The Electric Arc Furnace (EAF) is a critical piece of equipment in the steelmaking industry, primarily used to melt scrap metal or other raw materials to produce steel. It operates by generating an electric arc between electrodes and the charged material, reaching temperatures high enough to melt the metal. EAFs are favored for their efficiency, flexibility, and ability to recycle scrap metal, making them a sustainable alternative to traditional blast furnaces. They are widely used in mini-mills and are capable of producing a wide range of steel grades. Below, the key functions and advantages of EAFs are explained in detail.
Key Points Explained:
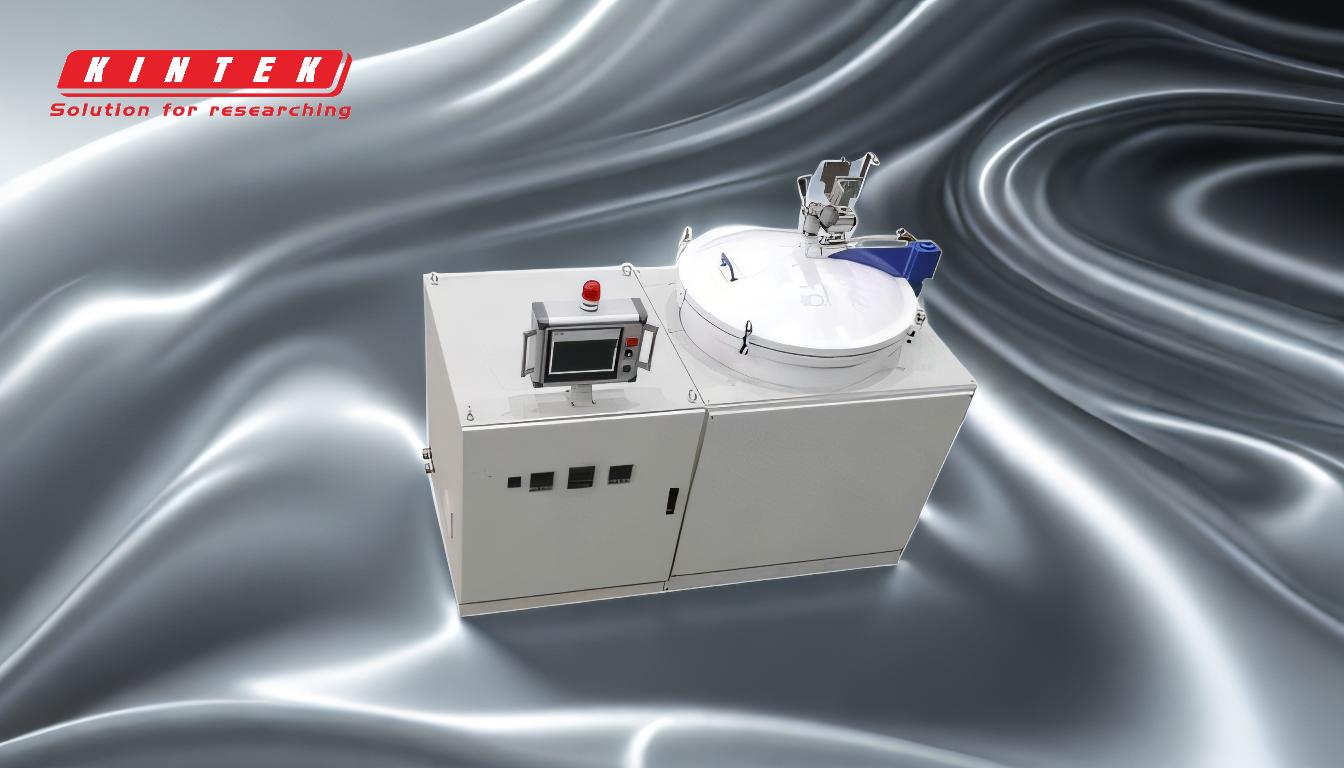
-
Primary Function: Melting Scrap Metal
- The EAF's core function is to melt scrap metal or other raw materials (such as direct reduced iron or pig iron) to produce molten steel.
