Hot pressing and compression molding are two distinct manufacturing processes used to shape materials, particularly in the production of composites, ceramics, and polymers. While both involve the application of heat and pressure, they differ significantly in their mechanisms, applications, and outcomes. Hot pressing combines pressing and sintering simultaneously, which accelerates phase changes and alloy formation, making it an activated sintering process. On the other hand, compression molding involves placing a pre-measured amount of material into a mold cavity and applying heat and pressure to shape the material. Transfer molding, a variant of compression molding, introduces the material into the mold cavity through holes, using a plunger and cylinder system.
Key Points Explained:
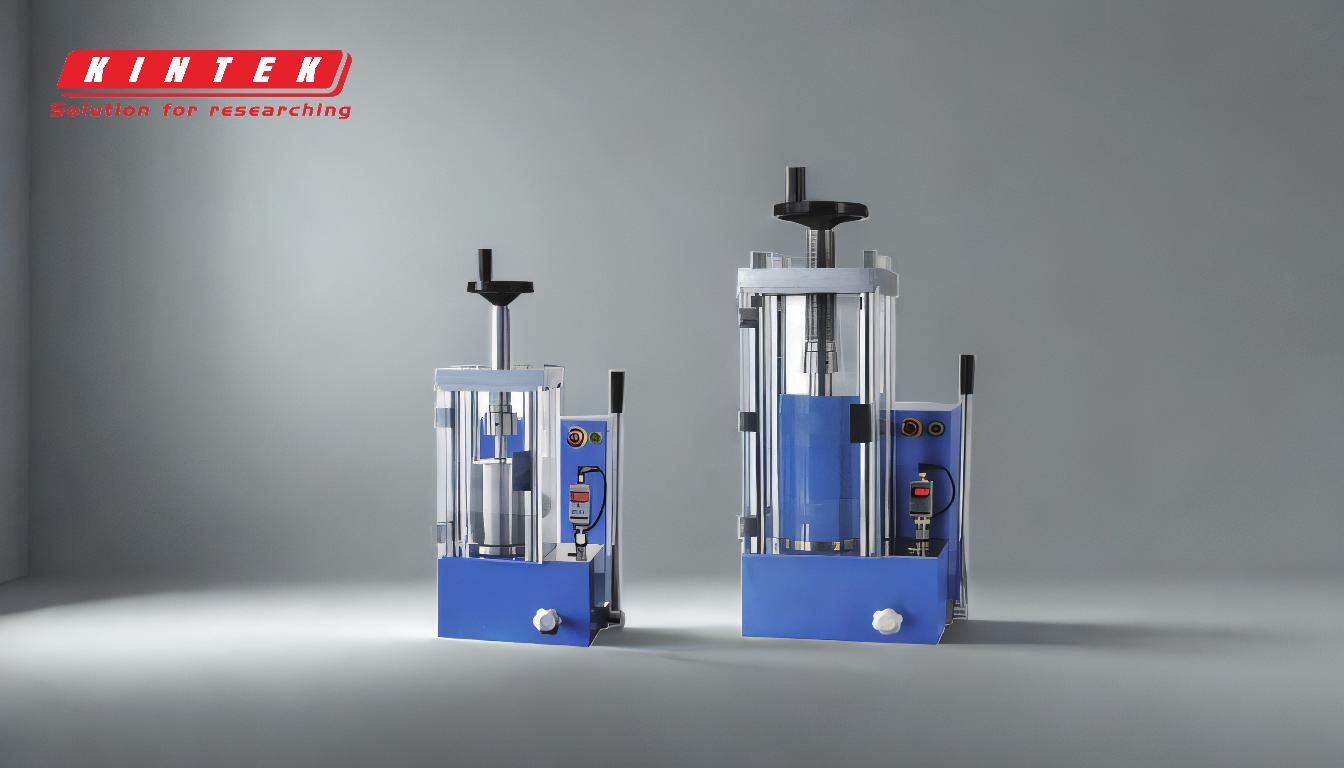
-
Mechanism of Operation:
- Hot Pressing: Hot pressing integrates the processes of pressing and sintering. The material is subjected to both high temperature and pressure simultaneously, which facilitates rapid densification and bonding. This method is particularly effective for materials that require high-density structures, such as ceramics and advanced composites.
- Compression Molding: In compression molding, a pre-measured amount of material is placed directly into a heated mold cavity. The mold is then closed, and pressure is applied to shape the material. This process is commonly used for thermosetting plastics and rubber compounds.
-
Material Flow and Filling:
- Hot Pressing: The material in hot pressing is typically in a powdered or granular form, which is compacted and sintered under heat and pressure. The process ensures uniform density and minimal porosity.
- Compression Molding: In compression molding, the material is usually in a pre-formed state, such as a sheet or billet. The material flows and fills the mold cavity under pressure, but the flow is less controlled compared to hot pressing.
-
Applications:
- Hot Pressing: This method is widely used in the production of high-performance materials, such as ceramic components, metal matrix composites, and advanced alloys. It is particularly beneficial for materials that require high strength and density.
- Compression Molding: Compression molding is commonly employed in the manufacturing of large, complex parts, such as automotive components, electrical insulators, and consumer goods. It is also used for producing rubber products like seals and gaskets.
-
Advantages and Limitations:
-
Hot Pressing:
- Advantages: High-density products, reduced processing time, and improved material properties.
- Limitations: Higher equipment costs, limited to materials that can withstand high temperatures and pressures.
-
Compression Molding:
- Advantages: Suitable for large and complex parts, cost-effective for high-volume production, and versatile in material compatibility.
- Limitations: Longer cycle times, potential for material waste, and less control over material flow compared to hot pressing.
-
Hot Pressing:
-
Transfer Molding:
- Mechanism: Transfer molding is a specialized form of compression molding where the material is transferred through holes into the mold cavity using a plunger and cylinder system. This method allows for more precise control over material placement and is particularly useful for intricate designs.
- Applications: Transfer molding is often used for encapsulating electronic components, producing intricate rubber parts, and manufacturing parts with complex geometries.
In summary, while both hot pressing and compression molding are essential techniques in material processing, they serve different purposes and are suited to different types of materials and applications. Hot pressing is ideal for high-density, high-performance materials, whereas compression molding is more versatile and cost-effective for large, complex parts. Transfer molding offers additional precision for intricate designs, making it a valuable variant of compression molding.
Summary Table:
Aspect | Hot Pressing | Compression Molding |
---|---|---|
Mechanism | Combines pressing and sintering simultaneously under high heat and pressure. | Material placed in a heated mold cavity, then shaped under pressure. |
Material Form | Powdered or granular form, compacted and sintered. | Pre-formed state (sheet or billet), flows under pressure. |
Applications | High-performance materials like ceramics, metal matrix composites, and alloys. | Large, complex parts like automotive components, rubber seals, and gaskets. |
Advantages | High-density products, reduced processing time, improved material properties. | Cost-effective for high-volume production, versatile material compatibility. |
Limitations | Higher equipment costs, limited to high-temperature/pressure materials. | Longer cycle times, potential material waste, less control over material flow. |
Need help choosing the right manufacturing process for your materials? Contact our experts today for personalized guidance!