Silver brazing is a process that requires precise temperature control and uniform heat distribution to ensure strong, reliable joints. The choice of heat source is critical, as it directly impacts the quality of the brazed joints, the efficiency of the process, and the overall cost. The most excellent heat sources for silver brazing include oxy-acetylene torches, induction heating systems, and furnace brazing. Each method has its unique advantages, such as localized heating, rapid processing, or suitability for mass production. The selection depends on factors like the material being brazed, joint design, production volume, and desired precision.
Key Points Explained:
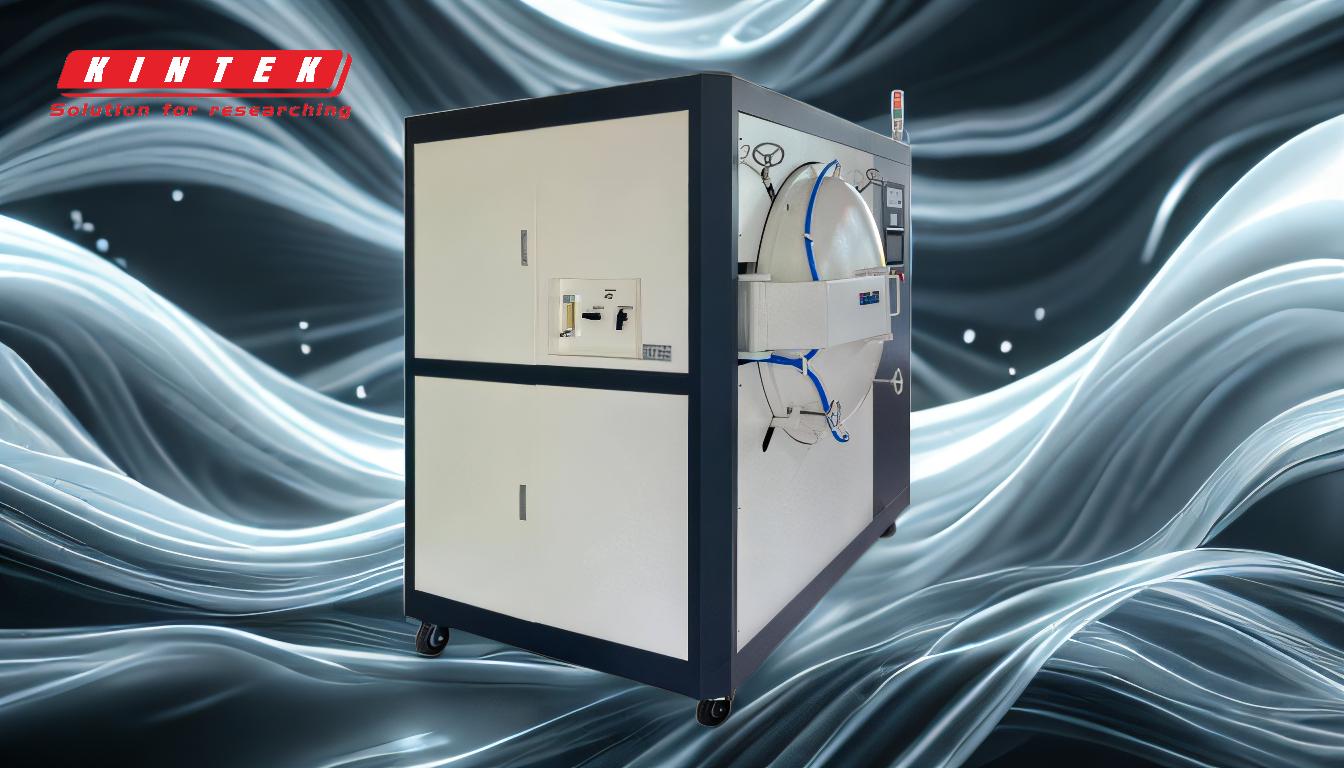
-
Oxy-Acetylene Torch:
-
Advantages:
- Provides localized heating, which is ideal for small-scale or intricate brazing tasks.
- Offers high temperatures (up to 3,500°C), suitable for silver brazing alloys.
- Portable and versatile, making it a popular choice for repair work and field applications.
-
Considerations:
- Requires skilled operators to control the flame and prevent overheating or oxidation.
- Not ideal for mass production due to slower processing times compared to other methods.
-
Advantages:
-
Induction Heating:
-
Advantages:
- Delivers rapid, localized heating with precise temperature control, minimizing heat-affected zones.
- Highly efficient and repeatable, making it suitable for high-volume production.
- Clean and energy-efficient, as it does not require an open flame.
-
Considerations:
- Initial setup costs can be higher due to the need for specialized equipment.
- Best suited for parts with simple geometries or those that can be easily adapted to induction coils.
-
Advantages:
-
Furnace Brazing:
-
Advantages:
- Provides uniform heating, making it ideal for complex assemblies or large-scale production.
- Can be used with controlled atmospheres (e.g., vacuum or inert gas) to prevent oxidation and improve joint quality.
- Suitable for brazing multiple parts simultaneously, increasing throughput.
-
Considerations:
- Requires longer cycle times compared to other methods.
- Higher initial investment and operational costs, especially for vacuum or controlled-atmosphere furnaces.
-
Advantages:
-
Factors Influencing Heat Source Selection:
- Material Compatibility: The heat source must be compatible with the base metals and silver brazing alloys used.
- Joint Design: Complex joints may require uniform heating, while simple joints can benefit from localized heating.
- Production Volume: High-volume production often favors induction heating or furnace brazing, while low-volume or repair work may use oxy-acetylene torches.
- Precision Requirements: Applications requiring precise temperature control and minimal heat-affected zones benefit from induction heating or furnace brazing.
-
Emerging Technologies:
- Laser Brazing: Offers ultra-precise heating for delicate or high-precision applications, though it is less common for silver brazing.
- Resistance Heating: Suitable for specific applications where direct electrical resistance heating of the joint is feasible.
In conclusion, the choice of heat source for silver brazing depends on the specific requirements of the application. Oxy-acetylene torches are versatile and portable, induction heating offers precision and efficiency, and furnace brazing ensures uniform heating for large-scale production. By carefully evaluating the material, joint design, and production needs, you can select the most excellent heat source for your silver brazing process.
Summary Table:
Heat Source | Advantages | Considerations |
---|---|---|
Oxy-Acetylene Torch | - Localized heating for small-scale tasks - High temperatures (up to 3,500°C) - Portable and versatile |
- Requires skilled operators - Not ideal for mass production |
Induction Heating | - Rapid, precise heating - High efficiency and repeatability - Clean and energy-efficient |
- Higher initial setup costs - Best for simple geometries |
Furnace Brazing | - Uniform heating for complex assemblies - Controlled atmospheres prevent oxidation - Suitable for mass production |
- Longer cycle times - Higher initial and operational costs |
Need help selecting the right heat source for your silver brazing process? Contact our experts today for personalized advice!