Sintering is a critical process in powder metallurgy and ceramics, where powdered materials are heated to form a solid mass without melting. The two primary types of sintering are liquid-phase sintering and solid-phase sintering. Liquid-phase sintering involves the addition of a low-melting-point material that melts during the process, aiding particle rearrangement and bonding, and reducing the required sintering temperature. This method is particularly useful for materials that are difficult to sinter. In contrast, solid-phase sintering occurs entirely in the solid state, where particles bond through diffusion without any liquid phase. The choice between these methods depends on the material properties and desired outcomes.
Key Points Explained:
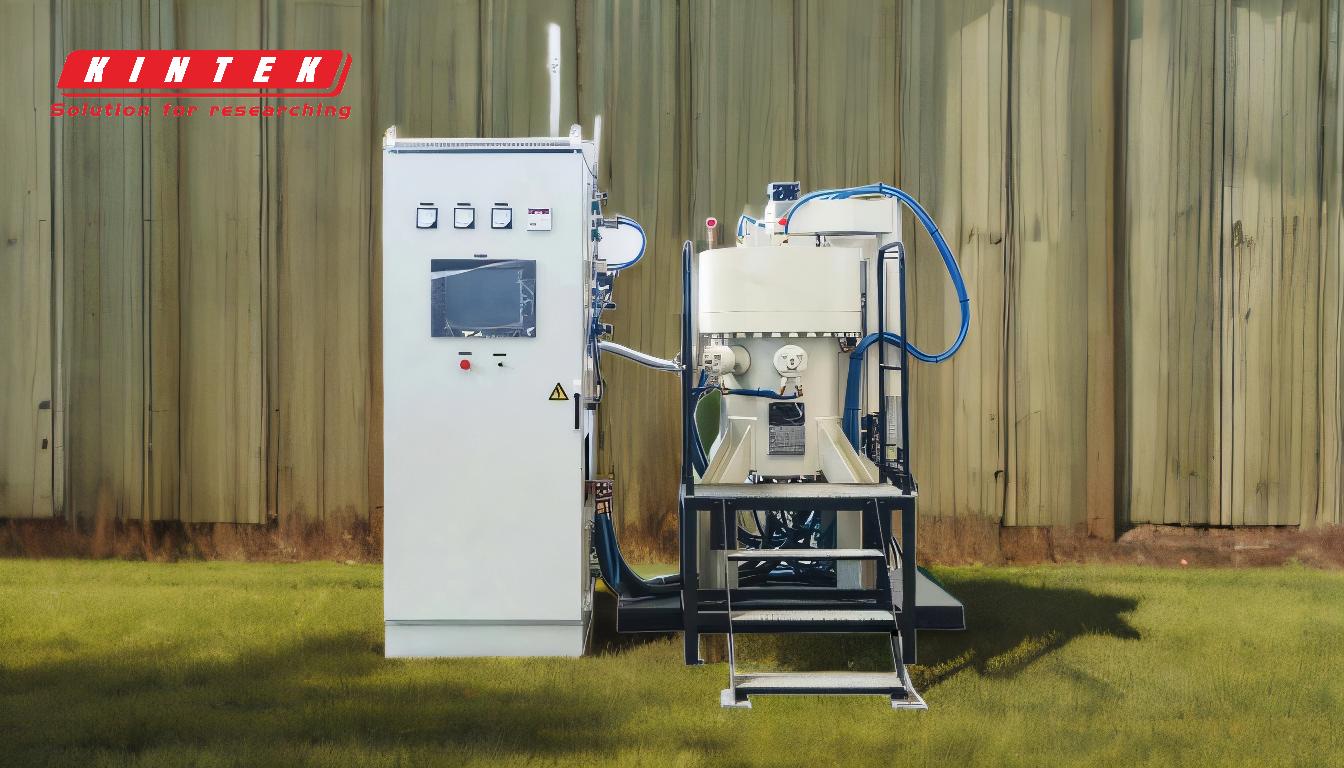
-
Definition and Mechanism:
- Liquid-Phase Sintering: This process involves adding a low-melting-point material to the powder. During heating, this additive melts, forming a liquid phase that aids in particle rearrangement and bonding. The liquid phase acts as a binder or flux, reducing the required sintering temperature and enhancing densification. This method is particularly useful for materials that are difficult to sinter.
