Epitaxy and Atomic Layer Deposition (ALD) are both advanced thin-film deposition techniques used in semiconductor manufacturing and material science, but they differ significantly in their principles, processes, and applications. Epitaxy involves the growth of a crystalline layer on a crystalline substrate, where the new layer mimics the atomic arrangement of the substrate. This technique is crucial for creating high-quality semiconductor materials with precise lattice matching. On the other hand, ALD is a precise layer-by-layer deposition method that uses sequential, self-limiting chemical reactions to deposit thin films with atomic-level control. ALD is known for its ability to produce highly uniform and conformal coatings, even on complex 3D structures. While epitaxy is primarily used for growing crystalline films with specific electronic properties, ALD is versatile and widely used for depositing thin films in applications requiring precise thickness control and uniformity.
Key Points Explained:
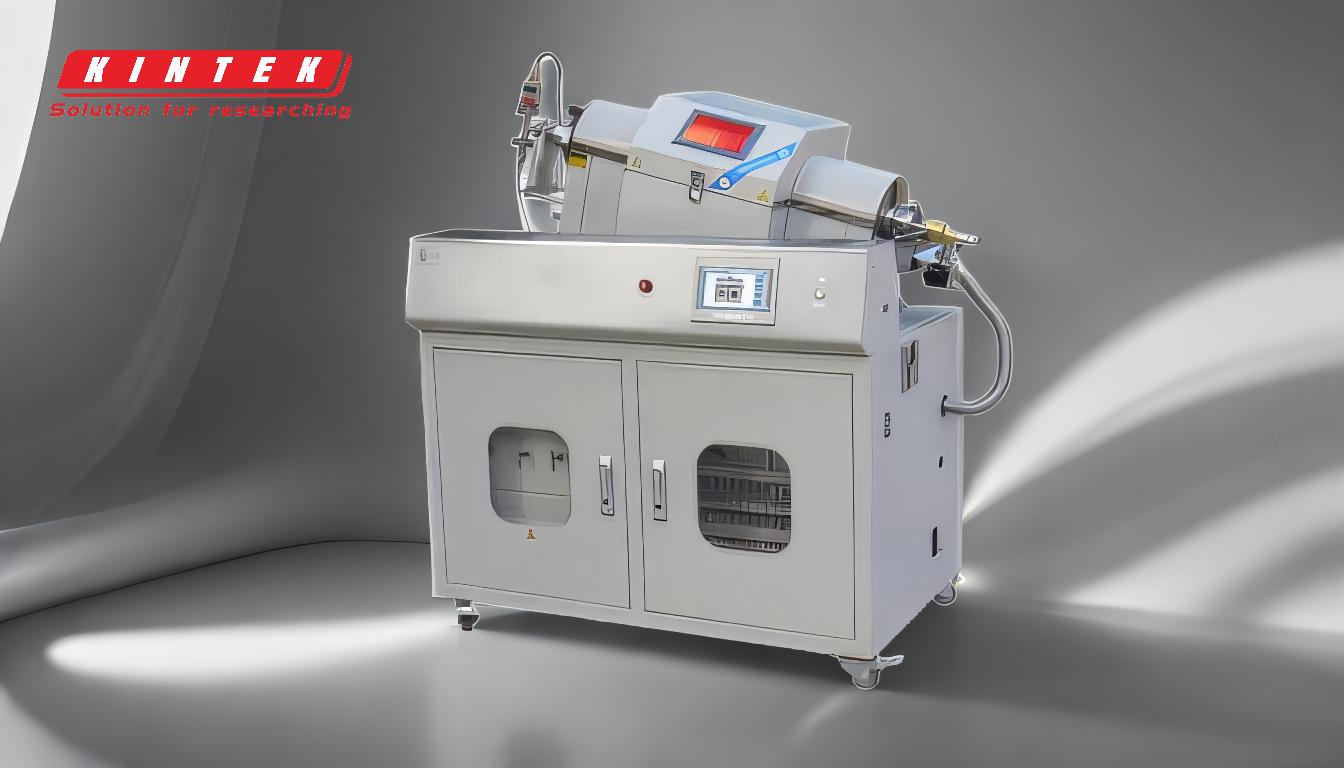
-
Definition and Purpose:
- Epitaxy: A process where a crystalline layer is grown on a crystalline substrate, maintaining the same atomic arrangement as the substrate. It is used to create high-quality semiconductor materials with specific electronic properties.
