The heating rate in sintering plays a critical role in determining the quality and properties of the final product. It influences the densification process, uniformity of sintering, and the overall material properties. A heating rate that is too high can lead to insufficient sintering, uneven densification, and undesirable material characteristics such as high crystallinity and melting peaks. Conversely, an optimal heating rate ensures uniform sintering, proper densification, and enhanced mechanical properties like tensile strength and fatigue resistance. Factors such as material type, particle size, and furnace conditions must be considered to determine the appropriate heating rate for specific sintering applications.
Key Points Explained:
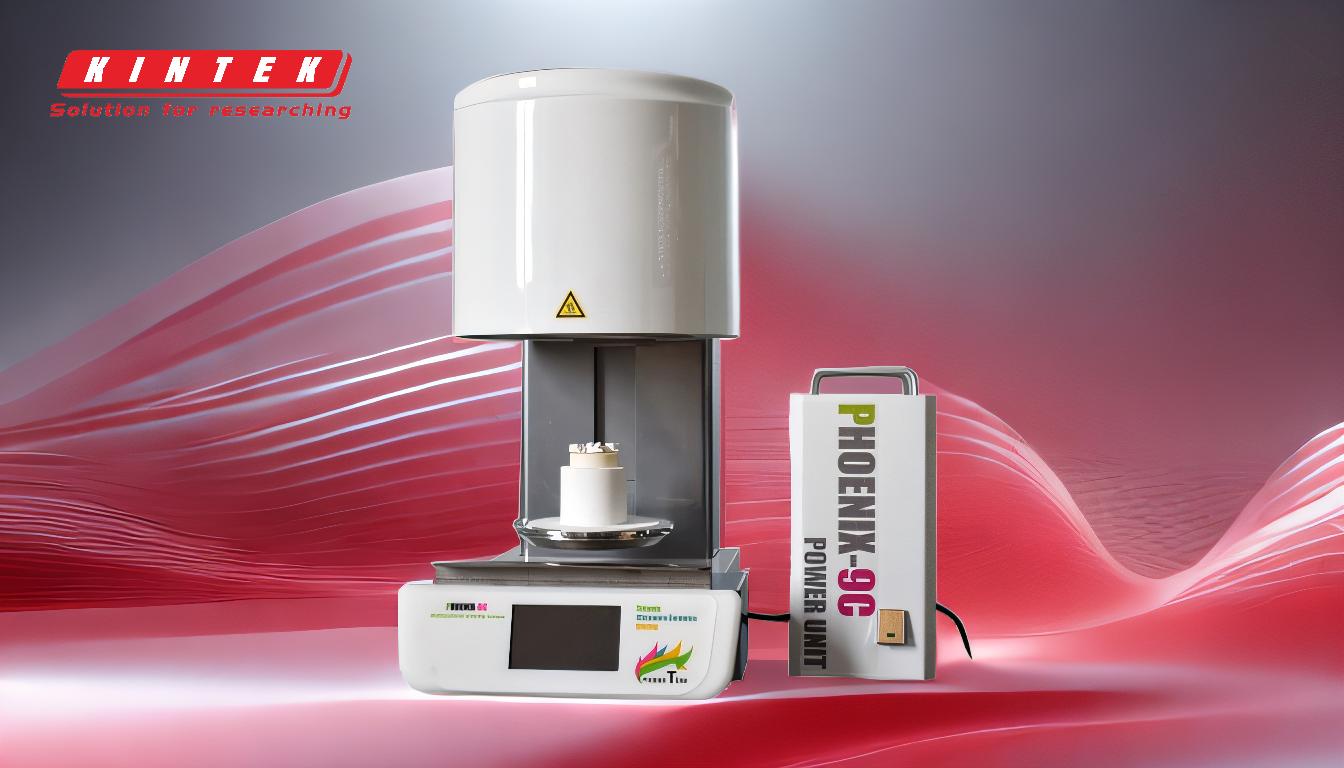
-
Definition and Importance of Heating Rate in Sintering:
- The heating rate refers to the speed at which the temperature is increased during the sintering process.
- It is a critical parameter because it directly affects the densification of the material, the uniformity of sintering, and the final mechanical properties of the product.
-
Consequences of High Heating Rates:
- Insufficient Sintering: A high heating rate can lead to insufficient sintering inside the material, resulting in poor densification and weak internal bonds.
- Uneven Sintering: Rapid heating can cause significant differences in sintering degrees across different areas of the material, leading to non-uniform properties.
- High-Temperature Melting Peaks: Excessive heating rates can cause localized melting, resulting in high-temperature melting peaks and increased crystallinity, which may degrade material performance.
-
Optimal Heating Rate for Uniform Sintering:
- The heating rate must be carefully controlled to ensure uniform sintering and proper densification.
- An optimal heating rate allows for gradual temperature increases, enabling the material to achieve uniform density and mechanical properties across all regions.
-
Factors Influencing Heating Rate:
- Material Type: Different materials require specific heating rates based on their thermal properties and sintering behavior.
- Particle Size: Smaller particles generally require lower heating rates to achieve uniform densification.
- Furnace Conditions: The type of furnace (e.g., belt conveyor, push, or batch furnace) and the atmospheric conditions (e.g., air, vacuum, or inert gas) influence the heating rate and sintering outcomes.
-
Impact of Heating Rate on Material Properties:
- Mechanical Properties: Proper heating rates enhance tensile strength, bending fatigue strength, and impact energy.
- Densification: Controlled heating rates promote better particle rearrangement and porosity elimination, leading to higher density and improved material performance.
-
Role of Thermocouples in Controlling Heating Rate:
- The quality and type of thermocouples used in the sintering furnace play a crucial role in monitoring and controlling the heating rate.
- Dual-core thermocouples are recommended for accurate temperature measurement and consistent heating rates.
-
Practical Considerations for Equipment Purchasers:
- When selecting sintering equipment, purchasers should consider the compatibility of the heating rate with the intended materials and desired product properties.
- Ensure the furnace has precise temperature control mechanisms and high-quality thermocouples to maintain optimal heating rates.
-
Summary of Key Takeaways:
- The heating rate is a vital parameter in sintering that affects densification, uniformity, and material properties.
- High heating rates can lead to insufficient sintering, uneven densification, and undesirable material characteristics.
- Optimal heating rates, influenced by material type, particle size, and furnace conditions, ensure uniform sintering and enhanced mechanical properties.
- Equipment purchasers should prioritize precise temperature control and high-quality thermocouples to achieve consistent and effective sintering outcomes.
Summary Table:
Key Factor | Impact on Sintering |
---|---|
High Heating Rate | Insufficient sintering, uneven densification, high crystallinity, and melting peaks. |
Optimal Heating Rate | Uniform sintering, proper densification, enhanced mechanical properties. |
Material Type | Determines specific heating rate requirements for effective sintering. |
Particle Size | Smaller particles require lower heating rates for uniform densification. |
Furnace Conditions | Influences heating rate and sintering outcomes based on type and atmosphere. |
Thermocouples | Dual-core thermocouples ensure accurate temperature control for consistent heating. |
Need help optimizing your sintering process? Contact our experts today for tailored solutions!