The highest temperature heating elements are typically made from materials that can withstand extreme heat without degrading. Among the most common materials used for such heating elements are silicon carbide (SiC), molybdenum disilicide (MoSi2), and tungsten. Silicon carbide heating elements can operate up to 1600°C, while molybdenum disilicide can reach up to 1800°C. Tungsten, however, stands out as it can withstand temperatures up to 3000°C, making it the highest temperature-resistant material used in heating elements. These materials are chosen based on their thermal stability, resistance to oxidation, and mechanical strength at high temperatures.
Key Points Explained:
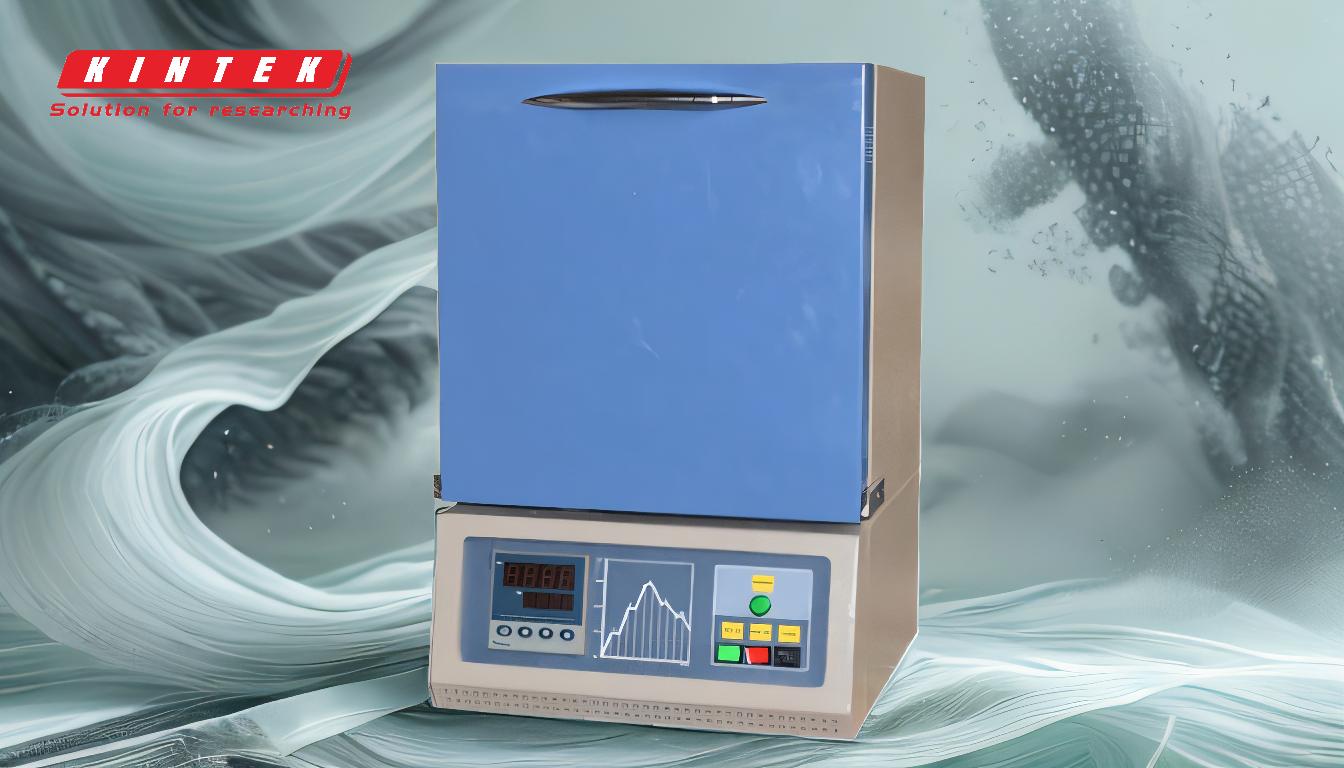
-
Silicon Carbide (SiC) Heating Elements:
- Temperature Range: Up to 1600°C.
- Properties: Silicon carbide is a ceramic material known for its high thermal conductivity, low thermal expansion, and excellent resistance to thermal shock. It is widely used in industrial furnaces and kilns.
- Applications: Commonly used in applications requiring high-temperature heating, such as ceramic sintering, metal heat treatment, and glass manufacturing.
-
Molybdenum Disilicide (MoSi2) Heating Elements:
- Temperature Range: Up to 1800°C.
- Properties: Molybdenum disilicide is a refractory ceramic compound that exhibits high melting points and excellent oxidation resistance. It forms a protective layer of silicon dioxide at high temperatures, which prevents further oxidation.
- Applications: Often used in high-temperature furnaces for processes like annealing, sintering, and crystal growth.
-
Tungsten Heating Elements:
- Temperature Range: Up to 3000°C.
- Properties: Tungsten has the highest melting point of all metals (3422°C) and maintains its strength at high temperatures. It is also highly resistant to thermal shock and has low vapor pressure at elevated temperatures.
- Applications: Used in specialized high-temperature environments such as vacuum furnaces, semiconductor manufacturing, and aerospace applications.
-
Factors Influencing the Choice of Heating Elements:
- Thermal Stability: The material must maintain its structural integrity at high temperatures.
- Oxidation Resistance: The ability to resist oxidation is crucial for longevity and performance.
- Mechanical Strength: The material should not deform or fail under thermal stress.
- Cost and Availability: While tungsten offers the highest temperature resistance, it is also more expensive and less readily available compared to silicon carbide and molybdenum disilicide.
-
Electric Heating Element Considerations:
- Design and Configuration: The design of the electric heating element must ensure efficient heat transfer and uniform temperature distribution.
- Power Supply: High-temperature heating elements require robust power supplies capable of delivering consistent energy without fluctuations.
- Cooling Systems: In some applications, cooling systems may be necessary to manage the extreme heat generated by these elements.
In summary, the choice of the highest temperature heating element depends on the specific application requirements, including the maximum temperature needed, the environment (oxidizing or inert), and the budget. Tungsten stands out for the highest temperature applications, but silicon carbide and molybdenum disilicide are also excellent choices for slightly lower temperature ranges.
Summary Table:
Material | Temperature Range | Key Properties | Applications |
---|---|---|---|
Silicon Carbide (SiC) | Up to 1600°C | High thermal conductivity, low thermal expansion, excellent thermal shock resistance | Ceramic sintering, metal heat treatment, glass manufacturing |
Molybdenum Disilicide (MoSi2) | Up to 1800°C | High melting point, excellent oxidation resistance, forms protective SiO2 layer | Annealing, sintering, crystal growth |
Tungsten | Up to 3000°C | Highest melting point (3422°C), high strength, low vapor pressure at high temps | Vacuum furnaces, semiconductor manufacturing, aerospace applications |
Need help choosing the right heating element for your application? Contact our experts today!