- ALD: A layer-by-layer deposition technique that uses sequential, self-limiting chemical reactions to deposit thin films with atomic-level precision. It is used for applications requiring highly uniform and conformal coatings.
-
Process Mechanism:
- Epitaxy: Involves the deposition of atoms onto a substrate in a way that they align with the substrate's crystal structure. This can be done using techniques like Molecular Beam Epitaxy (MBE) or Chemical Vapor Deposition (CVD).
- ALD: Uses two precursor materials that are introduced into the reaction chamber sequentially. Each precursor reacts with the surface in a self-limiting manner, ensuring precise control over film thickness and uniformity.
-
Temperature Requirements:
- Epitaxy: Typically requires high temperatures to ensure proper crystalline growth and lattice matching.
- ALD: Operates at lower, controlled temperatures, making it suitable for a wider range of substrates and applications.
-
Uniformity and Conformality:
- Epitaxy: Produces highly crystalline films with excellent electronic properties but may struggle with uniformity on complex 3D structures.
- ALD: Known for its ability to deposit highly uniform and conformal films, even on intricate 3D surfaces, due to its layer-by-layer approach.
-
Applications:
- Epitaxy: Primarily used in the semiconductor industry for growing high-quality crystalline films, such as those used in LEDs, lasers, and high-speed transistors.
- ALD: Used in a variety of applications, including semiconductor manufacturing, MEMS, solar cells, and protective coatings, where precise thickness control and uniformity are critical.
-
Material Compatibility:
- Epitaxy: Limited to materials that can form crystalline structures and match the lattice parameters of the substrate.
- ALD: Can deposit a wide range of materials, including metals, oxides, and nitrides, making it more versatile for different applications.
-
Precision and Control:
- Epitaxy: Offers precise control over the crystalline quality and electronic properties of the deposited film.
- ALD: Provides atomic-level control over film thickness and uniformity, making it ideal for applications requiring nanometer-scale precision.
-
Complexity and Cost:
- Epitaxy: Generally more complex and expensive due to the need for high temperatures and precise control over crystal growth.
- ALD: While still complex, ALD can be more cost-effective for certain applications due to its lower temperature requirements and ability to deposit films on a wide range of substrates.
In summary, while both epitaxy and ALD are crucial for advanced material deposition, they serve different purposes and are chosen based on the specific requirements of the application. Epitaxy is ideal for growing high-quality crystalline films, whereas ALD excels in depositing uniform and conformal thin films with precise thickness control.
Summary Table:
Aspect | Epitaxy | Atomic Layer Deposition (ALD) |
---|---|---|
Definition | Growth of a crystalline layer on a substrate with matching atomic structure. | Layer-by-layer deposition using sequential, self-limiting chemical reactions. |
Process Mechanism | Atoms align with substrate's crystal structure (e.g., MBE, CVD). | Two precursors react sequentially for atomic-level control. |
Temperature | High temperatures required for crystalline growth. | Operates at lower, controlled temperatures. |
Uniformity | Excellent crystalline quality; less uniform on complex 3D structures. | Highly uniform and conformal, even on intricate 3D surfaces. |
Applications | LEDs, lasers, high-speed transistors. | Semiconductor manufacturing, MEMS, solar cells, protective coatings. |
Material Compatibility | Limited to crystalline materials matching substrate lattice. | Versatile: metals, oxides, nitrides, and more. |
Precision | Precise control over crystalline quality and electronic properties. | Atomic-level control over thickness and uniformity. |
Complexity & Cost | More complex and expensive due to high temperatures. | Cost-effective for certain applications due to lower temperatures and versatility. |
Need help choosing the right thin-film deposition technique? Contact our experts today for tailored solutions!