Induction and resistance furnaces are both used for heating and melting metals, but they operate on fundamentally different principles. Induction furnaces use electromagnetic induction to generate heat directly within the metal charge, while resistance furnaces rely on electrically heated refractory elements to transfer heat to the metal. Induction furnaces are more efficient, reduce contamination, and are better suited for precise alloy compositions, whereas resistance furnaces can operate at higher temperatures and power densities but may have higher heat loss and contamination risks.
Key Points Explained:
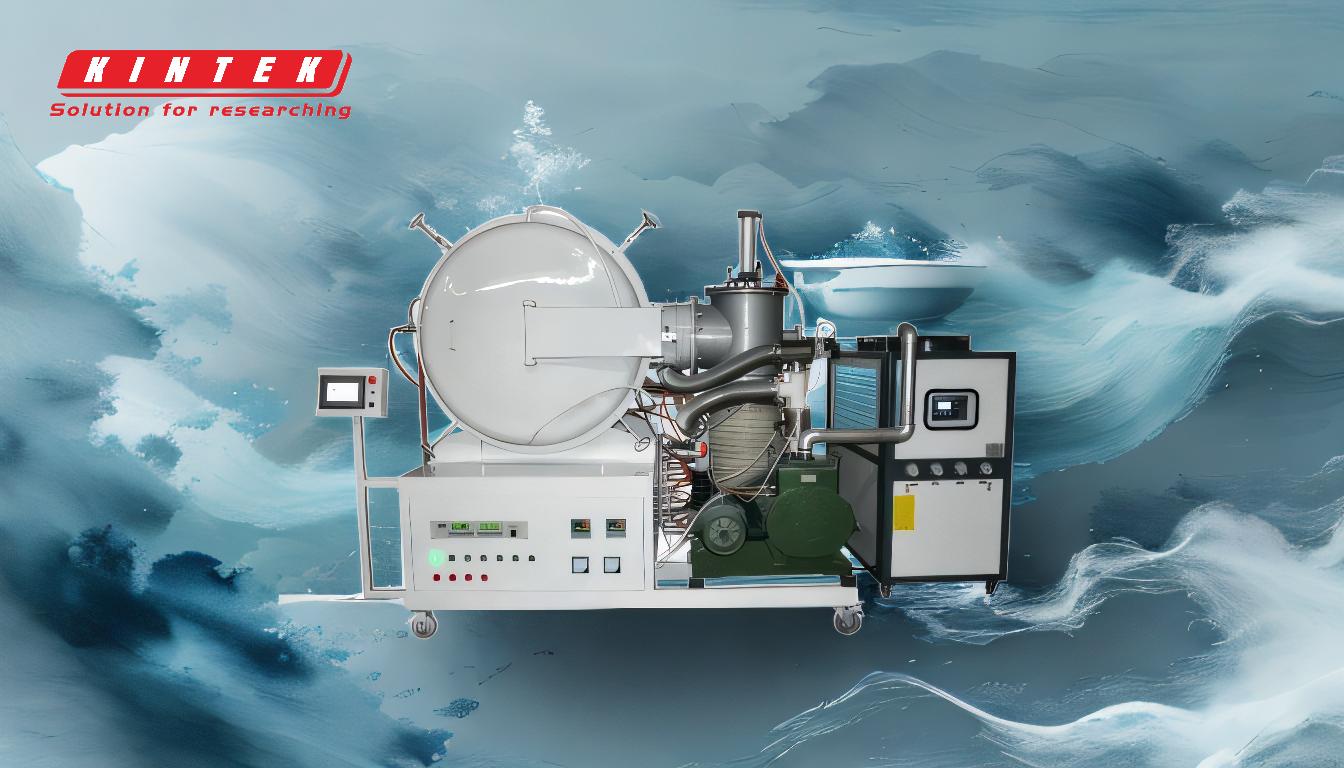
-
Heating Mechanism:
-
Induction Furnace:
- Heat is generated directly within the metal charge through electromagnetic induction. An alternating current in the furnace's coil creates a magnetic field, inducing eddy currents in the metal, which produce heat.
