Selective laser sintering (SLS) and electron beam melting (EBM) are both additive manufacturing (3D printing) technologies, but they differ significantly in their processes, materials, and applications. SLS uses a high-powered laser to sinter powdered material, typically polymers or metals, layer by layer to create a 3D object. EBM, on the other hand, uses an electron beam to melt metal powder in a vacuum environment, making it suitable for high-strength, high-temperature applications. While SLS is versatile and works with a range of materials, EBM is more specialized for metal parts, particularly in aerospace and medical industries. Both technologies eliminate the need for molds, but EBM offers higher precision and better mechanical properties for metal components.
Key Points Explained:
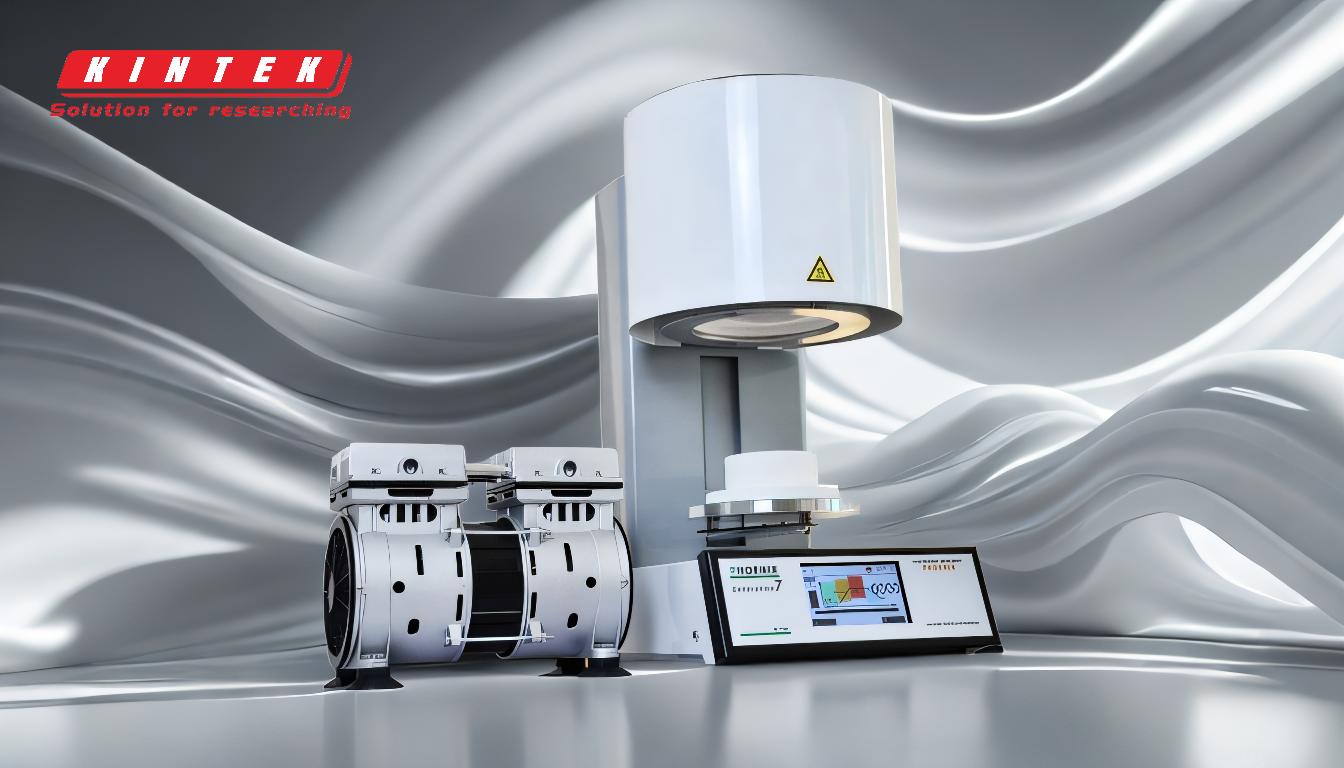
-
Process Mechanism:
- Selective Laser Sintering (SLS): Uses a high-powered laser to selectively sinter (fuse) powdered material, layer by layer, to build a 3D object. The laser heats the powder just enough to bond the particles without fully melting them.
- Electron Beam Melting (EBM): Uses a high-energy electron beam to fully melt metal powder in a vacuum chamber. The electron beam scans the powder bed, melting the material layer by layer to create a dense, high-strength part.
-
Materials Used:
- SLS: Primarily works with polymers (e.g., nylon, polyamide) and some metal powders. It is versatile and can handle a wide range of materials, including composites.
- EBM: Exclusive to metal powders, such as titanium, cobalt-chrome, and nickel-based alloys. It is ideal for producing high-strength, high-temperature-resistant parts.
-
Environmental Conditions:
- SLS: Operates in a controlled atmosphere, typically nitrogen or argon, to prevent oxidation of the material. It does not require a vacuum.
- EBM: Requires a high-vacuum environment to prevent contamination and ensure the electron beam functions effectively. This makes the process more complex and expensive.
-
Precision and Surface Finish:
- SLS: Produces parts with good surface finish and moderate precision. However, the surface may require post-processing (e.g., sanding or coating) for smoother finishes.
- EBM: Offers higher precision and better mechanical properties due to the full melting of metal powder. The parts have a rougher surface finish compared to SLS but are stronger and more durable.
-
Applications:
- SLS: Suitable for prototyping, functional parts, and low-volume production. Commonly used in automotive, aerospace, and consumer goods industries.
- EBM: Ideal for high-performance applications, such as aerospace components, medical implants, and turbine blades, where strength and thermal resistance are critical.
-
Cost and Production Speed:
- SLS: Generally faster and more cost-effective for prototyping and small-batch production. It does not require molds, reducing upfront costs.
- EBM: More expensive due to the vacuum environment and specialized equipment. It is slower but produces parts with superior mechanical properties, justifying the higher cost for critical applications.
-
Post-Processing Requirements:
- SLS: Parts may require minimal post-processing, such as support removal or surface finishing. However, the process is relatively straightforward.
- EBM: Parts often require heat treatment or machining to achieve the desired mechanical properties and surface finish. The vacuum environment also adds complexity to post-processing.
By understanding these key differences, equipment and consumable purchasers can make informed decisions based on the specific requirements of their projects, such as material properties, precision, and application needs.
Summary Table:
Aspect | Selective Laser Sintering (SLS) | Electron Beam Melting (EBM) |
---|---|---|
Process Mechanism | Uses a high-powered laser to sinter powdered material layer by layer. | Uses an electron beam to fully melt metal powder in a vacuum. |
Materials Used | Polymers (e.g., nylon, polyamide) and some metal powders. | Exclusive to metal powders (e.g., titanium, cobalt-chrome, nickel-based alloys). |
Environmental Conditions | Operates in a controlled atmosphere (nitrogen/argon). | Requires a high-vacuum environment. |
Precision & Surface Finish | Good surface finish, moderate precision. May require post-processing. | Higher precision, stronger parts. Rougher surface finish but superior mechanical properties. |
Applications | Prototyping, functional parts, low-volume production (automotive, aerospace, consumer goods). | High-performance applications (aerospace, medical implants, turbine blades). |
Cost & Production Speed | Faster and cost-effective for prototyping and small-batch production. | More expensive and slower, but ideal for critical applications. |
Post-Processing | Minimal (support removal, surface finishing). | Often requires heat treatment or machining due to vacuum environment. |
Need help choosing the right 3D printing technology for your project? Contact our experts today!