The HIP (Hot Isostatic Pressing) process of metal is a specialized powder metallurgy technique that involves applying high temperature and uniform pressure in all directions to a metal powder compact. This process ensures maximum uniformity in density and microstructure, leading to components with enhanced mechanical properties, minimal defects, and near-net shapes. HIP is particularly advantageous for producing complex geometries, improving material strength, and reducing material waste. It is widely used in industries requiring high-performance materials, such as aerospace, medical, and automotive sectors.
Key Points Explained:
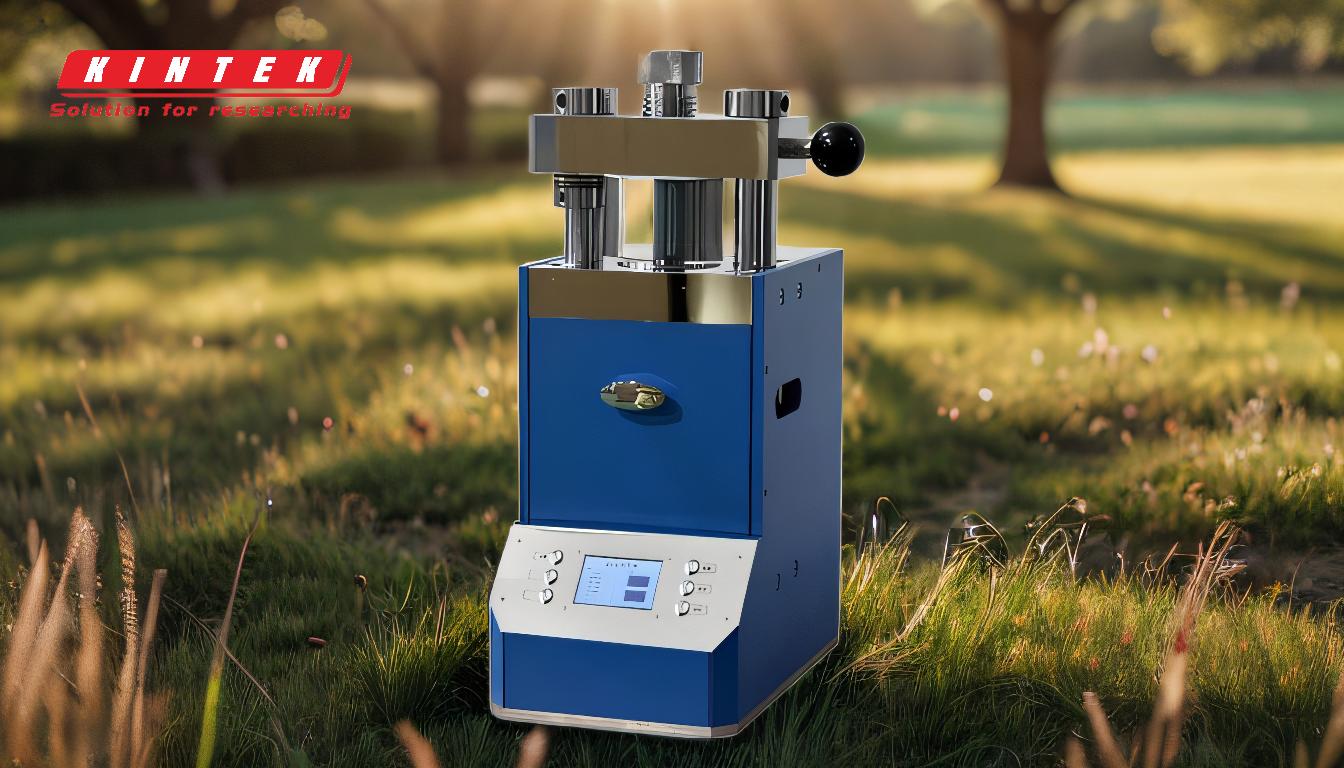
-
Definition of HIP Process:
- HIP (Hot Isostatic Pressing) is a powder metallurgy process that combines high temperature and isostatic pressure to densify and strengthen metal powders or pre-formed components.
- The process involves placing the material in a sealed container, which is then subjected to equal pressure from all directions while being heated to high temperatures.
-
Uniform Pressure Application:
- Unlike uniaxial pressing, which applies pressure in a single direction, HIP applies equal pressure in all directions. This ensures uniform density and microstructure throughout the component, eliminating weak points and defects.
- Uniform pressure application is achieved using a gas, typically argon, which transmits pressure evenly across the material.
-
High Temperature and Pressure:
- The HIP process operates at temperatures ranging from 900°C to 2000°C, depending on the material being processed.
- Pressure levels typically range from 50 MPa to 200 MPa, ensuring complete densification of the material.
-
Advantages of HIP:
- Uniform Strength: The equal pressure application results in components with uniform strength in all directions.
- Complex Geometries: HIP allows for the production of complex shapes that are difficult to achieve with traditional manufacturing methods.
- Reduced Defects: The process eliminates internal voids, porosity, and other defects, leading to improved mechanical properties.
- Near-Net Shape: HIP produces components that are close to their final shape, reducing the need for extensive machining and material waste.
- Enhanced Alloying: The process enables the use of advanced alloys without segregation, improving material performance.
-
Applications of HIP:
- Aerospace: HIP is used to produce high-strength, lightweight components for aircraft engines and structural parts.
- Medical: The process is employed to manufacture biocompatible implants with precise dimensions and high reliability.
- Automotive: HIP is utilized to create durable and lightweight parts for engines, transmissions, and other critical systems.
- Energy: The process is applied in the production of components for nuclear reactors, turbines, and other energy systems.
-
Comparison with Other Powder Metallurgy Techniques:
- HIP offers superior density and microstructure uniformity compared to uniaxial pressing and other conventional methods.
- The process is particularly beneficial for materials that require high performance and reliability, such as superalloys and ceramics.
-
Future Developments:
- Ongoing advancements in HIP technology focus on improving process efficiency, reducing costs, and expanding the range of materials that can be processed.
- Innovations in powder production, alloy development, and binder systems are expected to further enhance the capabilities of HIP.
In summary, the HIP process of metal is a highly effective method for producing high-performance components with uniform properties, complex geometries, and minimal defects. Its applications span across various industries, making it a critical technology in modern manufacturing.
Summary Table:
Key Aspect | Details |
---|---|
Definition | Combines high temperature and isostatic pressure to densify metal powders. |
Pressure Application | Uniform pressure in all directions using gases like argon. |
Temperature Range | 900°C to 2000°C, depending on material. |
Pressure Range | 50 MPa to 200 MPa for complete densification. |
Advantages | Uniform strength, complex geometries, reduced defects, near-net shapes. |
Applications | Aerospace, medical, automotive, and energy industries. |
Learn how the HIP process can revolutionize your manufacturing—contact our experts today!