Metal processing methods, while essential for manufacturing and construction, come with several disadvantages that can impact efficiency, cost, and environmental sustainability. These drawbacks include high energy consumption, material waste, environmental pollution, and limitations in precision and complexity. Additionally, certain methods may require specialized equipment and skilled labor, increasing production costs. Understanding these disadvantages is crucial for industries to make informed decisions and explore alternative or complementary techniques to mitigate these challenges.
Key Points Explained:
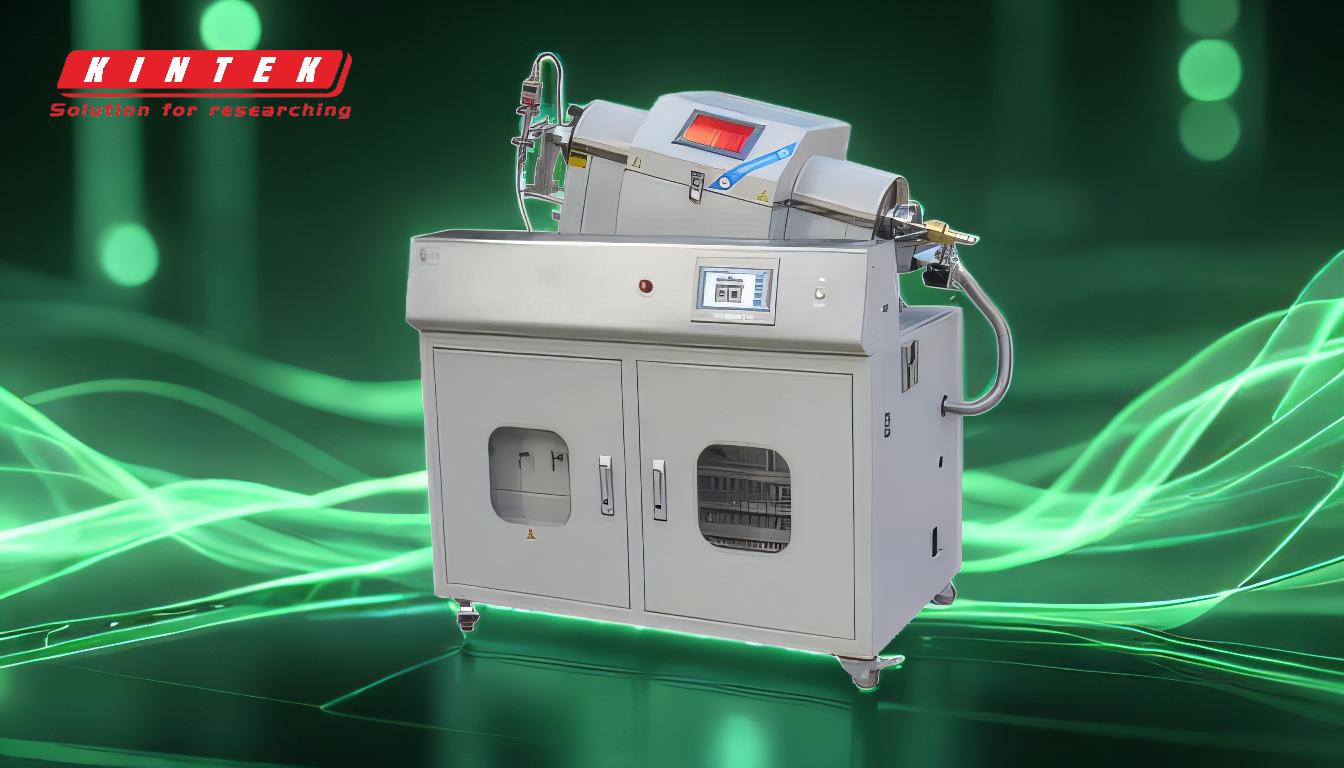
-
High Energy Consumption:
- Metal processing methods such as casting, forging, and machining often require significant amounts of energy to heat, melt, or shape metals. This not only increases operational costs but also contributes to higher carbon footprints, especially when non-renewable energy sources are used.
-
Material Waste:
- Many metal processing techniques, particularly machining and cutting, generate substantial material waste in the form of chips, shavings, or offcuts. This waste can be difficult to recycle or reuse, leading to increased material costs and environmental concerns.
-
Environmental Pollution:
- Processes like smelting, welding, and surface treatments can release harmful pollutants, including toxic gases, particulate matter, and chemical byproducts. These emissions can have detrimental effects on air quality, water sources, and soil, posing risks to both human health and ecosystems.
-
Limitations in Precision and Complexity:
- Traditional metal processing methods may struggle to achieve the high precision and intricate designs required for advanced engineering applications. Techniques like CNC machining offer better precision but are often limited by the complexity of the part geometry and the material properties.
-
Specialized Equipment and Skilled Labor:
- Many metal processing methods require expensive, specialized equipment and highly skilled operators. This can increase initial investment costs and ongoing operational expenses, making it challenging for smaller businesses to compete in the market.
-
Thermal and Mechanical Stress:
- Processes such as welding and heat treatment can introduce thermal and mechanical stresses into the metal, potentially leading to defects like warping, cracking, or weakened structural integrity. These issues can compromise the quality and durability of the final product.
-
Slow Production Rates:
- Some metal processing techniques, particularly those involving manual labor or complex setups, can be time-consuming. This can lead to slower production rates, which may not meet the demands of high-volume manufacturing or tight project deadlines.
-
Health and Safety Risks:
- Metal processing often involves hazardous conditions, such as exposure to high temperatures, sharp tools, and harmful chemicals. Ensuring worker safety requires stringent safety measures, which can add to the overall cost and complexity of operations.
By understanding these disadvantages, industries can explore alternative methods such as additive manufacturing, which offers reduced waste, greater design flexibility, and lower energy consumption in some cases. Additionally, adopting sustainable practices and investing in advanced technologies can help mitigate the negative impacts of traditional metal processing methods.
Summary Table:
Disadvantage | Key Impact |
---|---|
High Energy Consumption | Increases operational costs and carbon footprint. |
Material Waste | Generates chips, shavings, and offcuts, leading to higher material costs. |
Environmental Pollution | Releases toxic gases, particulate matter, and chemical byproducts. |
Precision and Complexity Limits | Struggles with intricate designs and high precision requirements. |
Specialized Equipment & Labor | Requires costly equipment and skilled operators, raising production costs. |
Thermal & Mechanical Stress | Can cause warping, cracking, or weakened structural integrity. |
Slow Production Rates | Time-consuming processes may delay high-volume manufacturing. |
Health & Safety Risks | Involves hazardous conditions, requiring stringent safety measures. |
Looking for sustainable metal processing solutions? Contact our experts today to explore alternatives!