Vacuum casting and injection molding are two distinct manufacturing processes used to produce plastic or resin parts, each with its own advantages, limitations, and applications. Vacuum casting is a low-pressure process ideal for prototyping and small-batch production, offering high detail and material versatility. Injection molding, on the other hand, is a high-pressure process suited for mass production, providing high precision, repeatability, and cost efficiency at scale. The choice between the two depends on factors like production volume, material requirements, budget, and desired part quality. Below, the key differences between these processes are explained in detail.
Key Points Explained:
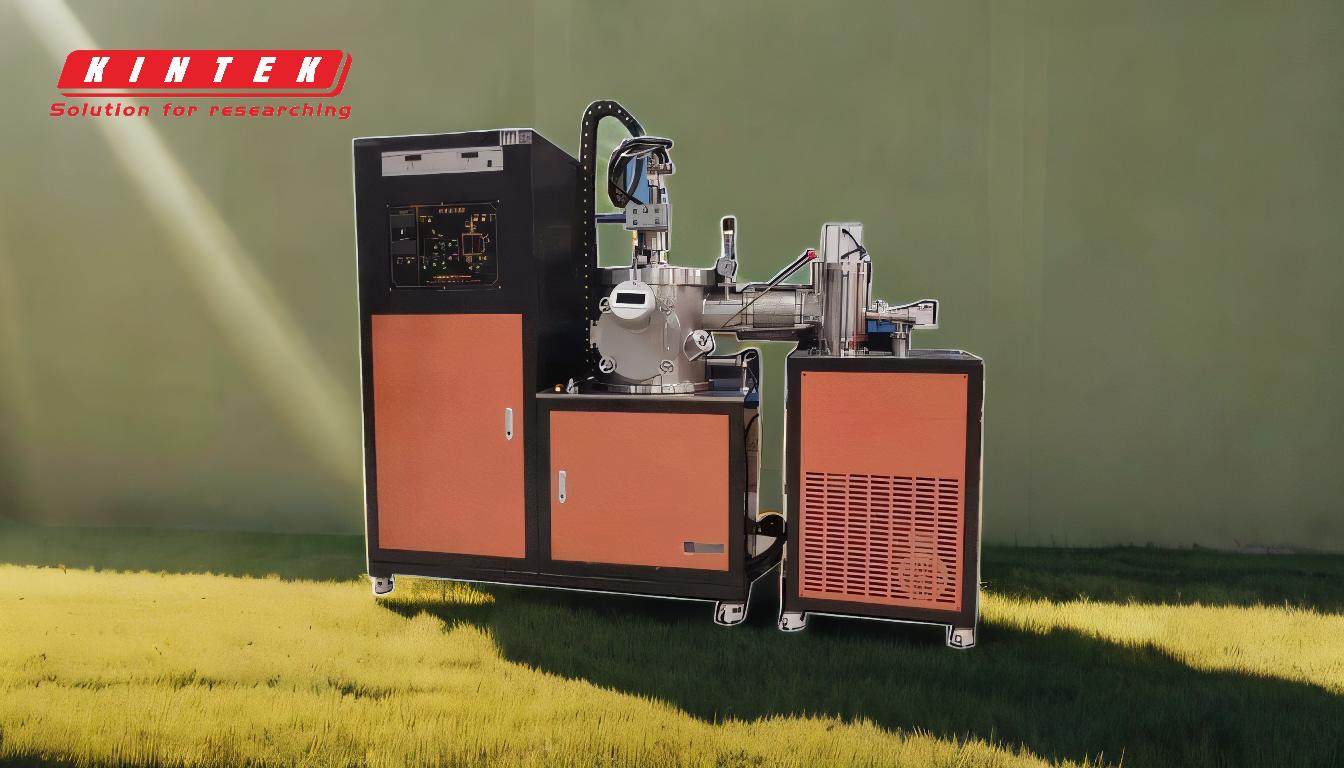
-
Process Mechanism:
-
Vacuum Casting:
- Uses a silicone mold created from a master pattern (often 3D printed).
- Liquid resin is poured into the mold, and a vacuum is applied to remove air bubbles, ensuring a smooth and detailed finish.
