Rockwool and ceramic fiber are both widely used insulation materials, but they differ significantly in terms of temperature resistance, applications, and material composition. Rockwool is primarily used for heat preservation at around 500°C, making it suitable for medium-temperature insulation. In contrast, ceramic fiber offers a broader range of temperature resistance, from low-temperature insulation at 200°C to fire insulation at 1000°C. This makes ceramic fiber more versatile for applications requiring extreme temperature resistance. Below, we explore the key differences between these materials in detail.
Key Points Explained:
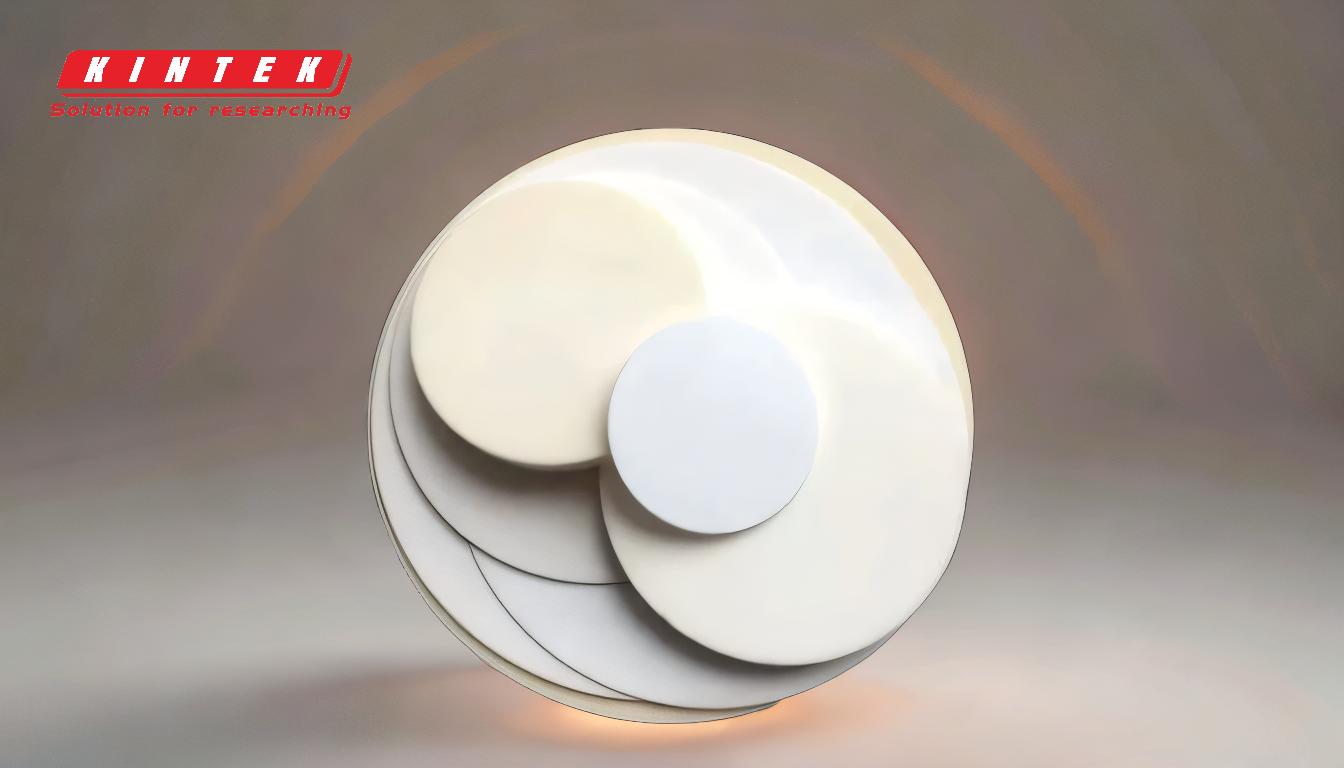
-
Temperature Resistance:
-
Ceramic Fiber:
- Can handle low-temperature insulation at 200°C.
- Suitable for medium-temperature insulation at 500°C.
- Capable of fire insulation at 1000°C.
- This wide range of temperature resistance makes ceramic fiber ideal for applications requiring extreme heat resistance, such as in furnaces, kilns, and high-temperature industrial processes.
-
Rockwool:
- Typically used for heat preservation at around 500°C.
- Not suitable for extremely high or low temperatures.
- Best for medium-temperature applications, such as building insulation and industrial equipment insulation.
-
Ceramic Fiber:
-
Material Composition:
-
Ceramic Fiber:
- Made from alumina-silica materials, which provide high thermal stability and resistance to thermal shock.
- Lightweight and flexible, making it easy to install in complex shapes and tight spaces.
-
Rockwool:
- Composed of natural basalt rock and recycled slag, which are melted and spun into fibers.
- Denser and heavier compared to ceramic fiber, providing better sound insulation and fire resistance in building applications.
-
Ceramic Fiber:
-
Applications:
-
Ceramic Fiber:
- Used in high-temperature environments such as furnaces, kilns, and boilers.
- Suitable for applications requiring thermal insulation in extreme conditions, including aerospace and automotive industries.
-
Rockwool:
- Commonly used in building insulation for walls, roofs, and floors.
- Also used in industrial settings for insulating pipes, tanks, and equipment operating at medium temperatures.
-
Ceramic Fiber:
-
Thermal Conductivity:
-
Ceramic Fiber:
- Lower thermal conductivity compared to rockwool, making it more efficient at insulating against high temperatures.
-
Rockwool:
- Higher thermal conductivity than ceramic fiber, but still effective for medium-temperature insulation and soundproofing.
-
Ceramic Fiber:
-
Durability and Longevity:
-
Ceramic Fiber:
- Highly durable in high-temperature environments but can degrade over time when exposed to thermal cycling and mechanical stress.
-
Rockwool:
- More durable in environments with moderate temperature fluctuations and mechanical stress, making it suitable for long-term use in building insulation.
-
Ceramic Fiber:
-
Cost Considerations:
-
Ceramic Fiber:
- Generally more expensive due to its specialized manufacturing process and high-temperature capabilities.
-
Rockwool:
- More cost-effective for medium-temperature applications and building insulation, making it a popular choice for large-scale projects.
-
Ceramic Fiber:
In summary, while both Rockwool and ceramic fiber are effective insulation materials, they serve different purposes based on their temperature resistance, material composition, and application areas. Ceramic fiber is the go-to choice for extreme high-temperature environments, whereas Rockwool is more suited for medium-temperature insulation and building applications. Understanding these differences is crucial for selecting the right material for specific insulation needs.
Summary Table:
Feature | Ceramic Fiber | Rockwool |
---|---|---|
Temperature Range | 200°C to 1000°C (low to high-temperature insulation) | Up to 500°C (medium-temperature insulation) |
Material Composition | Alumina-silica materials (lightweight, flexible) | Basalt rock and recycled slag (denser, heavier) |
Applications | Furnaces, kilns, boilers, aerospace, and automotive industries | Building insulation (walls, roofs, floors), industrial equipment insulation |
Thermal Conductivity | Lower thermal conductivity (efficient for high temperatures) | Higher thermal conductivity (effective for medium temperatures and soundproofing) |
Durability | Durable in high temperatures but degrades with thermal cycling | More durable in moderate temperature fluctuations and mechanical stress |
Cost | More expensive (specialized manufacturing) | Cost-effective for medium-temperature and building applications |
Need help choosing the right insulation material? Contact our experts today for personalized advice!