A kiln, particularly a rotary kiln, is a crucial piece of equipment in various industrial processes, especially in cement production. Its primary function is to facilitate the calcination of raw materials like limestone, transforming them into cement clinker through high-temperature heating. This process is essential for creating the building blocks of cement, which is a fundamental material in construction. The kiln operates by rotating, ensuring uniform heating and chemical reactions, which are critical for producing high-quality cement.
Key Points Explained:
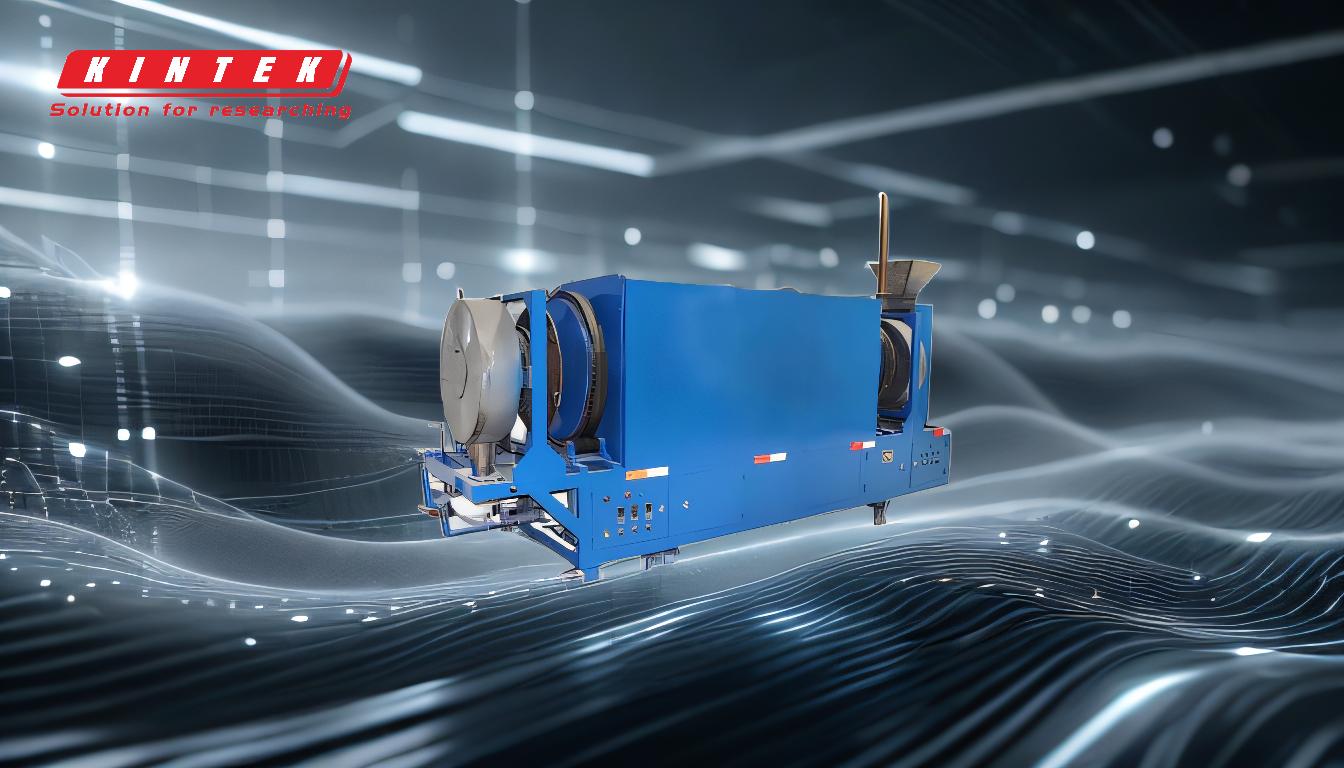
-
Role in Cement Production:
- The rotary kiln is central to cement manufacturing. It is responsible for the calcination process, where limestone (calcium carbonate) is heated to high temperatures, typically around 1450°C, to produce lime (calcium oxide). This lime then reacts with other materials to form cement clinker.
- The kiln's rotation ensures that the raw materials are evenly heated, promoting consistent chemical reactions and high-quality output.
-
Calcination Process:
- Calcination is a thermal treatment process that causes chemical decomposition or phase transition in the material. In the context of cement production, it involves the breakdown of limestone into lime and carbon dioxide.
- The kiln provides the necessary high-temperature environment for this process, which is critical for the formation of cement clinker.
-
Types of Kilns:
- While the rotary kiln is the most common type used in cement production, there are other types of kilns used in different industries, such as tunnel kilns, periodic kilns, and shuttle kilns. Each type is designed for specific applications and materials.
- The choice of kiln depends on the material being processed and the desired outcome.
-
Energy Efficiency and Environmental Considerations:
- Modern kilns are designed with energy efficiency in mind, incorporating features like heat recovery systems to minimize energy consumption.
- Environmental considerations are also crucial, with many kilns equipped with systems to reduce emissions and manage waste products effectively.
-
Applications Beyond Cement:
- While cement production is the most well-known application, kilns are also used in other industries, such as the production of lime, alumina, and certain types of ceramics.
- In these applications, the kiln serves a similar function, providing the high-temperature environment needed for chemical transformations.
-
Maintenance and Operation:
- Proper maintenance of the kiln is essential to ensure its longevity and efficiency. This includes regular inspections, cleaning, and replacement of worn-out parts.
- Operators must be trained to manage the kiln's temperature and rotation speed to optimize the calcination process and prevent damage to the equipment.
In summary, the kiln, especially the rotary kiln, is indispensable in cement production and other industrial processes requiring high-temperature treatment of materials. Its ability to uniformly heat and chemically transform raw materials makes it a cornerstone of modern manufacturing and construction industries.
Summary Table:
Aspect | Details |
---|---|
Primary Function | Facilitates calcination of raw materials like limestone to produce cement. |
Key Process | High-temperature heating (up to 1450°C) transforms limestone into clinker. |
Types of Kilns | Rotary, tunnel, periodic, and shuttle kilns for various industrial uses. |
Energy Efficiency | Modern kilns feature heat recovery systems to reduce energy consumption. |
Applications | Cement, lime, alumina, and ceramics production. |
Maintenance | Regular inspections and proper operation ensure efficiency and longevity. |
Learn more about how kilns can optimize your industrial processes—contact our experts today!