The highest sintering temperature can vary significantly depending on the material being processed, the desired properties of the final product, and the type of sintering furnace used. Based on the references provided, sintering temperatures can range from as low as 1120°C to as high as 1800°C. The maximum operating temperature for standard sintering furnaces is typically up to 1120°C, while specialized sintering kilns can reach temperatures of 1288°C/2350°F. In experimental settings, sintering temperatures as high as 1800°C have been used. The choice of temperature is influenced by factors such as material composition, particle size, required density, and the desired mechanical properties of the final product.
Key Points Explained:
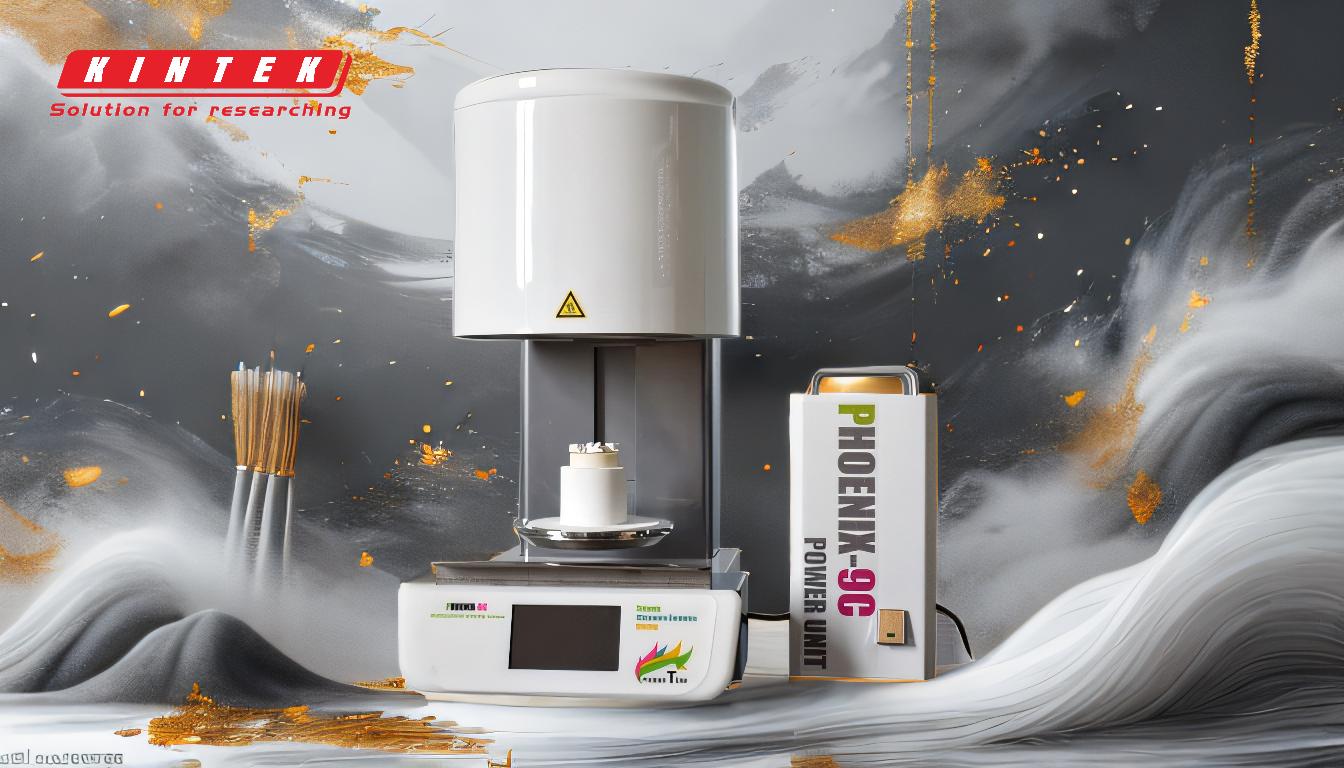
-
Range of Sintering Temperatures:
- Sintering temperatures can vary widely depending on the material and application. Standard sintering furnaces typically operate up to 1120°C, while specialized kilns can reach 1288°C/2350°F. In experimental conditions, temperatures as high as 1800°C have been employed.
- Why it matters: The temperature range is critical because it directly impacts the density, strength, and other mechanical properties of the sintered product. Higher temperatures generally lead to better densification and improved mechanical properties but must be balanced against material limitations and energy costs.
-
Factors Influencing Sintering Temperature:
- Material Composition: Different materials have different melting points and sintering behaviors. For example, ceramics and metals require different temperature ranges for optimal sintering.
- Particle Size: Finer powders typically sinter at lower temperatures due to their higher surface area, which enhances particle bonding.
- Desired Properties: The required density, tensile strength, and other mechanical properties of the final product influence the choice of sintering temperature.
- Atmosphere: The sintering atmosphere (e.g., air, vacuum, argon/nitrogen) can affect the sintering process and the maximum temperature that can be safely used.
- Why it matters: Understanding these factors helps in selecting the appropriate sintering temperature to achieve the desired product characteristics without damaging the material or the furnace.
-
High-Temperature Sintering Benefits:
- High-temperature sintering can significantly enhance the mechanical properties of the final product, including tensile strength, bending fatigue strength, and impact energy.
- Why it matters: For applications requiring high-performance materials, such as aerospace or automotive components, high-temperature sintering is essential to achieve the necessary strength and durability.
-
Equipment Limitations:
- The maximum operating temperature of sintering furnaces and kilns is a limiting factor. Standard furnaces typically max out at 1120°C, while specialized kilns can reach 1288°C/2350°F. Experimental setups may achieve even higher temperatures, such as 1800°C.
- Why it matters: The choice of equipment is crucial for achieving the desired sintering temperature. Using equipment that cannot reach the required temperature can result in suboptimal product properties.
-
Experimental vs. Industrial Sintering:
- In experimental settings, sintering temperatures can be pushed to extremes, such as 1800°C, to explore the limits of material properties and sintering behaviors.
- In industrial applications, the focus is often on balancing temperature with cost, energy efficiency, and equipment capabilities, typically resulting in lower maximum temperatures.
- Why it matters: Experimental data can inform industrial practices, but practical constraints often limit the temperatures used in large-scale production.
-
Optimal Sintering Parameters:
- The optimal sintering process is influenced by parameters such as temperature, applied pressure, average grain size, and gaseous atmosphere. Higher temperatures and finer powders can increase compaction, but the amount of liquid phase must be carefully controlled.
- Why it matters: Achieving the right balance of these parameters is essential for producing high-quality sintered products with the desired properties.
In summary, the highest sintering temperature depends on the material, desired properties, and equipment used, with standard furnaces reaching up to 1120°C, specialized kilns up to 1288°C/2350°F, and experimental setups potentially reaching 1800°C. Understanding the factors influencing sintering temperature and the limitations of available equipment is crucial for selecting the appropriate sintering conditions.
Summary Table:
Aspect | Details |
---|---|
Standard Furnace Range | Up to 1120°C |
Specialized Kiln Range | Up to 1288°C/2350°F |
Experimental Range | Up to 1800°C |
Key Influencing Factors | Material composition, particle size, desired properties, sintering atmosphere |
Benefits of High Temp | Enhanced tensile strength, bending fatigue strength, and impact energy |
Need help selecting the right sintering temperature for your application? Contact our experts today!