- The electric arc generated between the graphite electrodes and the charged material reaches temperatures of up to 3,500°C, sufficient to melt steel.
- This process is highly efficient and allows for the recycling of scrap metal, reducing the need for virgin iron ore and lowering environmental impact.
-
Flexibility in Steel Production
- EAFs can produce a wide variety of steel grades, from basic carbon steels to high-quality alloy steels.
- The ability to adjust the chemical composition of the steel during the melting process makes EAFs highly versatile.
- This flexibility is particularly advantageous for mini-mills, which often cater to niche markets or produce specialized steel products.
-
Energy Efficiency and Sustainability
- EAFs are more energy-efficient than traditional blast furnaces, as they primarily use electricity rather than fossil fuels.
- The use of scrap metal as a primary feedstock reduces the carbon footprint of steel production, aligning with global sustainability goals.
- Modern EAFs are equipped with energy recovery systems, further enhancing their efficiency.
-
Rapid Production Cycles
- EAFs have shorter production cycles compared to blast furnaces, typically taking 30 to 40 minutes to produce a batch of molten steel.
- This rapid turnaround time allows for quicker response to market demands and reduces inventory costs.
-
Cost-Effectiveness
- The use of scrap metal as a feedstock significantly reduces raw material costs.
- EAFs require less capital investment and have lower operating costs compared to blast furnaces, making them ideal for smaller-scale operations.
-
Environmental Benefits
- EAFs produce fewer greenhouse gas emissions compared to traditional steelmaking methods.
- The recycling of scrap metal reduces landfill waste and conserves natural resources.
-
Technological Advancements
- Modern EAFs incorporate advanced technologies such as automation, real-time monitoring, and process optimization systems.
- These advancements improve operational efficiency, product quality, and safety.
-
Applications in Mini-Mills
- EAFs are the backbone of mini-mills, which are smaller-scale steel production facilities.
- Mini-mills benefit from the EAF's flexibility, cost-effectiveness, and ability to produce high-quality steel from scrap.
-
Global Adoption
- EAFs are widely used in regions with abundant scrap metal supplies, such as North America and Europe.
- Their adoption is growing in developing countries as they seek more sustainable and cost-effective steelmaking solutions.
-
Challenges and Limitations
- EAFs rely heavily on the availability of high-quality scrap metal, which can be a limiting factor in some regions.
- The process requires a stable and reliable electricity supply, which may be a challenge in areas with inadequate infrastructure.
In summary, the Electric Arc Furnace (EAF) is a versatile and efficient tool in modern steelmaking, offering significant advantages in terms of flexibility, sustainability, and cost-effectiveness. Its ability to recycle scrap metal and produce high-quality steel makes it an essential component of the global steel industry.
Summary Table:
Key Feature | Description |
---|---|
Primary Function | Melts scrap metal or raw materials to produce molten steel. |
Temperature | Reaches up to 3,500°C using electric arcs. |
Flexibility | Produces a wide range of steel grades, from carbon to alloy steels. |
Energy Efficiency | Uses electricity, reducing reliance on fossil fuels. |
Sustainability | Recycles scrap metal, lowering carbon footprint and conserving resources. |
Production Speed | Short cycles (30-40 minutes) for rapid steel production. |
Cost-Effectiveness | Lower raw material and operational costs compared to blast furnaces. |
Environmental Benefits | Fewer greenhouse gas emissions and reduced landfill waste. |
Technological Advancements | Features automation, real-time monitoring, and energy recovery systems. |
Applications | Widely used in mini-mills for niche and specialized steel products. |
Ready to explore how an Electric Arc Furnace can transform your steelmaking process? Contact our experts today for tailored solutions!