The energy efficiency of a ball mill is generally low, with typical values around 1% for mineral ball milling and rod milling. This inefficiency is due to various factors such as the physical-chemical properties of the feed material, the size and density of the grinding balls, the rotation speed of the mill, and the filling ratio of the mill. While some crushing processes can achieve slightly higher energy efficiencies (up to 8% in high energy-efficient quasi-static uniaxial compression crushing), ball mills remain relatively energy-inefficient. Optimizing factors like drum diameter, length-to-diameter ratio, and timely removal of ground product can improve productivity but have limited impact on overall energy efficiency.
Key Points Explained:
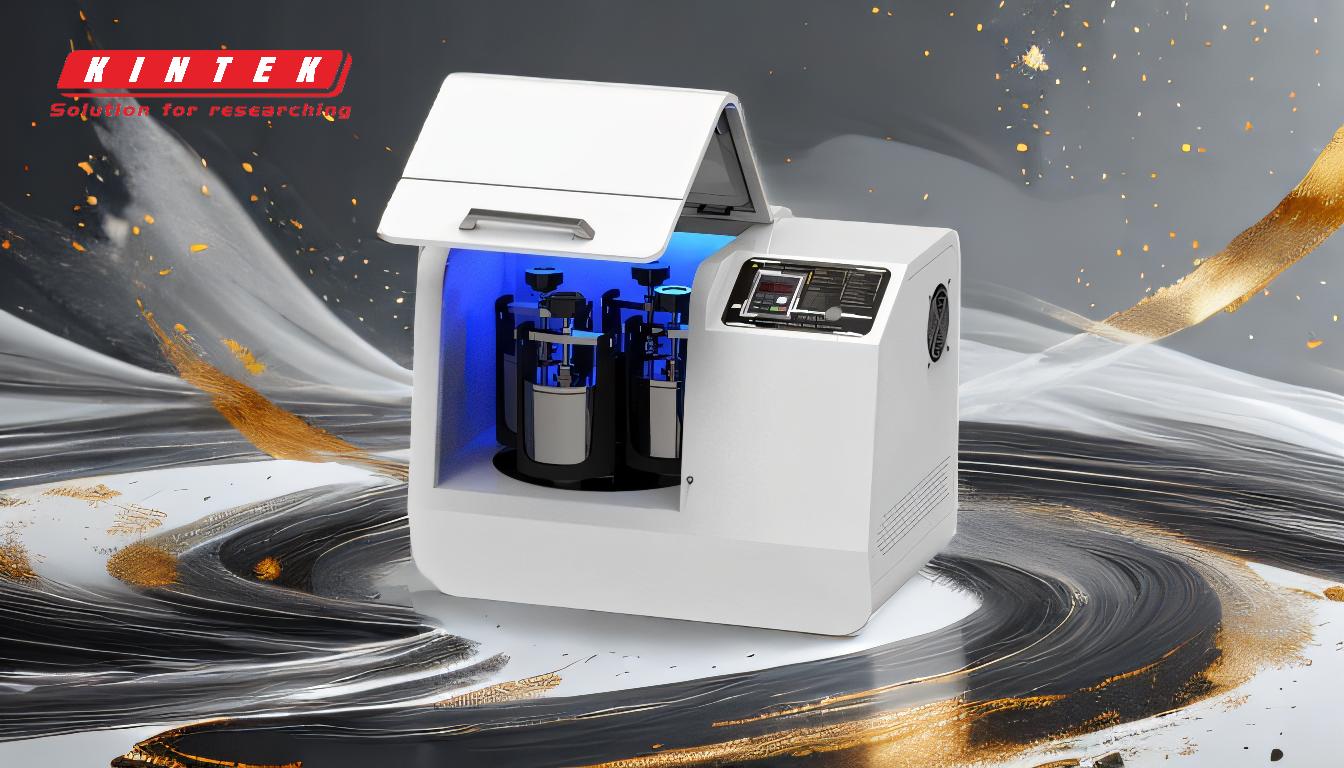
-
Energy Efficiency of Ball Mills:
- The energy efficiency of ball mills is generally low, with mineral ball milling and rod milling achieving around 1% efficiency.
- This low efficiency is due to the nature of the grinding process, where a significant amount of energy is lost as heat and sound rather than being used for material size reduction.
-
Factors Affecting Energy Efficiency:
- Physical-Chemical Properties of Feed Material: Harder or more abrasive materials require more energy to grind, reducing efficiency.
- Grinding Medium (Balls): The size, density, and number of balls impact the energy transfer efficiency. Larger or denser balls may improve grinding but can also increase energy consumption.
- Rotation Speed: Optimal rotation speed ensures effective grinding, but excessive speed can lead to energy waste.
- Filling Ratio: The percentage of the mill volume filled with grinding medium affects energy efficiency. Overfilling or underfilling can reduce efficiency.
-
Comparison with Other Crushing Processes:
- Crushing processes generally have higher energy efficiencies than ball milling, with values ranging from 3%-5% for standard crushing and up to 8% for high energy-efficient quasi-static uniaxial compression crushing.
- This highlights the inherent inefficiency of ball mills compared to other size reduction methods.
-
Optimization Strategies:
- Drum Diameter and Length-to-Diameter Ratio: An optimal L:D ratio (1.56–1.64) can improve productivity but has limited impact on energy efficiency.
- Timely Removal of Ground Product: Efficient removal of ground material can prevent over-grinding and reduce energy waste.
- Armor Surface Shape: The design of the mill's interior surface can influence grinding efficiency by affecting the movement of the grinding medium and material.
-
Residence Time and Feed Rate:
- The residence time of material in the mill chamber and the feed rate influence the degree of milling. Longer residence times can lead to over-grinding and energy waste, while faster feed rates may reduce grinding effectiveness.
-
Energy Loss Mechanisms:
- Energy is lost in ball mills through heat generation, sound, and friction between the grinding medium and the mill walls.
- These losses contribute to the low overall energy efficiency of the process.
-
Limitations of Ball Mills:
- Despite their widespread use, ball mills are inherently energy-inefficient due to the mechanical nature of the grinding process.
- Improvements in energy efficiency are limited by the physical principles governing the grinding process.
In summary, while ball mills are effective for grinding a wide range of materials, their energy efficiency is low, typically around 1%. This inefficiency is influenced by factors such as the properties of the feed material, the grinding medium, and the operational parameters of the mill. While some optimization strategies can improve productivity, they have limited impact on overall energy efficiency. Comparing ball mills to other crushing processes highlights their relative inefficiency, with other methods achieving higher energy efficiencies.
Summary Table:
Key Aspect | Details |
---|---|
Energy Efficiency | Typically around 1% for mineral ball milling and rod milling. |
Factors Affecting Efficiency | Feed material properties, grinding ball size/density, rotation speed, filling ratio. |
Comparison to Other Processes | Crushing processes achieve 3%-8% efficiency, outperforming ball mills. |
Optimization Strategies | Adjust drum diameter, L:D ratio, timely product removal, and armor design. |
Energy Loss Mechanisms | Heat, sound, and friction contribute to energy inefficiency. |
Looking to optimize your ball mill performance? Contact our experts today for tailored solutions!