- This method ensures that the heat originates from the metal itself, reducing contamination and heat loss.
-
Resistance Furnace:
- Heat is generated by electrically heated refractory elements (such as coils or rods) within the furnace. This heat is then transferred to the metal charge through conduction and radiation.
- This indirect heating method can lead to higher heat loss and potential contamination from the heating elements.
-
Induction Furnace:
-
Efficiency and Contamination:
-
Induction Furnace:
- More efficient due to direct heating of the metal, minimizing heat loss.
- Reduced contamination since the metal does not come into direct contact with external heating elements.
-
Resistance Furnace:
- Less efficient because heat must be transferred from the heating elements to the metal, leading to greater heat loss.
- Higher risk of contamination from the heating elements, especially if they degrade over time.
-
Induction Furnace:
-
Temperature and Power Density:
-
Induction Furnace:
- Typically operates at lower temperatures compared to resistance furnaces.
- Limited by the ability to maintain a strong magnetic field, especially with non-magnetic materials like aluminum.
-
Resistance Furnace:
- Can achieve higher temperatures and operate at higher power densities.
- Suitable for applications requiring very high temperatures, such as sintering processes.
-
Induction Furnace:
-
Design and Complexity:
-
Induction Furnace:
- Requires careful design of the coil and magnetic yoke to ensure efficient induction, especially for non-magnetic materials.
- More complex due to the need for precise control of the electromagnetic field.
-
Resistance Furnace:
- Simpler design with electrically heated elements, making it easier to construct and maintain.
- Less complex control systems compared to induction furnaces.
-
Induction Furnace:
-
Applications:
-
Induction Furnace:
- Ideal for melting and alloying metals with precise composition control.
- Commonly used in foundries for casting and in metallurgical research.
-
Resistance Furnace:
- Suitable for high-temperature processes like sintering, annealing, and heat treatment.
- Used in industries requiring uniform high temperatures, such as ceramics and glass manufacturing.
-
Induction Furnace:
-
Material Considerations:
-
Induction Furnace:
- Effective for conductive materials, but challenges arise with non-magnetic materials like aluminum, where magnetic field divergence can occur.
- Requires careful design to manage magnetic flux leakage and ensure efficient heating.
-
Resistance Furnace:
- Can handle a wide range of materials, including non-conductive ones, as heat is generated externally.
- Less sensitive to the material's magnetic properties, making it versatile for various industrial applications.
-
Induction Furnace:
In summary, the choice between an induction furnace and a resistance furnace depends on the specific requirements of the application, including the type of material, desired temperature, efficiency, and contamination concerns. Induction furnaces offer advantages in efficiency and contamination control, while resistance furnaces provide higher temperature capabilities and simpler design.
Summary Table:
Feature | Induction Furnace | Resistance Furnace |
---|---|---|
Heating Mechanism | Direct heating via electromagnetic induction in the metal charge. | Indirect heating via electrically heated refractory elements. |
Efficiency | Higher efficiency due to direct heating, reducing heat loss. | Lower efficiency due to heat transfer losses. |
Contamination Risk | Lower risk as metal doesn’t contact external heating elements. | Higher risk due to potential contamination from heating elements. |
Temperature Range | Lower temperatures, limited by magnetic field strength. | Higher temperatures, suitable for sintering and high-temperature processes. |
Design Complexity | More complex due to precise electromagnetic field control. | Simpler design with electrically heated elements. |
Applications | Ideal for precise alloy melting, foundries, and metallurgical research. | Suitable for sintering, annealing, and high-temperature industrial processes. |
Material Suitability | Best for conductive materials; challenges with non-magnetic materials like aluminum. | Versatile, works with conductive and non-conductive materials. |
Still unsure which furnace is right for your needs? Contact our experts today for personalized advice!