Brazing is a metal-joining process that involves melting a filler metal into a joint between two or more base metals. The highest temperature for brazing typically depends on the materials being joined and the type of filler metal used. Generally, brazing temperatures range from 450°C to 1200°C (840°F to 2200°F). However, the specific temperature must be carefully selected to avoid damaging the base metals while ensuring proper flow and adhesion of the filler metal. Factors such as the melting point of the filler metal, the thermal properties of the base metals, and the desired joint strength all play a role in determining the optimal brazing temperature.
Key Points Explained:
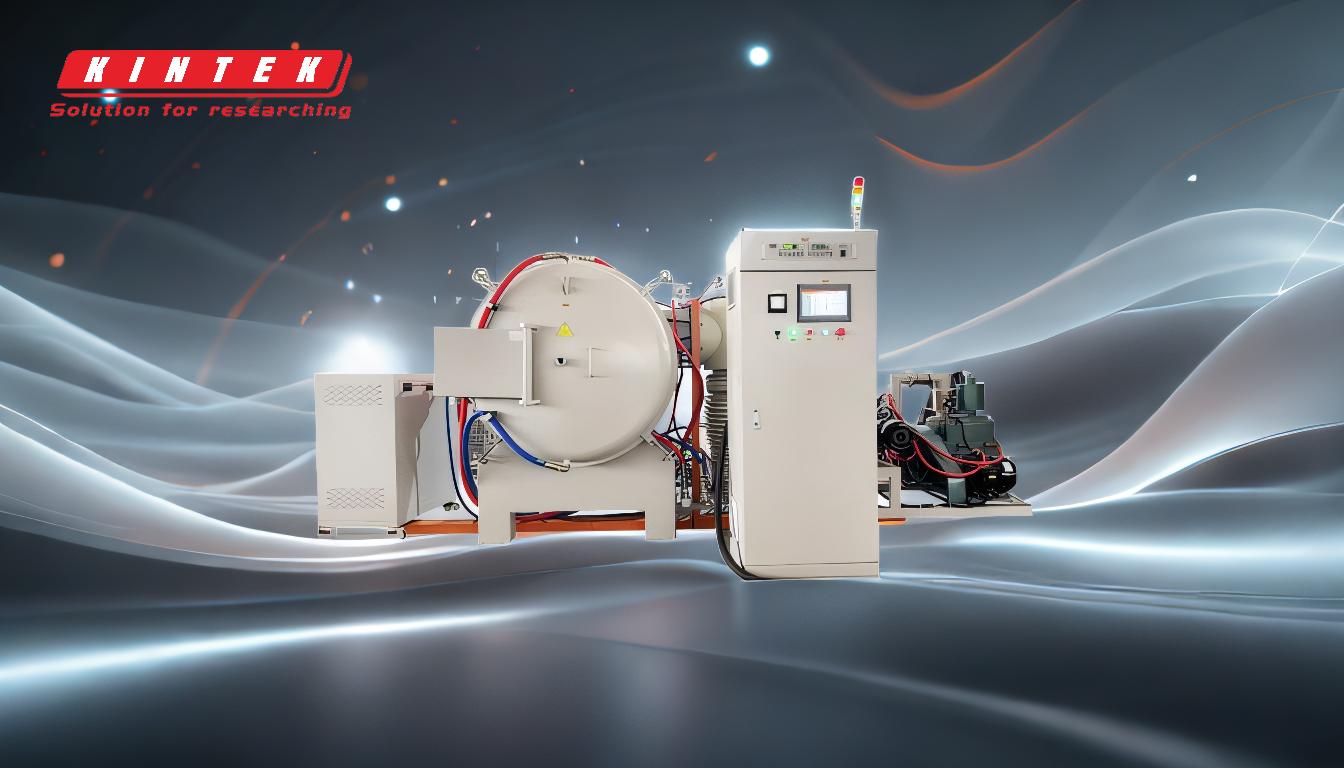
-
Definition and Process of Brazing:
- Brazing is a metal-joining process where a filler metal is melted and flowed into the joint between two or more base metals.
- The filler metal has a lower melting point than the base metals, ensuring that the base metals do not melt during the process.
-
Temperature Range for Brazing:
- Brazing typically occurs at temperatures between 450°C and 1200°C (840°F to 2200°F).
- The exact temperature depends on the materials being joined and the type of filler metal used.
-
Factors Influencing Brazing Temperature:
- Melting Point of Filler Metal: The filler metal must melt at a temperature lower than the base metals but high enough to ensure proper flow and adhesion.
- Thermal Properties of Base Metals: The base metals must withstand the brazing temperature without degrading or melting.
- Desired Joint Strength: Higher temperatures can improve joint strength but may risk damaging the base metals.
-
Types of Filler Metals and Their Temperature Ranges:
- Silver-Based Filler Metals: Typically used at temperatures between 600°C and 900°C (1112°F and 1652°F).
- Copper-Based Filler Metals: Often used at higher temperatures, around 900°C to 1100°C (1652°F to 2012°F).
- Nickel-Based Filler Metals: Used for high-temperature applications, with brazing temperatures up to 1200°C (2200°F).
-
Applications of High-Temperature Brazing:
- High-temperature brazing is used in industries such as aerospace, automotive, and power generation, where joints must withstand extreme conditions.
- Examples include turbine blades, heat exchangers, and exhaust systems.
-
Considerations for Selecting Brazing Temperature:
- Material Compatibility: Ensure that the base metals and filler metal are compatible at the selected temperature.
- Joint Design: The design of the joint can influence the optimal brazing temperature.
- Atmosphere Control: In some cases, a controlled atmosphere (e.g., vacuum or inert gas) is necessary to prevent oxidation and ensure a strong joint.
-
Safety and Equipment Requirements:
- High-temperature brazing requires specialized equipment, such as furnaces or torches, capable of reaching and maintaining the required temperatures.
- Safety precautions, including proper ventilation and protective gear, are essential to protect operators from high temperatures and fumes.
By understanding these key points, you can determine the appropriate brazing temperature for your specific application, ensuring a strong and durable joint while minimizing the risk of damage to the base metals.
Summary Table:
Aspect | Details |
---|---|
Temperature Range | 450°C to 1200°C (840°F to 2200°F) |
Filler Metal Types | Silver-Based (600°C–900°C), Copper-Based (900°C–1100°C), Nickel-Based (up to 1200°C) |
Key Factors | Melting point of filler metal, thermal properties of base metals, joint strength |
Applications | Aerospace, automotive, power generation (e.g., turbine blades, heat exchangers) |
Safety & Equipment | Specialized furnaces or torches, proper ventilation, and protective gear |
Need help determining the right brazing temperature for your project? Contact our experts today!