Sintering is a critical process in materials science where powdered materials are compacted and heated to form a solid structure. The application of pressure during sintering plays a significant role in influencing the final properties of the material. Pressure reduces sintering time and porosity, enhances densification, and improves mechanical properties such as tensile strength and impact energy. The optimal sintering process depends on various parameters, including temperature, pressure, particle size, and atmosphere. Understanding the effects of pressure during sintering is essential for achieving desired material properties and optimizing the manufacturing process.
Key Points Explained:
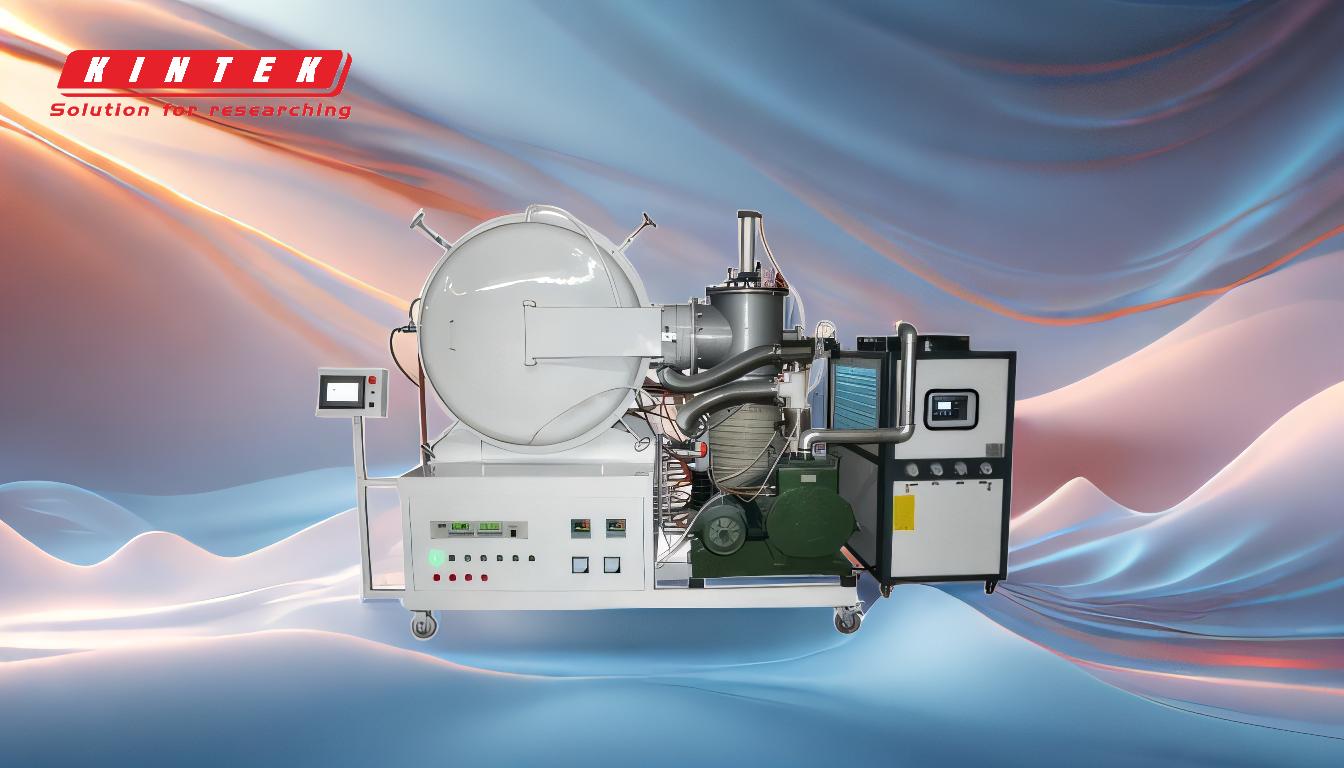
-
Reduction in Sintering Time and Porosity:
- Applying pressure during sintering significantly reduces the time required for the process. This is because pressure enhances particle rearrangement and promotes faster densification.
- Pressure also decreases the resulting porosity in the final product. Lower porosity leads to a denser and more uniform material, which is crucial for achieving high mechanical strength and durability.
-
Enhanced Densification:
- Pressure acts as an additional driving force for particle fusion, particularly in materials that are difficult to sinter. This is especially useful in techniques like hot pressing.
- The enhanced densification results in improved material properties, such as higher tensile strength, bending fatigue strength, and impact energy. These properties are critical for applications requiring robust and durable materials.
-
Influence of Sintering Parameters:
- Temperature: Higher sintering temperatures can increase compaction, but the amount of liquid phase must be carefully controlled to avoid defects.
- Particle Size: Finer powders generally promote better densification due to their higher surface area and reactivity.
- Atmosphere: The choice of atmosphere (e.g., air, vacuum, or inert gases like argon/nitrogen) can affect the sintering process and the final material properties.
-
Optimization of Sintering Process:
- The optimal sintering process is influenced by a combination of parameters, including sintering temperature, applied pressure, average grain size, and gaseous atmosphere.
- The choice of process depends on the expected product properties and the limiting parameters of the material being sintered. For example, materials that are difficult to sinter may require higher pressures and temperatures to achieve the desired densification.
-
Material-Specific Considerations:
- Different materials may respond differently to the application of pressure during sintering. For instance, ceramics and metals may require different pressure and temperature profiles to achieve optimal densification.
- The composition of the material also plays a crucial role. Homogeneous compositions with smaller particle sizes generally promote better densification and more uniform material properties.
In summary, the application of pressure during sintering is a powerful tool for enhancing the densification and mechanical properties of materials. By carefully controlling sintering parameters such as temperature, pressure, particle size, and atmosphere, manufacturers can optimize the sintering process to produce high-quality materials tailored to specific applications.
Summary Table:
Key Effect of Pressure | Impact on Sintering |
---|---|
Reduction in Sintering Time | Accelerates particle rearrangement and densification. |
Lower Porosity | Produces denser, more uniform materials with improved strength and durability. |
Enhanced Densification | Improves tensile strength, bending fatigue strength, and impact energy. |
Influence of Parameters | Temperature, particle size, and atmosphere play critical roles in optimizing sintering. |
Material-Specific Results | Different materials require tailored pressure and temperature profiles for best results. |
Want to optimize your sintering process? Contact our experts today for tailored solutions!