The floating catalyst chemical vapor deposition (CVD) method is a specialized technique within the broader CVD family, used primarily for synthesizing advanced materials like carbon nanotubes (CNTs) and graphene. Unlike traditional CVD, which involves a fixed substrate, the floating catalyst method introduces a catalyst in a gaseous or aerosol form into the reaction chamber. This catalyst "floats" in the gas stream, enabling the growth of nanomaterials directly in the gas phase. The method is highly efficient for producing high-quality, large-area films or nanostructures with precise control over material properties. It is widely used in applications such as electronic transistors, transparent conductors, and corrosion-resistant coatings.
Key Points Explained:
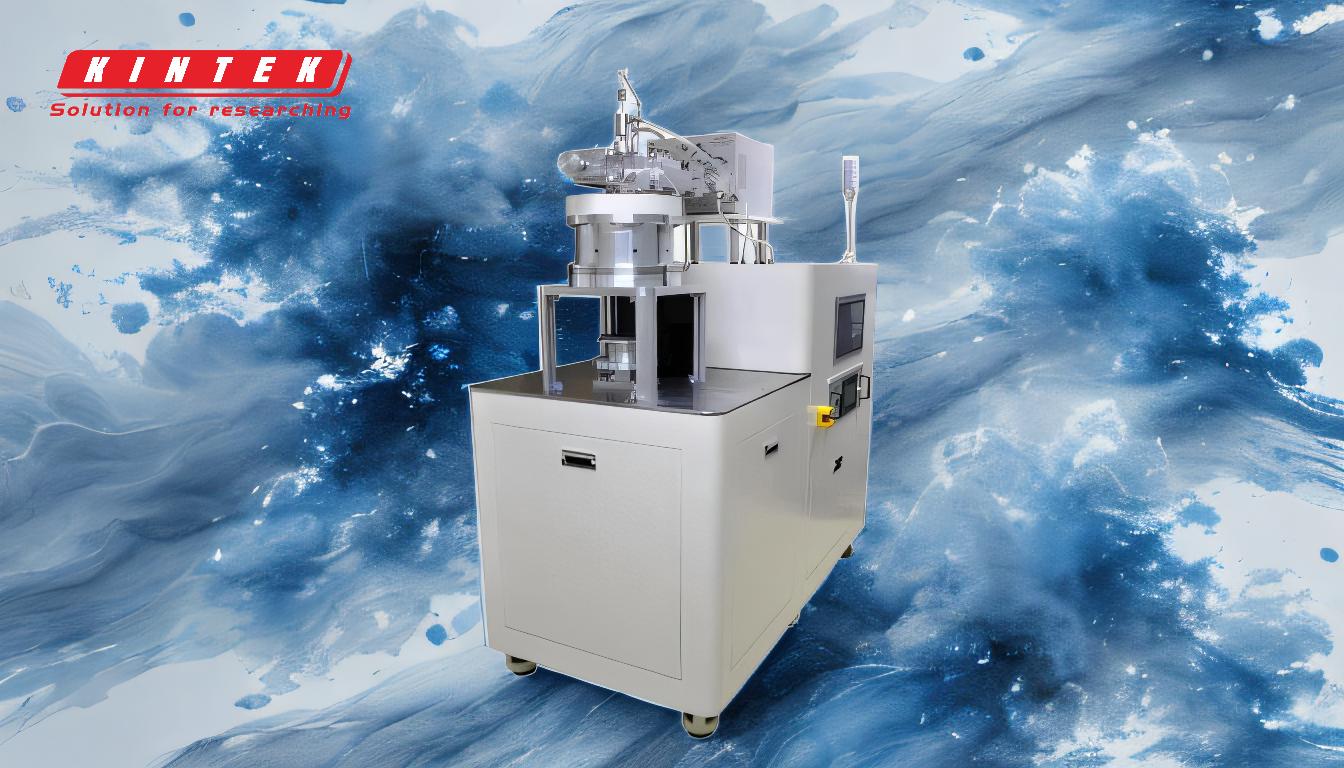
-
Definition and Core Concept:
- The floating catalyst CVD method is a variant of chemical vapor deposition where the catalyst is introduced in a gaseous or aerosol form rather than being pre-deposited on a substrate.
- This allows the catalyst to "float" in the gas stream, facilitating the growth of nanomaterials directly in the gas phase.
-
Mechanism of Operation:
- The process involves introducing precursor gases and a catalyst into a high-temperature reaction chamber.
- The catalyst particles act as nucleation sites for the growth of nanomaterials like carbon nanotubes or graphene.
- The reaction occurs in the gas phase, and the resulting materials are deposited onto a substrate or collected as free-standing structures.
-
Advantages Over Traditional CVD:
- Scalability: The floating catalyst method is highly scalable, making it suitable for industrial production of nanomaterials.
- Uniformity: It produces uniform, high-quality films or nanostructures with minimal defects.
- Flexibility: The method allows for precise control over material properties by adjusting parameters such as temperature, pressure, and gas flow rates.
-
Applications:
- Electronic Devices: Used to fabricate high-performance transistors, sensors, and transparent conductors.
- Energy Storage: Applied in the development of advanced batteries and supercapacitors.
- Coatings: Produces corrosion-resistant and wear-resistant coatings for industrial applications.
-
Key Parameters:
- Temperature: Critical for controlling the reaction kinetics and material quality.
- Gas Flow Rate: Influences the uniformity and growth rate of the nanomaterials.
- Catalyst Concentration: Determines the density and morphology of the synthesized materials.
-
Comparison with Other Methods:
- Unlike physical vapor deposition (PVD), which relies on physical processes like evaporation, CVD involves chemical reactions in the gas phase.
- Compared to the high-pressure high-temperature (HPHT) method, floating catalyst CVD operates at lower pressures and temperatures, making it more energy-efficient.
-
Challenges and Limitations:
- Catalyst Contamination: Residual catalyst particles can affect the purity of the final product.
- Process Control: Requires precise control over reaction conditions to achieve consistent results.
- Cost: While more efficient than some methods, the equipment and precursor materials can still be expensive.
By leveraging the floating catalyst CVD method, researchers and manufacturers can produce advanced nanomaterials with tailored properties for a wide range of cutting-edge applications.
Summary Table:
Aspect | Details |
---|---|
Definition | A CVD variant where the catalyst is introduced in gaseous or aerosol form. |
Key Mechanism | Catalyst "floats" in the gas stream, enabling gas-phase nanomaterial growth. |
Advantages | Scalability, uniformity, and precise control over material properties. |
Applications | Electronics, energy storage, and industrial coatings. |
Key Parameters | Temperature, gas flow rate, and catalyst concentration. |
Comparison to PVD | Involves chemical reactions, unlike PVD's physical processes. |
Challenges | Catalyst contamination, process control, and cost. |
Learn how floating catalyst CVD can revolutionize your nanomaterial production—contact our experts today!