The electron deposition method is a technique used to create thin films or coatings on a substrate by utilizing the kinetic energy of electrons. Unlike the aerosol deposition method, which relies on high-speed ceramic particles, electron deposition typically involves the use of an electron beam to deposit material onto a surface. This method is widely used in various industries, including semiconductor manufacturing, optics, and nanotechnology, due to its precision and ability to produce high-quality coatings.
Key Points Explained:
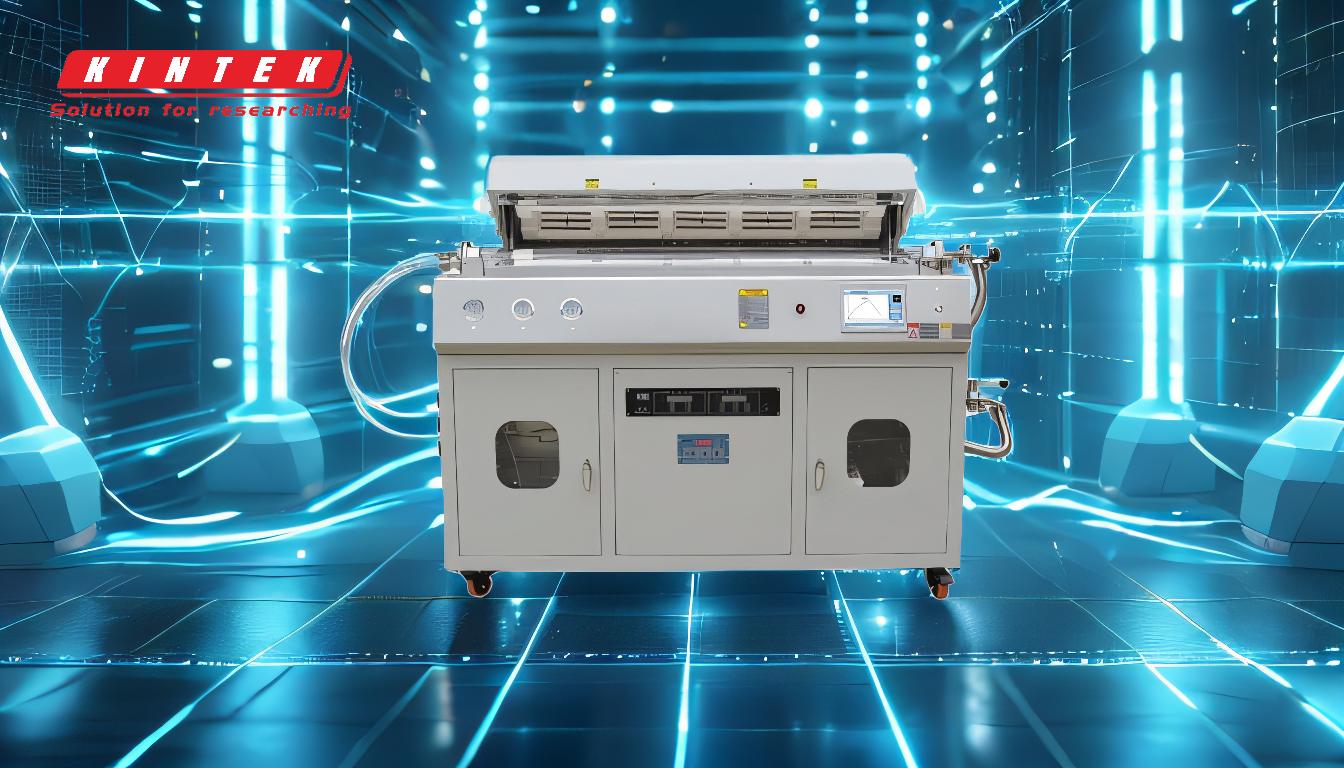
-
Principle of Electron Deposition:
- Electron deposition involves directing a focused beam of electrons onto a target material, causing it to vaporize and deposit onto a substrate.
- The process is typically carried out in a vacuum to prevent contamination and ensure a clean deposition environment.
-
Components of the Electron Deposition System:
- Electron Gun: Generates and focuses the electron beam.
- Vacuum Chamber: Maintains a low-pressure environment to facilitate the deposition process.
- Substrate Holder: Holds the material onto which the coating is to be deposited.
- Target Material: The material that is vaporized and deposited onto the substrate.
-
Advantages of Electron Deposition:
- High Precision: The electron beam can be precisely controlled, allowing for the deposition of very thin and uniform layers.
- Versatility: A wide range of materials, including metals, ceramics, and polymers, can be deposited using this method.
- No Additional Heat Treatment: Similar to the aerosol deposition method, electron deposition often does not require additional heat treatment, which can simplify the manufacturing process.
-
Applications of Electron Deposition:
- Semiconductor Industry: Used for depositing thin films of conductive and insulating materials on semiconductor wafers.
- Optics: Employed in the production of anti-reflective coatings and other optical films.
- Nanotechnology: Utilized in the fabrication of nanostructures and nanodevices.
-
Comparison with Aerosol Deposition:
- While both methods aim to create high-density coatings, electron deposition offers greater precision and is more suitable for applications requiring extremely thin and uniform layers.
- Aerosol deposition, on the other hand, is often faster and can be more cost-effective for certain applications, especially those involving ceramic materials.
-
Challenges and Considerations:
- Cost: Electron deposition systems can be expensive due to the need for high vacuum and precise electron beam control.
- Material Limitations: Not all materials are suitable for electron deposition, and some may require special handling or pre-treatment.
- Complexity: The process can be more complex compared to other deposition methods, requiring skilled operators and sophisticated equipment.
In summary, the electron deposition method is a highly precise and versatile technique for creating thin films and coatings. Its ability to produce high-quality, uniform layers without the need for additional heat treatment makes it a valuable tool in various high-tech industries. However, it also comes with challenges such as cost and complexity, which must be carefully considered when selecting a deposition method for a specific application.
Summary Table:
Aspect | Details |
---|---|
Principle | Uses an electron beam to vaporize and deposit material onto a substrate. |
Key Components | Electron gun, vacuum chamber, substrate holder, target material. |
Advantages | High precision, versatility, no additional heat treatment required. |
Applications | Semiconductor manufacturing, optics, nanotechnology. |
Challenges | High cost, material limitations, process complexity. |
Comparison with Aerosol | More precise, but slower and costlier than aerosol deposition for ceramics. |
Discover how electron deposition can elevate your manufacturing process—contact our experts today!