- The mold is then cured in an oven to solidify the resin.
-
Injection Molding:
- Involves injecting molten plastic or resin into a steel or aluminum mold under high pressure.
- The material cools and solidifies within the mold, after which the part is ejected.
- This process is highly automated and repeatable.
-
Vacuum Casting:
-
Production Volume:
-
Vacuum Casting:
- Best suited for low to medium production volumes (typically 10–50 parts per mold).
- Silicone molds degrade over time, limiting the number of parts that can be produced.
-
Injection Molding:
- Designed for high-volume production (thousands to millions of parts).
- Metal molds are durable and can withstand numerous cycles without significant wear.
-
Vacuum Casting:
-
Material Options:
-
Vacuum Casting:
- Offers a wide range of polyurethane resins that can mimic various engineering plastics (e.g., ABS, PP, PC).
- Limited to materials that can be cured at relatively low temperatures.
-
Injection Molding:
- Compatible with a vast array of thermoplastics and some thermosetting materials.
- Can handle high-performance materials like PEEK, nylon, and polycarbonate.
-
Vacuum Casting:
-
Cost Considerations:
-
Vacuum Casting:
- Lower initial costs due to inexpensive silicone molds.
- Higher per-unit costs for larger production runs due to mold degradation and manual labor.
-
Injection Molding:
- High upfront costs for tooling (metal molds).
- Lower per-unit costs for high-volume production due to automation and material efficiency.
-
Vacuum Casting:
-
Part Quality and Precision:
-
Vacuum Casting:
- Produces parts with excellent surface finish and fine details.
- Slight variations may occur due to manual processes and mold flexibility.
-
Injection Molding:
- Delivers high precision and consistency across all parts.
- Ideal for complex geometries and tight tolerances.
-
Vacuum Casting:
-
Lead Time:
-
Vacuum Casting:
- Shorter lead time for mold creation (typically 1–2 weeks).
- Suitable for rapid prototyping and quick-turnaround projects.
-
Injection Molding:
- Longer lead time for mold design and fabrication (several weeks to months).
- Economical only for large-scale production.
-
Vacuum Casting:
-
Applications:
-
Vacuum Casting:
- Ideal for prototyping, functional testing, and small-batch production.
- Commonly used in industries like automotive, consumer electronics, and medical devices.
-
Injection Molding:
- Best for mass production of consumer goods, automotive components, and industrial parts.
- Widely used in industries requiring high-volume, consistent output.
-
Vacuum Casting:
-
Environmental Impact:
-
Vacuum Casting:
- Generates less waste compared to injection molding.
- Silicone molds are not recyclable, but the process uses less energy.
-
Injection Molding:
- Can produce significant material waste (e.g., sprues and runners).
- Energy-intensive due to high-pressure machinery and heating requirements.
-
Vacuum Casting:
By understanding these key differences, manufacturers and designers can make informed decisions about which process best suits their specific needs, balancing factors like cost, volume, material, and part quality.
Summary Table:
Aspect | Vacuum Casting | Injection Molding |
---|---|---|
Process Mechanism | Uses silicone molds, vacuum removes air bubbles, resin cures in oven. | Molten plastic injected into metal molds under high pressure. |
Production Volume | Low to medium (10–50 parts per mold). | High-volume (thousands to millions of parts). |
Material Options | Polyurethane resins mimicking engineering plastics. | Wide range of thermoplastics and high-performance materials (e.g., PEEK). |
Cost Considerations | Lower initial costs, higher per-unit costs for larger runs. | High upfront tooling costs, lower per-unit costs for mass production. |
Part Quality | Excellent surface finish, slight variations due to manual processes. | High precision, consistency, and tight tolerances. |
Lead Time | Shorter (1–2 weeks for mold creation). | Longer (several weeks to months for mold fabrication). |
Applications | Prototyping, functional testing, small-batch production. | Mass production of consumer goods, automotive, and industrial parts. |
Environmental Impact | Less waste, uses less energy, silicone molds not recyclable. | Significant material waste, energy-intensive process. |
Still unsure which process is best for your project? Contact our experts today for personalized advice!