Rapid Thermal Anneal (RTA) and Rapid Thermal Processing (RTP) are terms often used interchangeably in semiconductor manufacturing, but they can have nuanced differences depending on the context. Both processes involve rapidly heating silicon wafers to high temperatures (often exceeding 1,000°C) for short durations to achieve specific material properties or device performance. However, RTP is a broader term that encompasses various thermal processes, including annealing, oxidation, and chemical vapor deposition, while RTA specifically refers to the annealing process. The distinction lies in the application and scope: RTA is a subset of RTP, focusing solely on annealing, whereas RTP covers a wider range of thermal treatments.
Key Points Explained:
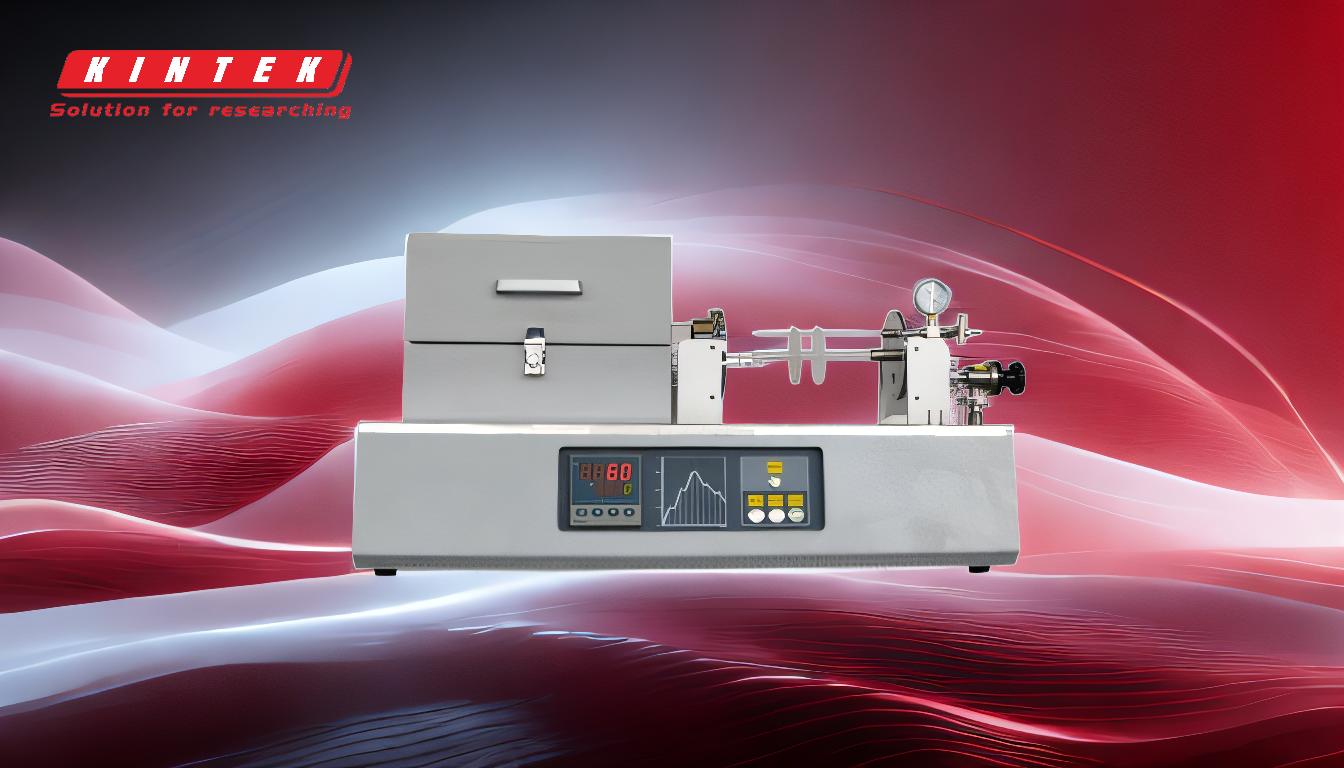
-
Definition and Scope:
- RTA (Rapid Thermal Anneal): A specific thermal process used to repair crystal lattice damage, activate dopants, or modify material properties by rapidly heating and cooling silicon wafers.
- RTP (Rapid Thermal Processing): A broader category of thermal processes that includes RTA but also encompasses other treatments like oxidation, nitridation, and deposition.
-
Temperature and Time:
- Both RTA and RTP involve heating wafers to temperatures exceeding 1,000°C. However, the duration and thermal profile may vary depending on the specific process and desired outcome.
- RTA typically focuses on achieving precise thermal cycles to optimize dopant activation or defect repair, while RTP may involve more complex thermal profiles for multiple purposes.
-
Applications:
- RTA: Primarily used for annealing purposes, such as activating dopants after ion implantation or repairing lattice damage caused by etching or deposition processes.
- RTP: Used for a wider range of applications, including growing oxide layers, forming silicides, and depositing thin films, in addition to annealing.
-
Equipment:
- Both RTA and RTP processes are performed using similar equipment, such as rapid thermal processing systems with lamp-based heating. However, RTP systems may have additional capabilities to support diverse thermal processes.
-
Industry Usage:
- The terms are often used interchangeably because RTA is a common application of RTP. However, when precision is required, RTA refers specifically to annealing, while RTP refers to the broader set of thermal processes.
In summary, while RTA and RTP are closely related and often overlap in usage, RTA is a specialized subset of RTP focused on annealing, whereas RTP encompasses a wider range of thermal treatments in semiconductor manufacturing.
Summary Table:
Aspect | RTA (Rapid Thermal Anneal) | RTP (Rapid Thermal Processing) |
---|---|---|
Definition | A specific thermal process for annealing, focusing on dopant activation and defect repair. | A broader category of thermal processes, including annealing, oxidation, nitridation, and more. |
Temperature | Exceeds 1,000°C with precise thermal cycles for annealing. | Exceeds 1,000°C, with varied thermal profiles for multiple purposes. |
Applications | Primarily used for annealing, dopant activation, and lattice repair. | Used for annealing, oxide growth, silicide formation, and thin film deposition. |
Equipment | Uses lamp-based heating systems, similar to RTP. | Similar to RTA but may include additional capabilities for diverse thermal processes. |
Industry Usage | Often used interchangeably, but RTA specifically refers to annealing. | Encompasses a wider range of thermal treatments beyond just annealing. |
Need expert guidance on RTA and RTP for your semiconductor processes? Contact us today to learn more!