PVD (Physical Vapor Deposition) coatings are renowned for their exceptional hardness, durability, and versatility. These coatings are widely used in industries requiring high-performance materials, such as microelectronics, optics, and medical devices. The hardness of a PVD coating depends on the specific material used, with some coatings achieving extreme levels of hardness due to their unique properties and deposition processes. Among the hardest PVD coatings are those based on diamond-like carbon (DLC) and titanium nitride (TiN), which are known for their superior wear resistance, high-temperature stability, and excellent adhesion to substrates. This makes them ideal for applications requiring extreme durability and performance.
Key Points Explained:
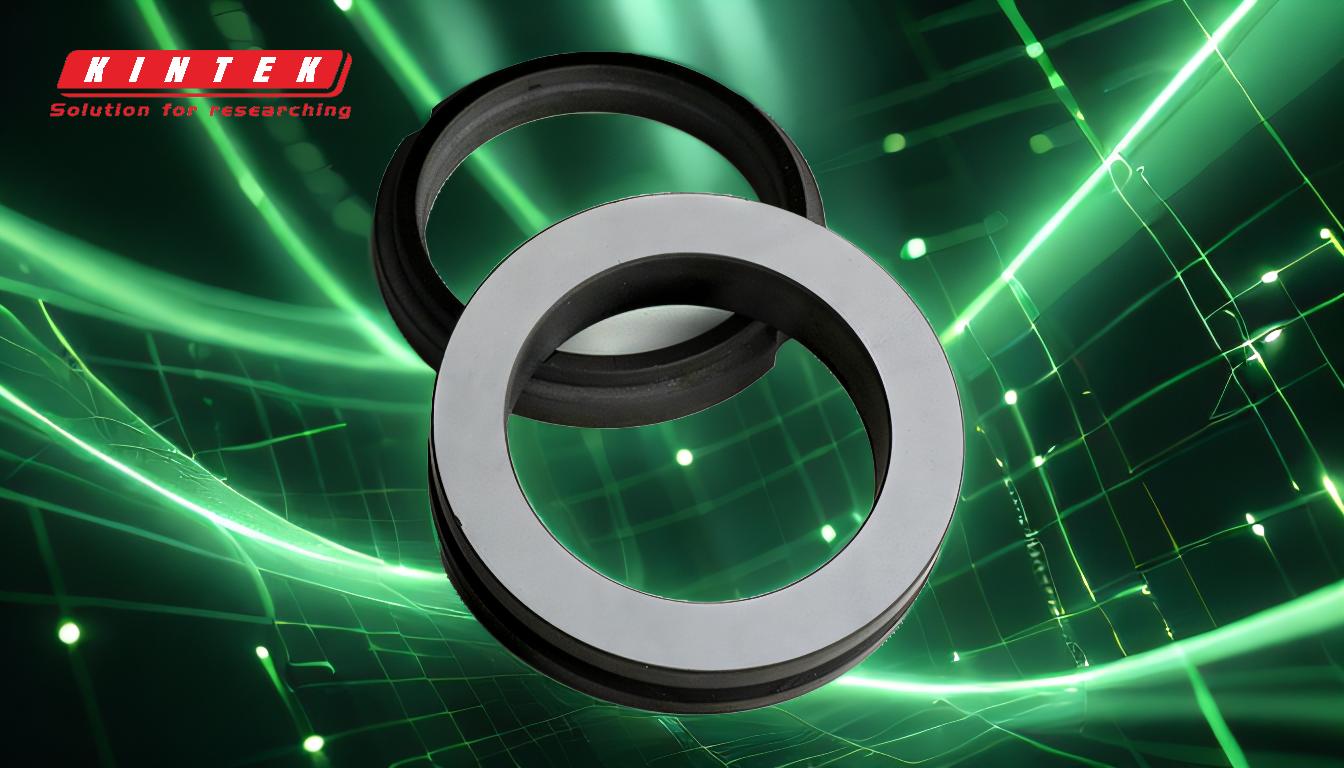
-
What Makes PVD Coatings Hard?
- PVD coatings are created through a process where a solid material is vaporized in a vacuum and then deposited onto a substrate. This process allows for precise control over the coating's properties, including hardness.
- The hardness of PVD coatings is influenced by the material used, the deposition process, and the resulting microstructure. Materials like diamond-like carbon (DLC) and titanium nitride (TiN) are particularly hard due to their strong atomic bonds and dense structures.
-
Diamond-Like Carbon (DLC) Coatings
- DLC coatings are among the hardest PVD coatings available. They consist of a mixture of sp2 (graphite-like) and sp3 (diamond-like) carbon bonds, which give them exceptional hardness and wear resistance.
- These coatings are used in applications requiring extreme durability, such as cutting tools, automotive components, and medical devices. They also exhibit low friction and high chemical inertness.
-
Titanium Nitride (TiN) Coatings
- TiN coatings are another example of extremely hard PVD coatings. They are known for their golden color and are widely used in industrial applications, including cutting tools and machine components.
- TiN coatings provide excellent hardness, wear resistance, and thermal stability, making them suitable for high-stress environments.
-
Other Hard PVD Coatings
- Other hard PVD coatings include titanium aluminum nitride (TiAlN), chromium nitride (CrN), and zirconium nitride (ZrN). These coatings offer a balance of hardness, corrosion resistance, and thermal stability, making them suitable for specialized applications.
- The choice of coating depends on the specific requirements of the application, such as the operating environment, substrate material, and desired performance attributes.
-
Advantages of Hard PVD Coatings
- Durability: Hard PVD coatings are highly resistant to wear, abrasion, and impact, extending the lifespan of coated components.
- High-Temperature Stability: These coatings can withstand extreme temperatures, making them suitable for high-temperature applications.
- Versatility: PVD coatings can be applied to a wide range of substrates, including metals, ceramics, and polymers.
- Precision and Control: The PVD process allows for precise control over the coating's thickness, composition, and properties, ensuring optimal performance.
-
Applications of Hard PVD Coatings
- Industrial Tools: Cutting tools, drills, and molds benefit from the hardness and wear resistance of PVD coatings.
- Aerospace and Automotive: Components exposed to high stress and temperature, such as engine parts and turbine blades, are often coated with hard PVD materials.
- Medical Devices: Surgical instruments and implants use PVD coatings for their biocompatibility and durability.
- Electronics and Optics: PVD coatings are used in microchips, optical lenses, and solar panels due to their purity and performance attributes.
In summary, the hardest PVD coatings, such as DLC and TiN, are highly valued for their exceptional hardness, durability, and versatility. These coatings are essential in industries requiring materials that can withstand extreme conditions and provide long-lasting performance. The precise control offered by the PVD process ensures that these coatings meet the specific needs of various applications, making them a critical component in modern manufacturing and technology.
Summary Table:
Coating Type | Key Properties | Applications |
---|---|---|
Diamond-Like Carbon (DLC) | Extreme hardness, low friction, high chemical inertness | Cutting tools, automotive components, medical devices |
Titanium Nitride (TiN) | Excellent hardness, wear resistance, thermal stability | Industrial tools, machine components |
Titanium Aluminum Nitride (TiAlN) | Balanced hardness, corrosion resistance, thermal stability | Specialized industrial applications |
Chromium Nitride (CrN) | High hardness, corrosion resistance | Aerospace, automotive, and medical industries |
Zirconium Nitride (ZrN) | Superior hardness, thermal stability | Electronics, optics, and high-stress environments |
Find the perfect PVD coating for your application—contact our experts today to get started!