The history of the vacuum furnace is a fascinating journey that reflects advancements in materials science, engineering, and industrial processes. Vacuum furnaces, which are designed to operate in a controlled, low-pressure environment, have evolved significantly since their inception. Initially developed to meet the demands of high-temperature applications in metallurgy and material processing, these furnaces have become indispensable in industries requiring precise thermal treatments, such as aerospace, automotive, and electronics. The ability to operate without oxidation or contamination has made vacuum furnaces a cornerstone of modern manufacturing and research.
Key Points Explained:
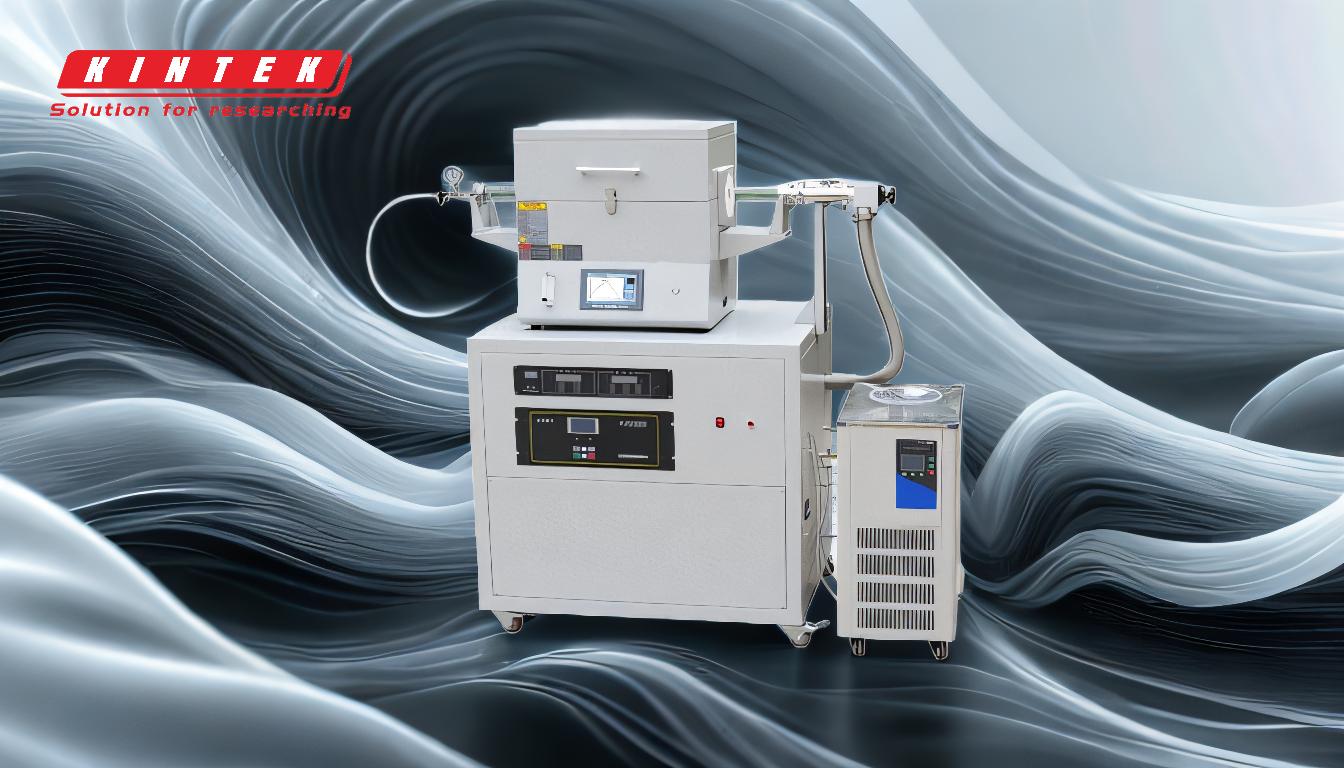
-
Origins and Early Development:
- The concept of vacuum heating dates back to the early 20th century when scientists and engineers began exploring ways to process materials without exposure to atmospheric gases.
- Early vacuum furnaces were rudimentary and primarily used in laboratory settings for experiments involving high-temperature materials.
- The development of vacuum technology during World War II, particularly in the aerospace and defense industries, accelerated the adoption of vacuum furnaces for industrial applications.
-
Advancements in Design and Materials:
- Modern vacuum furnaces incorporate advanced materials, such as fiber insulation in a 'hard pack' or rigidized form, to withstand high convection fan velocities and ensure rapid heat-up and cool-down rates.
- The use of these materials allows the furnace to be opened and unloaded at any required temperature, enhancing operational flexibility.
- Innovations in heating elements, such as graphite or molybdenum, have improved thermal efficiency and durability.
-
Types of Vacuum Furnaces:
- Vacuum furnaces can be categorized based on their heating methods, such as gas-fired or electrically heated systems.
- Electrically heated vacuum furnaces are more common due to their precise temperature control and ability to maintain a consistent vacuum environment.
- Specialized designs, such as horizontal or vertical configurations, cater to specific industrial needs.
-
Applications and Industry Impact:
- Vacuum furnaces are widely used in heat treatment processes, including annealing, brazing, sintering, and hardening, where contamination-free environments are critical.
- Industries such as aerospace, automotive, and electronics rely on vacuum furnaces for producing high-performance components with superior mechanical properties.
- The ability to process materials like titanium, superalloys, and advanced ceramics has expanded the scope of vacuum furnace applications.
-
Future Trends and Innovations:
- Ongoing research focuses on improving energy efficiency, reducing cycle times, and integrating smart technologies for real-time monitoring and control.
- The development of hybrid vacuum furnaces, combining multiple heating methods, is expected to further enhance performance and versatility.
- Sustainability initiatives are driving the adoption of eco-friendly materials and processes in vacuum furnace manufacturing.
For more detailed information on vacuum furnaces, you can explore this resource: vacuum furnace.
The history of the vacuum furnace is a testament to human ingenuity and the relentless pursuit of technological advancement. From humble beginnings to becoming a critical tool in modern industry, vacuum furnaces continue to push the boundaries of what is possible in material processing and thermal treatment.
Summary Table:
Key Milestones | Details |
---|---|
Origins and Early Development | - Early 20th century: Concept of vacuum heating. |
- WWII: Accelerated adoption in aerospace and defense industries. | |
Advancements in Design | - Modern materials like fiber insulation improve heat-up and cool-down rates. |
- Innovations in heating elements (graphite, molybdenum) enhance efficiency. | |
Types of Vacuum Furnaces | - Electrically heated systems dominate due to precise temperature control. |
- Specialized designs (horizontal/vertical) cater to industrial needs. | |
Applications | - Used in annealing, brazing, sintering, and hardening processes. |
- Critical in aerospace, automotive, and electronics industries. | |
Future Trends | - Focus on energy efficiency, smart technologies, and hybrid designs. |
Learn how vacuum furnaces can revolutionize your processes—contact our experts today!