Resistance and induction furnaces are both widely used in industrial heating and melting processes, but they differ significantly in their working principles, efficiency, and applications. Resistance furnaces rely on external heating elements to generate heat, which is then transferred to the material, while induction furnaces generate heat directly within the material using electromagnetic induction. This fundamental difference leads to variations in energy efficiency, contamination levels, and operational capabilities. Below, the key differences are explained in detail.
Key Points Explained:
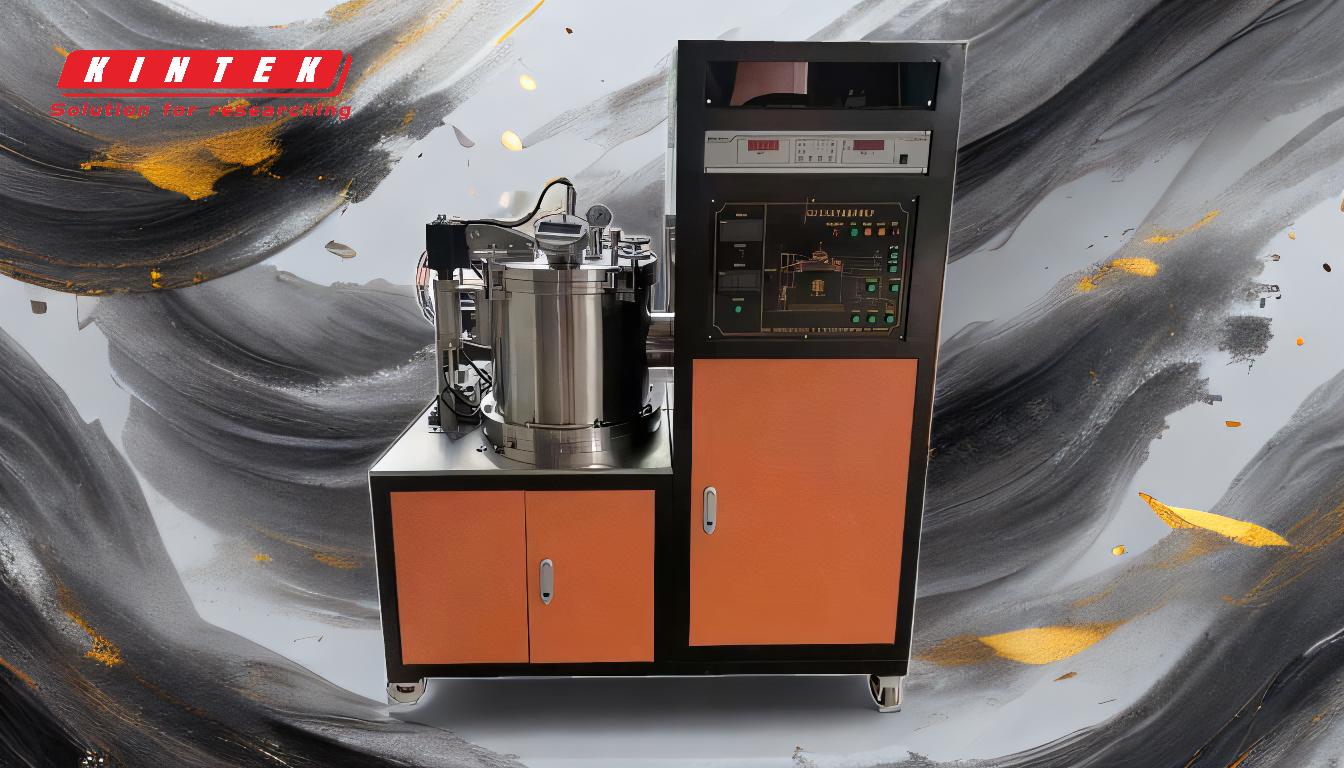
-
Heating Mechanism:
-
Resistance Furnace:
- Uses external heating elements (e.g., refractory elements or coils) to generate heat.
- Heat is transferred to the material through conduction, convection, or radiation.
- Suitable for processes where uniform heating is required, but the heat source is external to the material.
-
Induction Furnace:
- Generates heat directly within the material using electromagnetic induction.
- Alternating current creates an alternating magnetic field, inducing eddy currents in the material, which produce heat due to resistance.
- Ensures uniform heating and minimizes contamination since no external heat source is involved.
