Sintering is a critical process in materials science that transforms powdered materials into dense, solid structures by applying heat and sometimes pressure. This process significantly impacts the microstructure of materials, including grain size, pore size, and grain boundary distribution, which in turn affects the material's mechanical properties such as strength, durability, and density. Sintering involves various physical and chemical changes, including material migration, grain boundary movement, and densification, leading to the formation of a cohesive and strong material body. The process can be achieved through methods like transient liquid phase sintering and permanent liquid phase sintering, depending on the material composition and desired properties.
Key Points Explained:
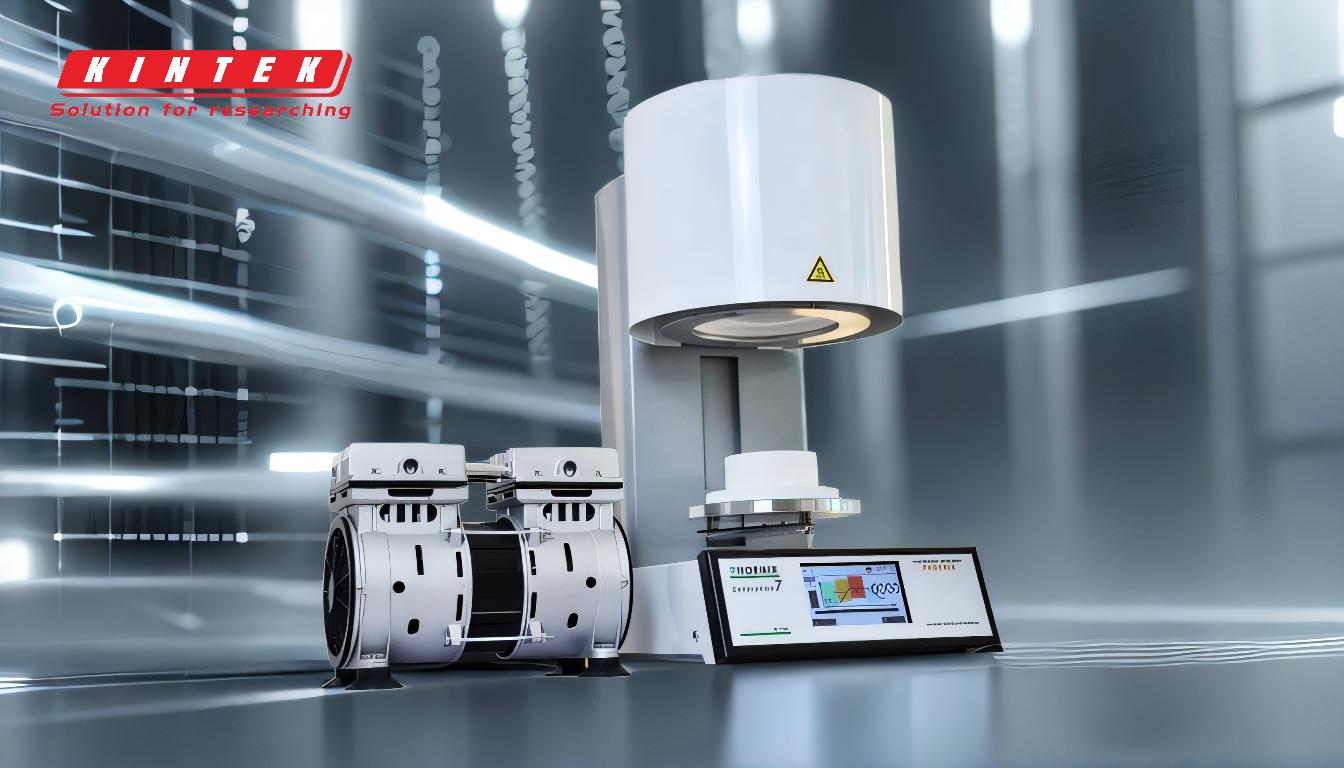
-
Microstructural Changes During Sintering:
- Grain Size: Sintering causes the grains within the material to grow and merge, leading to a reduction in grain boundaries and an increase in overall grain size. Larger grains can enhance certain properties like thermal stability but may reduce strength due to fewer grain boundaries.
- Pore Size: The process reduces the size and number of pores within the material, leading to increased density. This densification improves mechanical properties such as strength and durability.
- Grain Boundary Shape and Distribution: Sintering alters the shape and distribution of grain boundaries, which can influence the material's mechanical and thermal properties. Well-distributed grain boundaries can enhance strength and toughness.
-
Physical and Chemical Changes:
- Evaporation and Removal of Impurities: During sintering, water, organic matter, and adsorbed gases are evaporated or removed, leading to a purer material.
- Stress Relief: The high temperatures used in sintering help relieve internal stresses within the material, improving its structural integrity.
- Reduction of Surface Oxides: Surface oxides on powder particles are reduced, which enhances the bonding between particles.
- Material Migration and Recrystallization: Atoms migrate across grain boundaries, leading to recrystallization and grain growth, which are essential for densification and strength development.
-
Types of Sintering:
- Transient Liquid Phase Sintering: This method involves adding a material that melts at the sintering temperature, such as copper in iron powder. The liquid phase temporarily forms, facilitating particle bonding before solidifying.
- Permanent Liquid Phase Sintering: In this method, a liquid material, such as carbide, is added and remains liquid throughout the process. It flows into pores and cracks, further bonding the particles and enhancing density.
-
Impact on Material Properties:
- Strength and Durability: The densification and reduction of pores during sintering lead to materials with higher strength and durability. The elimination of weak points, such as large pores and impurities, contributes to these improved properties.
- Density: Sintering increases the material's density, making it more suitable for applications requiring high mechanical performance.
- Thermal and Electrical Properties: The changes in microstructure can also affect thermal and electrical conductivity, making sintered materials useful in various industrial applications.
-
Applications and Importance:
- Ceramics and Metals: Sintering is essential for producing dense ceramic and metal parts with desired mechanical properties. It is widely used in industries such as automotive, aerospace, and electronics.
- Customization of Properties: By controlling the sintering process, manufacturers can tailor the material's properties to meet specific application requirements, such as increased hardness, wear resistance, or thermal stability.
In summary, sintering is a transformative process that significantly impacts the microstructure and properties of materials. By understanding and controlling the sintering process, manufacturers can produce materials with enhanced strength, durability, and density, suitable for a wide range of industrial applications.
Summary Table:
Aspect | Key Details |
---|---|
Microstructural Changes | Grain size growth, pore size reduction, and improved grain boundary distribution. |
Physical & Chemical Changes | Evaporation of impurities, stress relief, and material migration for densification. |
Types of Sintering | Transient and permanent liquid phase sintering for tailored material properties. |
Impact on Properties | Enhanced strength, durability, density, and thermal/electrical conductivity. |
Applications | Widely used in ceramics, metals, automotive, aerospace, and electronics industries. |
Discover how sintering can optimize your material properties—contact our experts today!