A heat treatment process furnace is a specialized piece of equipment designed to alter the physical and chemical properties of materials through controlled heating and cooling processes. These furnaces are essential in industries such as metallurgy, manufacturing, and materials science, where precise thermal processing is required to achieve desired material characteristics like hardness, strength, or ductility. Heat treatment furnaces come in various types, including retort furnaces, vacuum furnaces, and induction heating furnaces, each tailored for specific applications. They typically consist of key components such as heating chambers, cooling systems, and control mechanisms to ensure uniform and efficient heat treatment. Understanding the working principles and components of these furnaces is crucial for selecting the right equipment for specific heat treatment processes.
Key Points Explained:
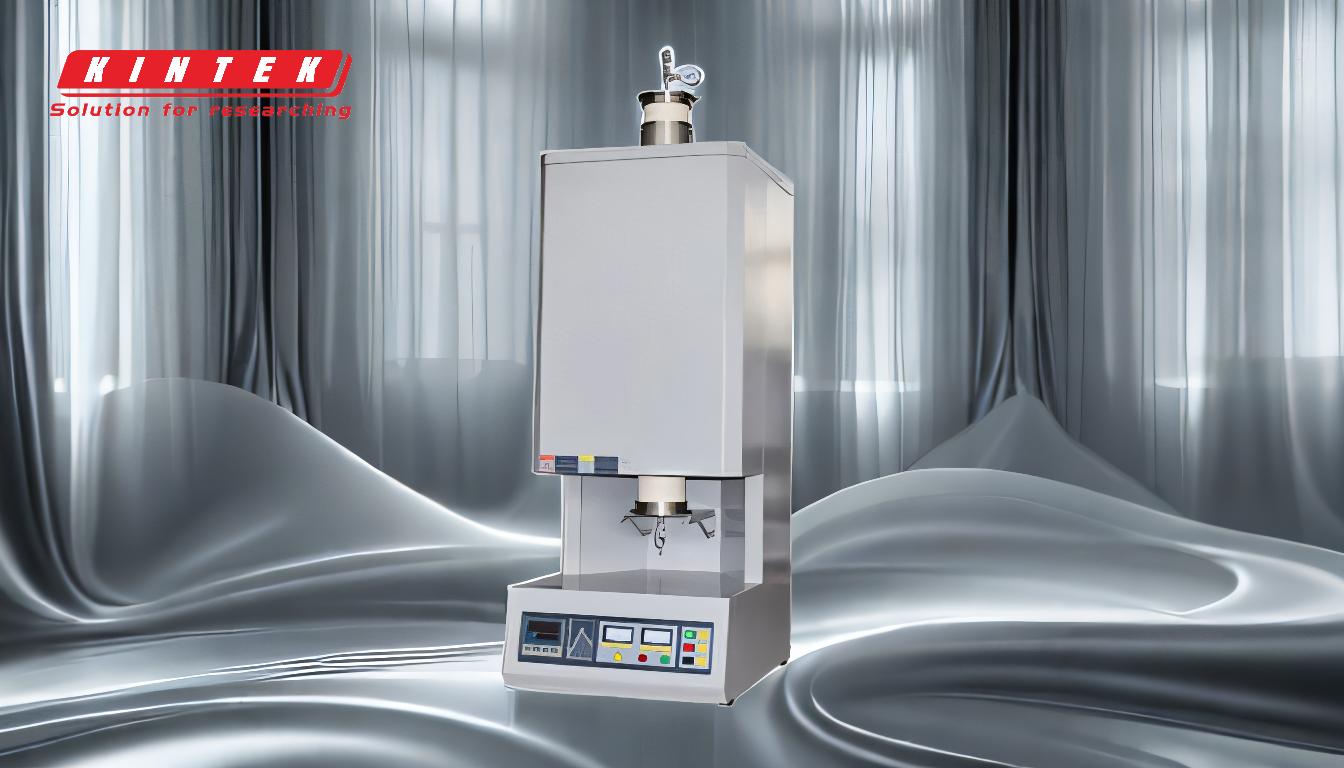
-
Purpose of Heat Treatment Furnaces:
- Heat treatment furnaces are used to modify the physical and chemical properties of materials, such as metals and alloys, through controlled heating and cooling cycles.
- Common heat treatment processes include annealing, quenching, tempering, and case hardening, each requiring precise temperature control and timing.
-
Types of Heat Treatment Furnaces:
- Retort Furnace: This type of furnace consists of two interconnected chambers—a hot chamber for heating and a fast cooling chamber. It is often used for processes requiring controlled atmospheres, such as gas carburizing or nitriding.
- Vacuum Furnace: Operates in a low-pressure environment, ideal for processes requiring minimal oxidation or contamination. It includes components like a vacuum system, heating elements, and a cooling system.
- Induction Heating Furnace: Uses electromagnetic induction to heat conductive materials internally, ensuring uniform heating without direct contact.
-
Key Components of Heat Treatment Furnaces:
- Heating Chamber: The core component where materials are heated to the desired temperature. It may include electric heating elements, gas burners, or induction coils.
- Cooling System: Essential for controlled cooling after heating. This can include water-cooled or air-cooled chambers, depending on the furnace type.
- Control System: Manages temperature, pressure, and timing to ensure precise heat treatment. Advanced furnaces use programmable logic controllers (PLCs) for automation.
-
Working Principles:
- Retort Furnace: Materials are heated in the hot chamber and then transferred to the cooling chamber for rapid cooling, ensuring controlled thermal cycles.
- Vacuum Furnace: Creates a low-pressure environment to prevent oxidation. Heat is generated through electric heating elements, and cooling is achieved via steam condensation or forced convection.
- Induction Heating Furnace: Alternating current through a copper coil generates an electromagnetic field, inducing eddy currents in the material for internal heating.
-
Applications of Heat Treatment Furnaces:
- Used in industries like aerospace, automotive, and tool manufacturing to enhance material properties such as hardness, strength, and wear resistance.
- Specific applications include annealing of metals, hardening of steel, and brazing of components.
-
Advantages of Heat Treatment Furnaces:
- Precision: Allows for exact control of temperature and cooling rates, ensuring consistent results.
- Efficiency: Modern furnaces are designed to minimize energy consumption while maximizing throughput.
- Versatility: Suitable for a wide range of materials and heat treatment processes.
-
Considerations for Purchasing:
- Capacity: Ensure the furnace can handle the required material size and volume.
- Temperature Range: Choose a furnace that meets the maximum and minimum temperature requirements for your processes.
- Atmosphere Control: For processes requiring specific atmospheres (e.g., inert gas or vacuum), select a furnace with appropriate controls.
- Automation: Advanced control systems can improve process repeatability and reduce labor costs.
By understanding these key points, purchasers can make informed decisions when selecting a heat treatment process furnace, ensuring it meets their specific industrial needs.
Summary Table:
Aspect | Details |
---|---|
Purpose | Modifies physical and chemical properties of materials through heating and cooling. |
Types | Retort, Vacuum, Induction Heating Furnaces. |
Key Components | Heating Chamber, Cooling System, Control System. |
Applications | Aerospace, automotive, tool manufacturing. |
Advantages | Precision, efficiency, versatility. |
Considerations | Capacity, temperature range, atmosphere control, automation. |
Ready to enhance your material processing? Contact us today to find the perfect heat treatment furnace for your needs!