When discussing molds in the context of thermoforming, the distinction between positive and negative molds is crucial. Negative molds are characterized by their concave cavities, which shape the material from the outside, while positive molds have a convex shape, shaping the material from the inside. This fundamental difference affects the design, application, and outcome of the thermoforming process, influencing factors such as material distribution, detail reproduction, and ease of demolding.
Key Points Explained:
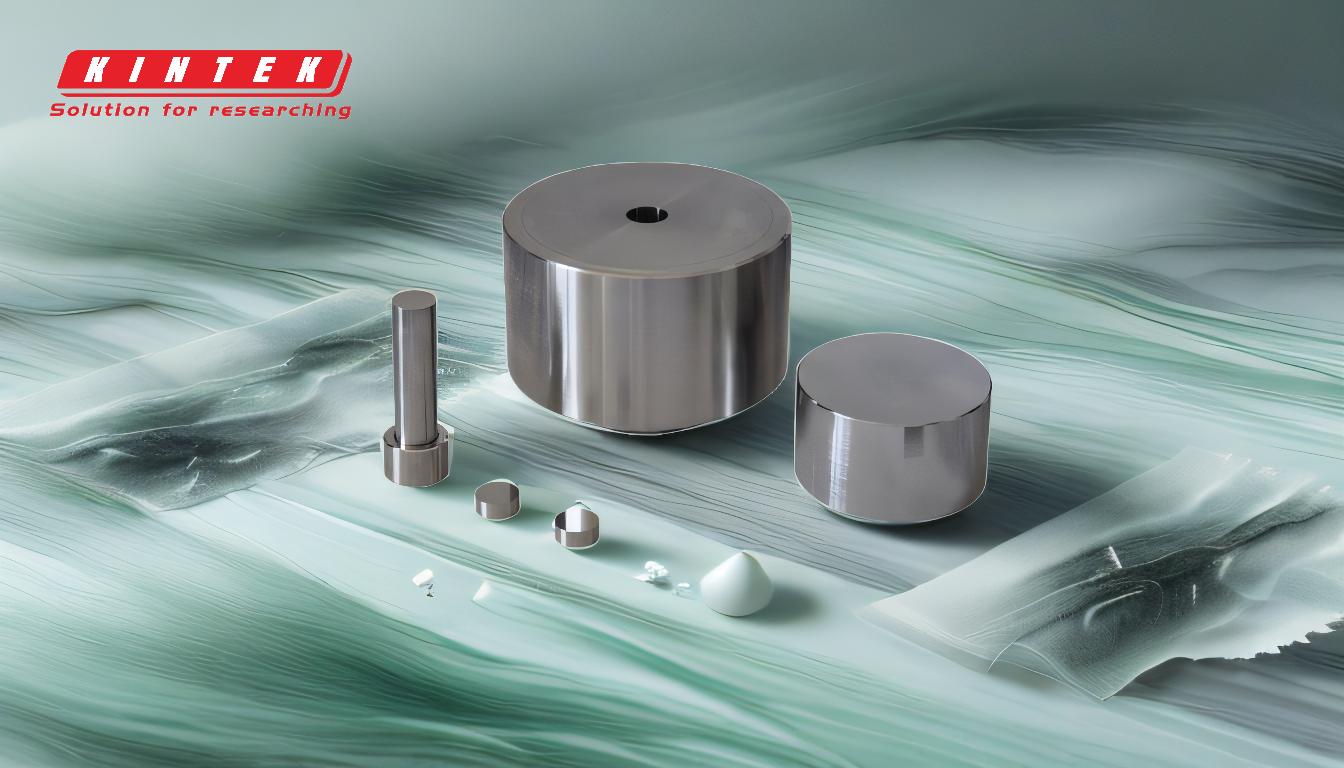
-
Definition and Structure:
- Negative Molds: These molds feature concave cavities. The material is draped over the mold, and the vacuum or pressure is applied to pull the material into the cavities, creating the desired shape from the outside.
- Positive Molds: These molds have a convex shape. The material is placed over the mold, and the vacuum or pressure is applied to push the material against the mold, shaping it from the inside.
-
Application in Thermoforming:
- Negative Molds: Ideal for creating parts with intricate details on the outer surface. Commonly used for packaging, where the exterior appearance is critical.
- Positive Molds: Suitable for parts where the interior surface needs to be precise and detailed. Often used for products like trays or containers where the internal dimensions are crucial.
-
Material Distribution:
- Negative Molds: Tend to result in more uniform material thickness, as the material is stretched into the cavities.
- Positive Molds: Can lead to variations in material thickness, especially at the edges, as the material is stretched over the convex shape.
-
Ease of Demolding:
- Negative Molds: Generally easier to demold, as the material shrinks away from the mold as it cools.
- Positive Molds: Can be more challenging to demold, as the material may cling to the convex surface, requiring more force or additional mechanisms for release.
-
Detail Reproduction:
- Negative Molds: Excellent for reproducing fine details on the outer surface of the product.
- Positive Molds: Better suited for detailing the inner surface, ensuring precise internal dimensions and features.
-
Design Considerations:
- Negative Molds: Designers must consider the depth and complexity of the cavities to ensure proper material flow and detail reproduction.
- Positive Molds: Designers need to account for the convex shape's impact on material distribution and demolding, often incorporating draft angles and release mechanisms.
Understanding these differences allows manufacturers to choose the appropriate mold type based on the specific requirements of the product, ensuring optimal quality and efficiency in the thermoforming process.
Summary Table:
Aspect | Negative Molds | Positive Molds |
---|---|---|
Structure | Concave cavities, shapes material from the outside. | Convex shape, shapes material from the inside. |
Application | Ideal for intricate outer surface details (e.g., packaging). | Suitable for precise internal dimensions (e.g., trays, containers). |
Material Distribution | Uniform thickness due to material stretching into cavities. | Thickness variations, especially at edges, due to stretching over convex shape. |
Ease of Demolding | Easier to demold; material shrinks away from the mold. | More challenging; material may cling to the convex surface. |
Detail Reproduction | Excellent for outer surface details. | Better for inner surface details and precise dimensions. |
Design Considerations | Focus on cavity depth and complexity for material flow and detail reproduction. | Incorporate draft angles and release mechanisms for easier demolding. |
Need help choosing the right mold for your thermoforming project? Contact our experts today!