- Solid-Phase Sintering: In this process, the powder compact is densified entirely in the solid state at the sintering temperature. No liquid phase is present; instead, particles bond through solid-state diffusion mechanisms. This method is typically used for materials that can achieve sufficient densification without the need for a liquid phase.
-
Temperature Requirements:
- Liquid-Phase Sintering: The presence of a liquid phase significantly lowers the sintering temperature, making the process more energy-efficient. The liquid phase facilitates faster particle rearrangement and bonding, which can be beneficial for materials that require lower processing temperatures.
- Solid-Phase Sintering: This method generally requires higher temperatures compared to liquid-phase sintering because the particles must bond through solid-state diffusion, which is a slower process and often requires more thermal energy.
-
Material Suitability:
- Liquid-Phase Sintering: Ideal for materials that are difficult to sinter or require enhanced densification. The liquid phase helps in filling pores and rearranging grains, leading to a more favorable packing arrangement.
- Solid-Phase Sintering: Suitable for materials that can achieve sufficient densification through solid-state diffusion alone. This method is often used for materials that do not require the additional benefits provided by a liquid phase.
-
Process Efficiency:
- Liquid-Phase Sintering: The process is generally more efficient due to the lower sintering temperatures and faster densification rates. The liquid phase aids in faster particle rearrangement and bonding, leading to quicker processing times.
- Solid-Phase Sintering: While it may require higher temperatures and longer processing times, this method can be more straightforward and less complex, as it does not involve managing a liquid phase.
-
Applications:
- Liquid-Phase Sintering: Commonly used in the production of ceramics, cemented carbides, and certain metal alloys where enhanced densification and lower processing temperatures are beneficial.
- Solid-Phase Sintering: Typically used for metals and ceramics that can achieve the desired density and properties through solid-state diffusion alone.
-
Equipment Considerations:
- Liquid-Phase Sintering: The process may require specialized sintering furnaces capable of precise temperature control to manage the liquid phase effectively.
- Solid-Phase Sintering: Standard sintering furnaces are usually sufficient, as the process does not involve a liquid phase and can be conducted at higher temperatures without the need for precise liquid phase management.
In summary, the choice between liquid-phase and solid-phase sintering depends on the material properties, desired outcomes, and processing constraints. Liquid-phase sintering offers advantages in terms of lower temperatures and faster densification, while solid-phase sintering is more straightforward and suitable for materials that can achieve sufficient densification through solid-state diffusion.
Summary Table:
Aspect | Liquid-Phase Sintering | Solid-Phase Sintering |
---|---|---|
Definition | Involves a low-melting-point material that melts, aiding particle rearrangement and bonding. | Occurs entirely in the solid state; particles bond through solid-state diffusion. |
Temperature | Lower sintering temperature due to the liquid phase. | Higher temperatures required for solid-state diffusion. |
Material Suitability | Ideal for difficult-to-sinter materials or those requiring enhanced densification. | Suitable for materials achieving densification through solid-state diffusion. |
Process Efficiency | More efficient due to faster densification and lower temperatures. | Slower but straightforward, without the complexity of managing a liquid phase. |
Applications | Used in ceramics, cemented carbides, and certain metal alloys. | Commonly used for metals and ceramics achieving properties through solid-state diffusion. |
Equipment | Requires specialized sintering furnaces with precise temperature control. | Standard sintering furnaces are sufficient. |
Need help choosing the right sintering method for your materials? Contact our experts today for personalized advice!