-
Resistance Furnace:
-
Efficiency and Energy Consumption:
-
Resistance Furnace:
- Less energy-efficient due to heat loss during transfer from the external source to the material.
- Requires more energy to maintain high temperatures, especially in large-scale operations.
-
Induction Furnace:
- More energy-efficient as heat is generated directly within the material, reducing heat loss.
- Achieves faster heating rates and higher thermal efficiency, making it ideal for high-temperature applications.
-
Resistance Furnace:
-
Temperature and Power Density:
-
Resistance Furnace:
- Operates at lower power densities compared to induction furnaces.
- Suitable for applications requiring moderate temperatures (e.g., annealing, tempering).
-
Induction Furnace:
- Capable of operating at higher temperatures and power densities.
- Can reach forging temperatures of up to 1250°C and melting temperatures of up to 1650°C, making it suitable for melting and high-temperature processing.
-
Resistance Furnace:
-
Contamination and Purity:
-
Resistance Furnace:
- Higher risk of contamination due to the use of external heating elements, which may introduce impurities.
- Requires careful selection of heating elements and furnace linings to minimize contamination.
-
Induction Furnace:
- Minimal contamination as heat is generated within the material itself.
- Ideal for applications requiring high-purity materials, such as in the semiconductor or aerospace industries.
-
Resistance Furnace:
-
Control and Automation:
-
Resistance Furnace:
- Typically relies on manual or semi-automated control systems.
- Limited by the complexity of maintaining uniform heating across large volumes.
-
Induction Furnace:
- Equipped with advanced control systems, including automatic frequency scanning, constant power control, and comprehensive protection mechanisms.
- Offers precise temperature control and smooth operation, reducing the need for manual intervention.
-
Resistance Furnace:
-
Applications:
-
Resistance Furnace:
- Commonly used for heat treatment processes like annealing, hardening, and tempering.
- Suitable for batch processing of materials that do not require extremely high temperatures.
-
Induction Furnace:
- Widely used in melting and forging applications, especially for metals like steel, aluminum, and copper.
- Preferred for continuous processes and high-temperature operations where efficiency and purity are critical.
-
Resistance Furnace:
-
Design and Maintenance:
-
Resistance Furnace:
- Simpler design with fewer components, making maintenance relatively straightforward.
- However, heating elements may require frequent replacement due to wear and tear.
-
Induction Furnace:
- More complex design with components like inductors, capacitors, and control systems.
- Requires careful design considerations, such as yoke layout and inductor spacing, to ensure optimal performance.
- Maintenance is easier for advanced models with integrated circuits and modular components.
-
Resistance Furnace:
-
Material Suitability:
-
Resistance Furnace:
- Suitable for a wide range of materials, including non-metallic and magnetic materials.
- Limited by the material's ability to absorb heat from an external source.
-
Induction Furnace:
- Best suited for conductive materials, especially metals.
- Challenges arise with non-magnetic materials like aluminum, which require specialized inductor designs to ensure efficient heating.
-
Resistance Furnace:
In summary, resistance and induction furnaces serve different purposes based on their heating mechanisms, efficiency, and applications. Resistance furnaces are better suited for moderate-temperature processes and batch operations, while induction furnaces excel in high-temperature, high-purity, and continuous processes. The choice between the two depends on the specific requirements of the application, including temperature, material type, and desired efficiency.
Summary Table:
Aspect | Resistance Furnace | Induction Furnace |
---|---|---|
Heating Mechanism | External heating elements transfer heat via conduction, convection, or radiation. | Heat generated directly within the material using electromagnetic induction. |
Efficiency | Less energy-efficient due to heat loss during transfer. | More energy-efficient with faster heating rates and reduced heat loss. |
Temperature Range | Suitable for moderate temperatures (e.g., annealing, tempering). | Capable of high temperatures (up to 1650°C) for melting and forging. |
Contamination Risk | Higher risk due to external heating elements. | Minimal contamination, ideal for high-purity applications. |
Control Systems | Manual or semi-automated control systems. | Advanced automation with precise temperature control and protection mechanisms. |
Applications | Heat treatment processes (e.g., annealing, hardening). | Melting, forging, and high-temperature operations for metals like steel and aluminum. |
Design & Maintenance | Simpler design but heating elements may require frequent replacement. | Complex design with easier maintenance for advanced models. |
Material Suitability | Suitable for non-metallic and magnetic materials. | Best for conductive materials, especially metals. |
Need help choosing the right furnace for your application? Contact our experts today for personalized advice!