Increasing the pressure during hot press sintering has significant effects on the sintering process and the final properties of the material. Higher pressure can enhance densification, improve mechanical properties, and influence the microstructure of the sintered material. However, it also introduces challenges such as potential anisotropy and limitations in product shape due to the unidirectional nature of the pressure. Below, we explore the key points in detail.
Key Points Explained:
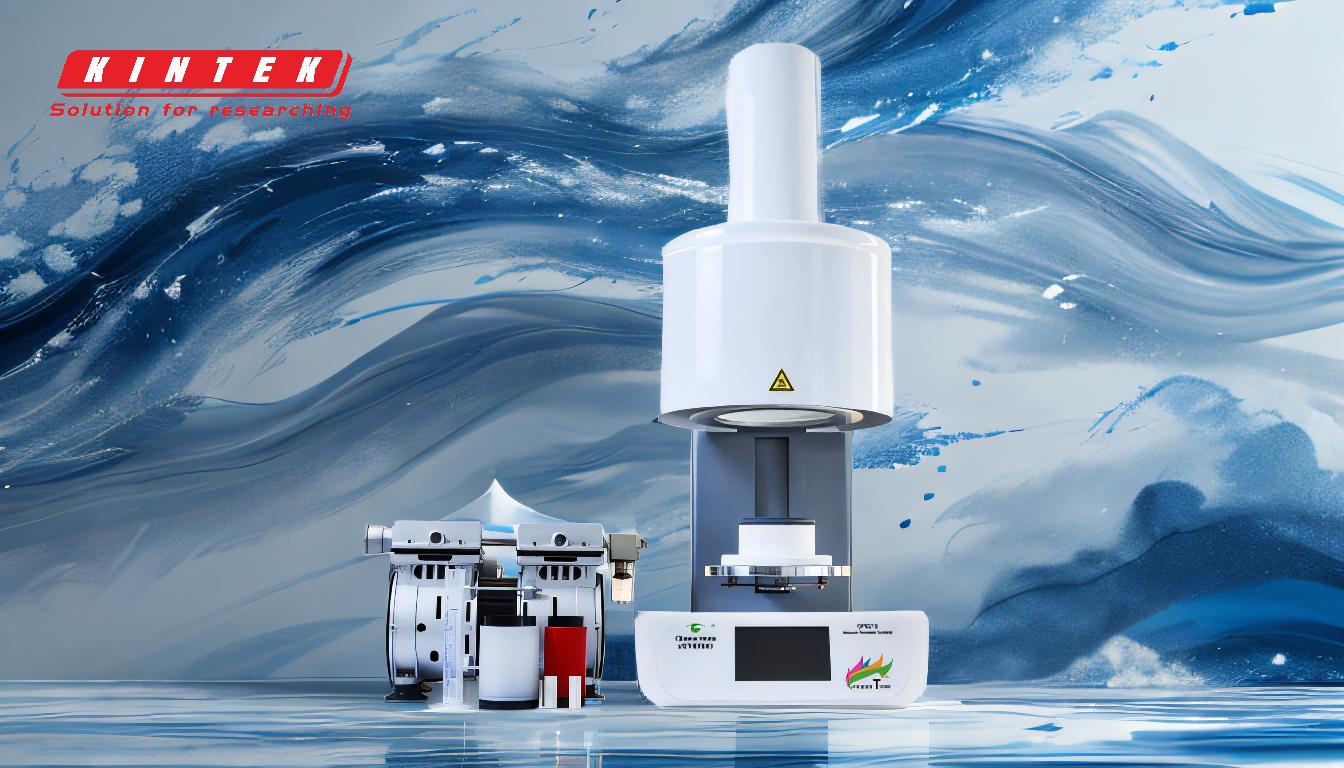
-
Enhanced Densification:
- Mechanism: Increasing pressure during sintering reduces the diffusion distance between particles by promoting particle rearrangement and eliminating agglomeration. This accelerates the densification process.
- Impact: Higher pressure provides a greater sintering driving force, which enhances viscosity flow, diffusion creep, grain rotation, grain boundary slip, and plastic deformation. These mechanisms collectively lead to faster and more complete densification of the green body.
- Example: In the middle and late stages of sintering, oscillating pressure (as in OPS technology) is particularly effective in achieving high-density materials.
-
Improved Mechanical Properties:
- Mechanism: The application of pressure during sintering can lead to a more uniform and refined microstructure, which typically results in improved mechanical properties such as hardness, strength, and toughness.
- Impact: The elimination of porosity and the promotion of grain boundary strengthening contribute to these enhanced properties.
- Example: Ceramics sintered under high pressure often exhibit superior mechanical performance compared to those sintered at lower pressures.
-
Microstructural Anisotropy:
- Mechanism: The unidirectional nature of the pressure in hot press sintering can lead to uneven pressure distribution within the billet. This uneven distribution can cause anisotropy in the microstructure and mechanical properties of the sintered material.
- Impact: Non-equiaxial crystal systems are particularly susceptible to this effect, leading to directional differences in properties such as strength and thermal conductivity.
- Example: Cylindrical or ring-shaped products produced via hot press sintering may exhibit different properties along different axes due to this anisotropy.
-
Shape and Size Limitations:
- Mechanism: The mold used in hot press sintering imposes constraints on the shape and size of the final product. The mold must withstand the high pressures and temperatures involved, limiting the complexity of the shapes that can be produced.
- Impact: This limitation means that hot press sintering is typically used for simpler geometries such as cylinders or rings, rather than more complex shapes.
- Example: Producing intricate or large components via hot press sintering is challenging due to these constraints.
-
Process Optimization:
- Mechanism: Balancing the pressure with other sintering parameters (such as temperature and time) is crucial for optimizing the sintering process. Too much pressure can lead to defects, while too little may result in incomplete densification.
- Impact: Proper optimization can lead to high-quality sintered materials with minimal defects and optimal properties.
- Example: In industrial applications, careful control of pressure and other parameters is essential for producing high-performance ceramics and other sintered materials.
In summary, increasing the pressure during hot press sintering significantly influences the densification, mechanical properties, and microstructure of the sintered material. While it offers several benefits, such as enhanced densification and improved mechanical properties, it also introduces challenges like microstructural anisotropy and shape limitations. Understanding these effects is crucial for optimizing the sintering process and achieving the desired material properties.
Summary Table:
Effect | Mechanism | Impact | Example |
---|---|---|---|
Enhanced Densification | Reduces diffusion distance, promotes particle rearrangement, eliminates agglomeration | Faster and more complete densification | Oscillating pressure (OPS) effective in high-density materials |
Improved Mechanical Properties | Uniform and refined microstructure, elimination of porosity | Enhanced hardness, strength, and toughness | High-pressure sintered ceramics show superior mechanical performance |
Microstructural Anisotropy | Uneven pressure distribution due to unidirectional nature of pressure | Directional differences in properties like strength and thermal conductivity | Cylindrical or ring-shaped products exhibit anisotropic properties |
Shape and Size Limitations | Mold constraints due to high pressure and temperature | Limited to simpler geometries like cylinders or rings | Intricate or large components are challenging to produce |
Process Optimization | Balancing pressure with temperature and time | High-quality materials with minimal defects and optimal properties | Industrial applications require careful control of parameters |
Optimize your sintering process with expert guidance—contact us today to learn more!