
- DC Magnetron Sputtering: Best suited for conductive materials like pure metals (e.g., Iron, Copper, Nickel). It is not ideal for dielectric materials due to charge accumulation and arcing issues.
- RF Magnetron Sputtering: Suitable for both conductive and non-conductive materials, especially dielectric targets. The alternating charge prevents charge buildup, making it effective for insulating materials.
-
Deposition Rate and Efficiency:
- DC Magnetron Sputtering: Offers high deposition rates, making it efficient for large substrates and industrial applications. It is cost-effective for conductive materials.
- RF Magnetron Sputtering: Has a lower deposition rate compared to DC sputtering. However, it provides better control and uniformity for smaller substrates and complex materials.
-
Operational Costs and Applications:
- DC Magnetron Sputtering: Lower operational costs and simpler setup make it ideal for large-scale production of conductive films. It is widely used in industries requiring high throughput.
- RF Magnetron Sputtering: Higher operational costs due to the complexity of the RF power supply. It is preferred for applications requiring precise control over film properties, such as in semiconductor and optical coatings.
-
Charge Accumulation and Arcing:
- DC Magnetron Sputtering: Prone to charge accumulation and arcing when used with dielectric materials, which can damage the power supply and the film.
- RF Magnetron Sputtering: The alternating charge prevents charge accumulation, eliminating arcing issues and making it suitable for dielectric materials.
-
Magnetic Field Utilization:
- Both DC and RF magnetron sputtering use magnetic fields to trap electrons near the target surface, enhancing plasma generation and deposition efficiency. This magnetic confinement allows for higher current at lower gas pressures, improving the overall deposition process.
-
Film Quality and Control:
- DC Magnetron Sputtering: Produces films with high purity, good compactness, and uniform thickness, especially for conductive materials. It is easy to industrialize for large-area substrates.
- RF Magnetron Sputtering: Offers better control over film properties, such as particle size and uniformity, making it suitable for high-precision applications. It is ideal for depositing complex materials like alloys and oxides.
In summary, the choice between DC and RF magnetron sputtering depends on the specific requirements of the application, including the type of material to be deposited, desired deposition rate, and film quality. DC sputtering is more cost-effective and efficient for conductive materials, while RF sputtering provides greater flexibility and control for both conductive and non-conductive materials, albeit at a higher cost.
Summary Table:
Aspect | DC Magnetron Sputtering | RF Magnetron Sputtering |
---|---|---|
Power Source | Direct Current (DC) | Alternating Current (AC) at 13.56 MHz |
Material Compatibility | Best for conductive materials (e.g., metals) | Suitable for both conductive and non-conductive materials (e.g., dielectrics) |
Deposition Rate | High deposition rate, ideal for large substrates | Lower deposition rate, better for smaller substrates and complex materials |
Operational Costs | Lower costs, simpler setup | Higher costs due to RF power supply complexity |
Charge Accumulation | Prone to charge buildup and arcing with non-conductive materials | Prevents charge buildup, no arcing issues |
Applications | Large-scale production of conductive films | High-precision applications like semiconductor and optical coatings |
Film Quality | High purity, uniform thickness for conductive materials | Better control over film properties, ideal for alloys and oxides |
Still unsure which sputtering method is right for your application? Contact our experts today for personalized guidance!