The history of induction furnaces is rooted in the discovery of electromagnetic induction by Michael Faraday, which laid the foundation for their development. Early experiments were conducted in the late 1870s, with significant milestones including the first patent for melting metals by Edward Allen Colby around 1900 and the first practical use by Kjellin in Sweden in 1900. The technology evolved with the introduction of 3-phase applications in Germany in 1906 and high-frequency furnaces by Edwin F. Northrup in 1916. The vacuum induction melting furnace emerged around 1920, driven by the demand for alloy materials during World War II. Over time, induction furnaces transitioned from small-scale to large-scale operations, significantly improving efficiency and capacity.
Key Points Explained:
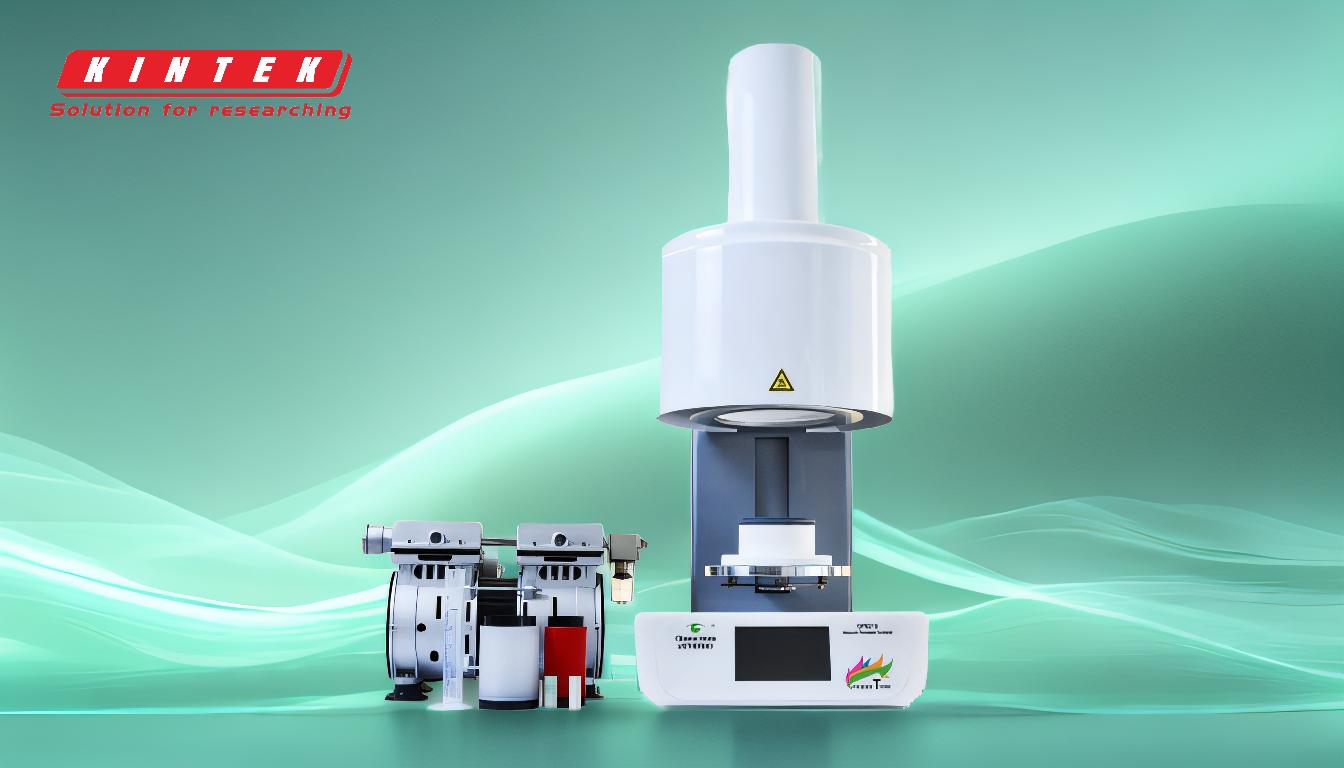
-
Discovery of Electromagnetic Induction:
- The foundation of induction furnace technology lies in Michael Faraday's discovery of electromagnetic induction in the early 19th century. This principle enabled the generation of heat through electromagnetic fields, which became the basis for induction heating and melting processes.
-
Early Experiments and Patents:
- In the late 1870s, Sebastian Z. de Ferranti conducted experiments on induction heating in Europe, leading to the first patent for industrial applications in 1887.
- Edward Allen Colby patented the first induction furnace specifically for melting metals around 1900, marking a significant step in the commercialization of the technology.
-
First Practical Applications:
- The first practical use of an induction furnace was achieved by F. A. Kjellin in Gysinnge, Sweden, in 1900. This demonstrated the feasibility of induction heating for industrial metal melting.
- In 1907, the first steel produced in an induction furnace in the United States was made in a Colby furnace near Philadelphia, showcasing the technology's potential in steel manufacturing.
-
Introduction of 3-Phase Induction Furnaces:
- The first induction furnace designed for 3-phase application was built in Germany in 1906 by Rochling-Rodenhauser. This innovation improved the efficiency and scalability of induction furnaces, making them more suitable for industrial use.
-
High-Frequency Induction Furnaces:
- Edwin F. Northrup implemented the first high-frequency induction furnace application in 1916. This advancement allowed for faster and more precise heating, expanding the range of applications for induction technology.
-
Development of Vacuum Induction Melting (VIM):
- Around 1920, the vacuum induction melting furnace was developed, initially for smelting nickel-chromium alloys. The demand for high-performance alloys during World War II accelerated its development, leading to larger-scale and more efficient operations.
-
Evolution to Modern Induction Furnaces:
- Over the decades, induction furnaces have evolved from small-scale, batch operations to large-scale, continuous or semi-continuous processes. Modern furnaces can handle capacities ranging from several tons to dozens of tons, significantly increasing output and efficiency.
- Today, induction furnaces are widely used in various industries, including steelmaking, foundries, and specialized alloy production, due to their precision, energy efficiency, and environmental benefits.
The history of induction furnaces reflects a continuous evolution driven by scientific discoveries, industrial needs, and technological advancements. From Faraday's foundational work to modern large-scale operations, induction furnaces have become a cornerstone of modern metallurgy and manufacturing.
Summary Table:
Milestone | Year | Key Contributor/Event |
---|---|---|
Discovery of Electromagnetic Induction | Early 19th Century | Michael Faraday |
First Patent for Metal Melting | ~1900 | Edward Allen Colby |
First Practical Use | 1900 | F. A. Kjellin (Sweden) |
3-Phase Induction Furnace | 1906 | Rochling-Rodenhauser (Germany) |
High-Frequency Induction Furnace | 1916 | Edwin F. Northrup |
Vacuum Induction Melting (VIM) | ~1920 | Developed for nickel-chromium alloys |
Modern Large-Scale Operations | 20th-21st Century | Evolved for steelmaking, foundries, and alloys |
Discover how induction furnaces can revolutionize your operations—contact our experts today!