The efficiency of biomass pyrolysis is influenced by a variety of factors, including the type and moisture content of the biomass, the temperature and residence time in the pyrolysis furnace, and the pressure conditions. Proper control of these factors is essential to optimize the process and achieve the desired end products, such as bio-oil, bio-char, and syngas. Case studies from companies like Haldor Topsøe, Showa Denko K.K, Green Fuel, and Rentech demonstrate the versatility and potential of biomass pyrolysis in producing biofuels and other valuable outputs. Additionally, advanced technologies like PLC automation and modular designs enhance the efficiency and adaptability of pyrolysis systems. Policies and regulations further support the sustainable and environmentally-friendly operation of these facilities.
Key Points Explained:
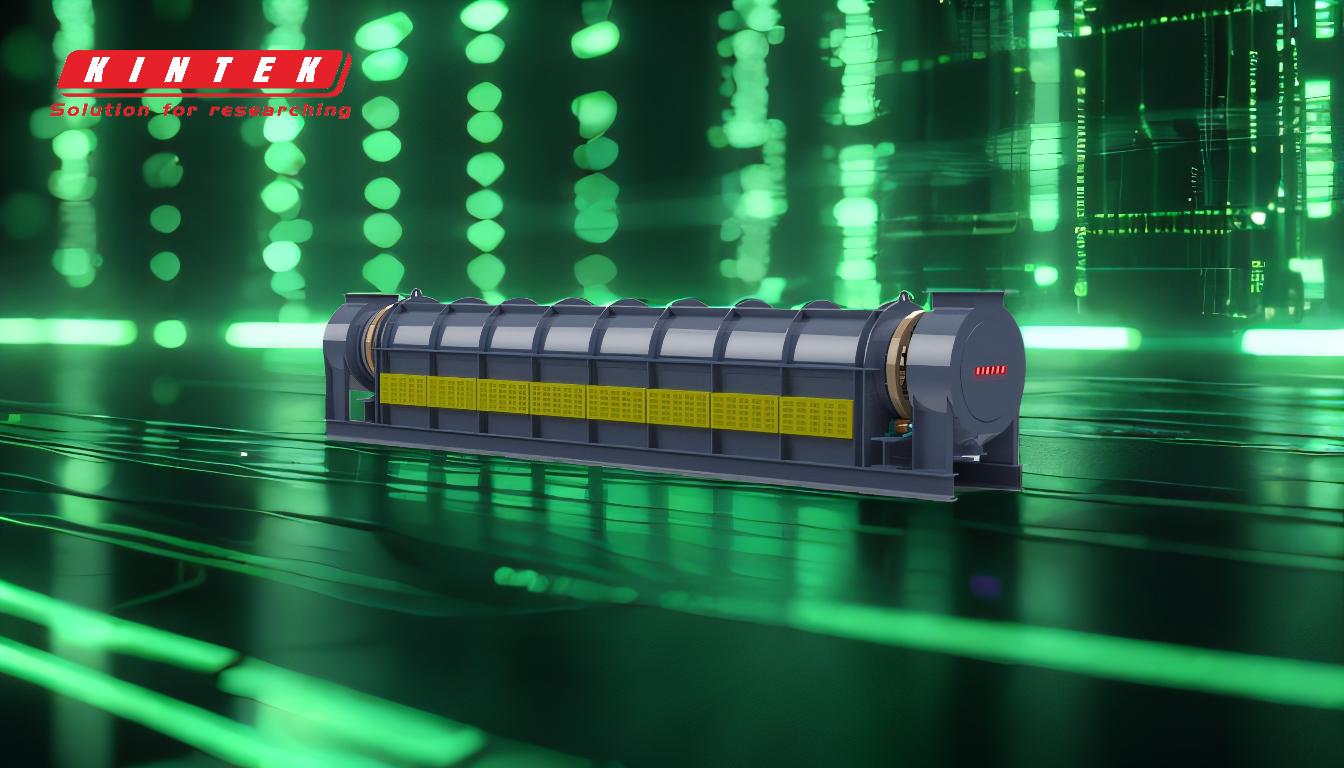
-
Factors Affecting Efficiency:
- Biomass Type and Moisture Content: Different types of biomass (e.g., wood, agricultural residues) have varying chemical compositions and moisture levels, which can significantly impact the pyrolysis process. High moisture content can reduce efficiency by requiring more energy to evaporate water before pyrolysis begins.
- Temperature and Residence Time: The temperature within the pyrolysis furnace and the duration that biomass remains in the reactor are critical. Optimal temperatures (typically between 400°C and 600°C) and sufficient residence time ensure complete decomposition of biomass into desired products.
- Pressure Conditions: Operating pressure can influence the yield and composition of pyrolysis products. For instance, higher pressures may favor the production of bio-oil over bio-char.
-
Technological Advancements:
- Flexible Heating Methods: Modern pyrolysis machines can adapt to various fuel types, enhancing their versatility and efficiency.
- High-Temperature Resistance: The use of high-aluminum refractory castables ensures durability and thermal insulation, maintaining consistent high temperatures for effective pyrolysis.
- Corrosion-Resistant Materials: Double-layer pyrolysis cylinders made of stainless steel prevent corrosion, extending the lifespan of the equipment.
- Precise Temperature Control: Multiple temperature monitoring points and advanced PLC automation technology allow for accurate control, optimizing the pyrolysis process.
- Modular Design: Rapid assembly and customization options make pyrolysis systems adaptable to different scales and requirements.
-
Case Studies:
- Haldor Topsøe: Converts biomass into a biofuel similar to diesel, showcasing the potential for renewable fuel production.
- Showa Denko K.K: Produces bio-oil from biomass, demonstrating the versatility of pyrolysis in generating liquid fuels.
- Green Fuel: Focuses on bio-char production, highlighting the use of pyrolysis in creating soil amendments and carbon sequestration products.
- Rentech: Converts biomass into synthetic natural gas (SNG), illustrating the application of pyrolysis in producing gaseous fuels.
-
Policy and Regulatory Support:
- Governments and regulatory bodies promote the use of sustainable and renewable energy sources through policies that encourage the adoption of biomass pyrolysis technologies. These regulations ensure that pyrolysis facilities operate safely and with minimal environmental impact, supporting the transition to a circular economy.
-
Waste Composition and Reactor Settings:
- The efficiency of pyrolysis is also influenced by the composition of the biomass waste flow. The extent to which the organic fraction can be degraded and converted into gas form affects the temperature, pressure, and other reactor settings. Proper management of these parameters is crucial for maximizing the efficiency of the pyrolysis process.
By understanding and optimizing these factors, biomass pyrolysis can be a highly efficient and sustainable method for converting biomass into valuable energy products, contributing to the reduction of greenhouse gas emissions and the promotion of renewable energy sources.
Summary Table:
Key Factors | Impact on Efficiency |
---|---|
Biomass Type & Moisture | High moisture reduces efficiency; different biomass types yield varying results. |
Temperature & Residence Time | Optimal range (400°C–600°C) ensures complete decomposition into bio-oil, bio-char, syngas. |
Pressure Conditions | Higher pressures favor bio-oil production; affects yield and product composition. |
Technological Advancements | PLC automation, modular designs, and corrosion-resistant materials enhance efficiency. |
Policy & Regulations | Support sustainable operations, ensuring minimal environmental impact. |
Ready to optimize your biomass pyrolysis process? Contact us today for expert guidance and solutions!