Flame brazing, while a widely used method for joining metals, has several disadvantages that can impact the quality, efficiency, and cost-effectiveness of the process. These drawbacks include the need for precise joint fits to ensure proper capillary action, potential annealing of components due to high temperatures, and design considerations for brazing material placement. Understanding these limitations is crucial for selecting the appropriate brazing method for specific applications.
Key Points Explained:
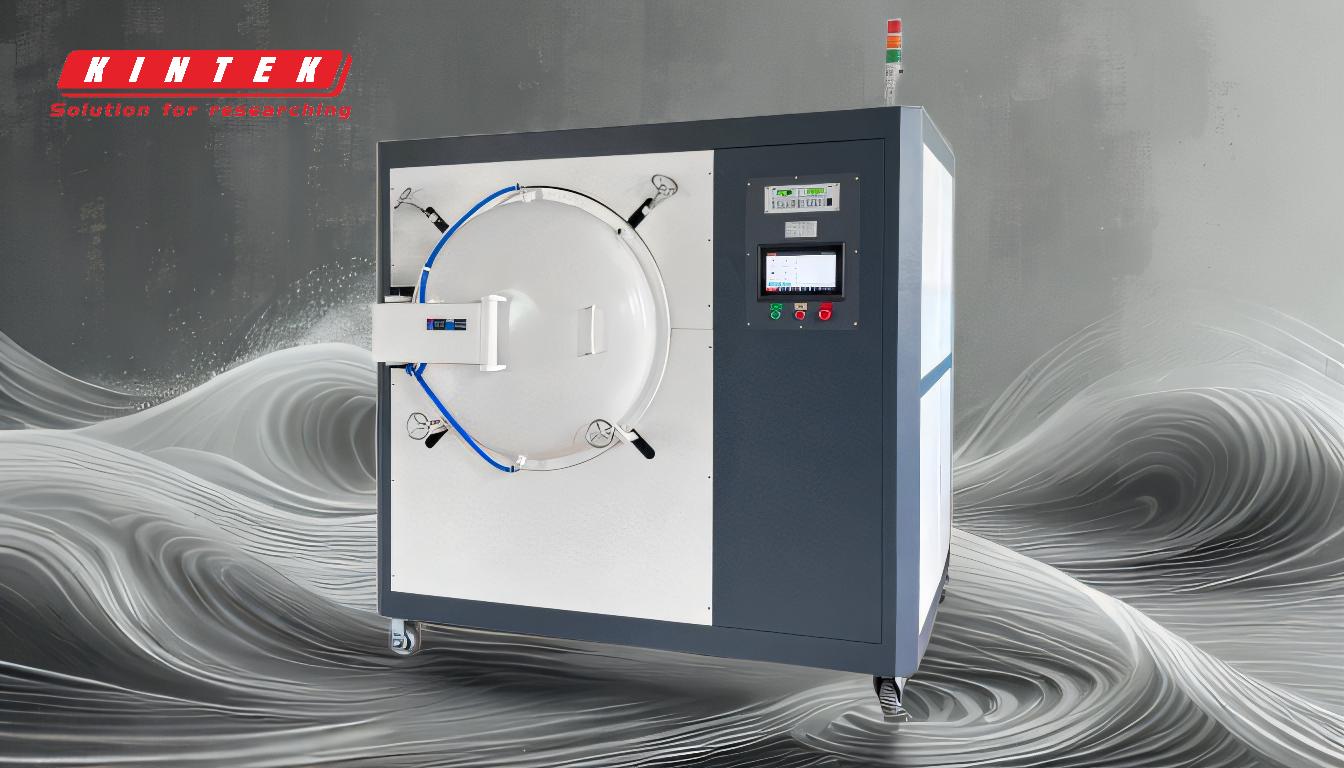
-
Need for Close Fits to Facilitate Capillary Action:
- Flame brazing relies on capillary action to draw the molten filler metal into the joint. This requires the joint surfaces to be very close together, typically within a few thousandths of an inch. Achieving and maintaining such tight tolerances can be challenging, especially for complex or large assemblies.
- Impact: The necessity for close fits can increase the complexity of the design and manufacturing process, potentially leading to higher costs and longer production times.
-
Annealing of Component Parts:
- The high temperatures used in flame brazing can cause the base metals to anneal, which is a process that softens the metal by altering its microstructure. This can be particularly problematic for metals that require high strength or hardness.
- Impact: Annealing can reduce the mechanical properties of the components, such as tensile strength and hardness, which may necessitate additional heat treatment processes to restore the desired properties. This adds to the overall cost and complexity of the manufacturing process.
-
Design Considerations for Brazing Material Placement:
- Flame brazing requires careful planning to ensure that the brazing material is placed correctly within the joint. This often involves designing the components to include features such as grooves or reservoirs to hold the filler metal.
- Impact: The need for such design modifications can complicate the engineering process and may limit the flexibility in component design. It also requires precise control during the brazing process to ensure that the filler metal flows correctly and forms a strong bond.
-
Potential for Oxidation and Contamination:
- The open flame used in flame brazing can expose the metal surfaces to oxygen, leading to oxidation. This can weaken the joint and reduce the overall quality of the brazed assembly.
- Impact: To mitigate oxidation, flux is often used, but this adds another step to the process and can introduce contamination if not properly applied or removed. Additionally, the use of flux may require post-brazing cleaning, further increasing the complexity and cost.
-
Limited Control Over Heat Distribution:
- Flame brazing can result in uneven heat distribution, which can lead to inconsistent joint quality. Areas that are too hot may experience excessive melting or distortion, while cooler areas may not achieve proper bonding.
- Impact: Inconsistent heat distribution can compromise the integrity of the brazed joint, leading to potential failures in service. It also requires skilled operators to manage the flame and heat application carefully, which can increase labor costs.
-
Safety and Environmental Concerns:
- The use of an open flame poses safety risks, including the potential for burns, fires, and explosions. Additionally, the process may produce harmful fumes, especially if fluxes or other chemicals are used.
- Impact: Safety measures and proper ventilation are essential, which can add to the operational costs. There may also be environmental regulations to consider, particularly regarding the disposal of used flux and other by-products.
In summary, while flame brazing is a versatile and widely used joining method, it comes with several disadvantages that can affect the quality, cost, and complexity of the manufacturing process. These include the need for precise joint fits, potential annealing of components, design considerations for brazing material placement, risks of oxidation and contamination, limited control over heat distribution, and safety and environmental concerns. Understanding these limitations is essential for making informed decisions about the use of flame brazing in specific applications.
Summary Table:
Disadvantage | Impact |
---|---|
Need for precise joint fits | Increases design complexity, costs, and production time |
Potential annealing of components | Reduces mechanical properties, requiring additional heat treatment |
Design considerations for material placement | Complicates engineering and limits design flexibility |
Oxidation and contamination risks | Weakens joints, requires flux, and increases post-brazing cleaning |
Limited control over heat distribution | Leads to inconsistent joint quality and higher labor costs |
Safety and environmental concerns | Requires safety measures, ventilation, and compliance with regulations |
Need help choosing the right brazing method for your application? Contact our experts today!