The HIP (Hot Isostatic Pressing) process in powder metallurgy is a technique used to enhance the physical properties of materials, such as strength and durability, by applying high temperature and pressure simultaneously. This process involves placing the material inside an HIP machine, which consists of a furnace and a pressure vessel. Argon gas is introduced into the vessel, increasing both temperature and pressure. After a specific duration, the vessel is cooled, and the treated material is removed. The HIP process is particularly effective in eliminating porosity and improving the mechanical properties of the material.
Key Points Explained:
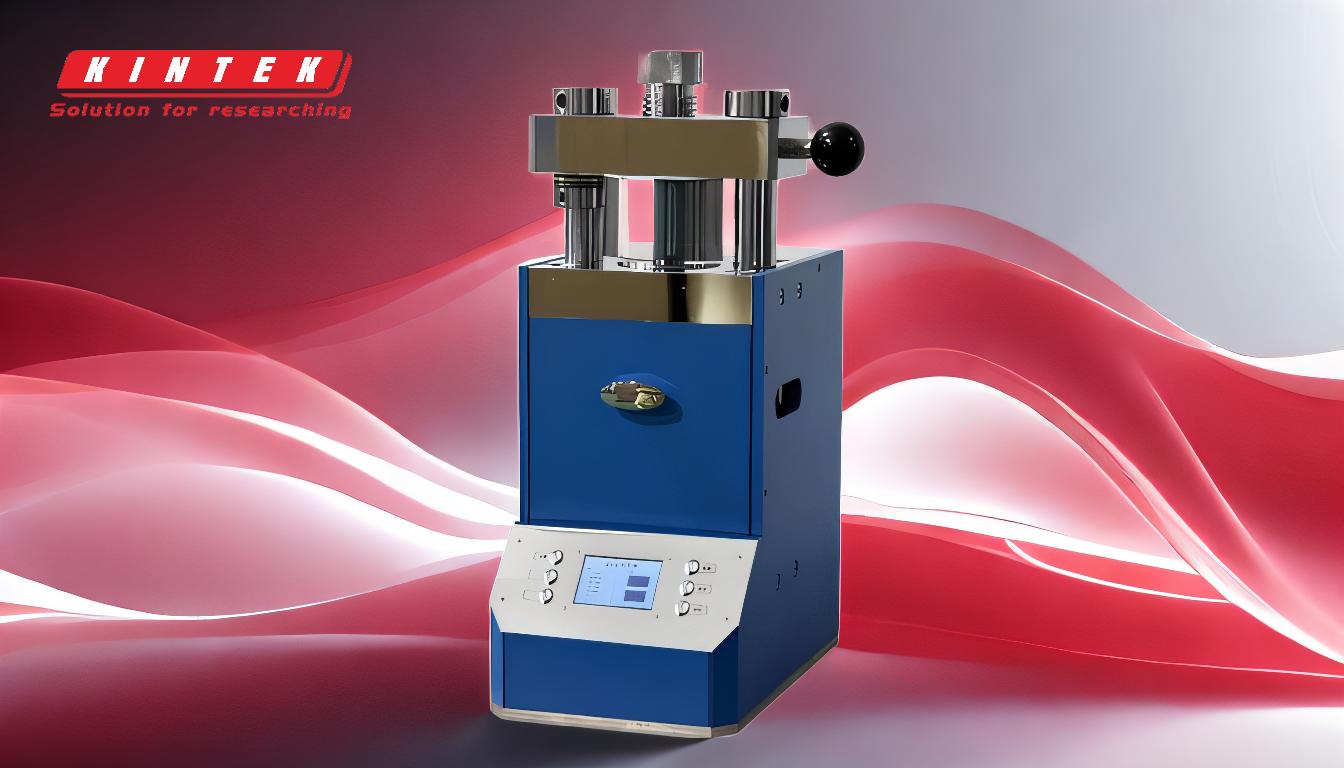
-
Components of the HIP Machine:
- The HIP machine is equipped with a furnace and a pressure vessel. The furnace is responsible for heating the material, while the pressure vessel applies the necessary pressure to the material during the process.
-
Role of Argon Gas:
- Argon gas is used in the HIP process because it is inert and does not react with the material being treated. The gas is forced into the pressure vessel, which increases the internal pressure and temperature, facilitating the densification of the material.
-
Temperature and Pressure Application:
- The HIP process involves elevating the temperature of the material to just below its melting point while simultaneously applying high pressure. This combination of heat and pressure helps in the diffusion of atoms, leading to the elimination of porosity and the bonding of particles.
-
Cooling and Removal:
- After the material has been subjected to the desired temperature and pressure for a specific amount of time, the vessel is cooled. The cooling process must be controlled to prevent thermal shock, which could damage the material. Once cooled, the treated material is removed from the vessel.
-
Benefits of the HIP Process:
- The HIP process significantly improves the mechanical properties of materials, such as tensile strength, fatigue resistance, and overall durability. It is particularly beneficial for materials used in high-stress environments, such as aerospace components and medical implants.
-
Comparison with Hot Pressing:
- Unlike hot pressing, which combines compaction and sintering in one chamber, the HIP process applies pressure uniformly from all directions. This isotropic pressure application ensures a more uniform densification of the material, leading to better mechanical properties.
-
Stages of Compaction in Powder Metallurgy:
- The HIP process can be compared to the stages of compaction in powder metallurgy, where pressure is applied in stages to achieve a dense and uniform green compact. However, the HIP process goes a step further by applying both heat and pressure simultaneously to achieve a fully dense material.
In summary, the HIP process in powder metallurgy is a sophisticated technique that leverages high temperature and pressure to enhance the properties of materials. By understanding the key components and steps involved, manufacturers can produce materials with superior strength and durability, suitable for demanding applications.
Summary Table:
Key Aspect | Details |
---|---|
Components | Furnace and pressure vessel |
Role of Argon Gas | Inert gas used to increase pressure and temperature for densification |
Temperature & Pressure | Elevated to near melting point with high pressure for atom diffusion |
Cooling & Removal | Controlled cooling to prevent thermal shock; treated material is removed |
Benefits | Improved tensile strength, fatigue resistance, and durability |
Comparison with Hot Pressing | Uniform pressure application ensures better densification and properties |
Learn how the HIP process can transform your materials—contact us today for expert guidance!