Hot isostatic pressing (HIP) is a manufacturing process that applies high temperature and uniform pressure to materials using an inert gas, typically argon, to improve their density, mechanical properties, and microstructure. The process involves loading components into a pressurized vessel, heating the chamber, and applying pressure uniformly from all directions. This eliminates porosity, enhances material properties, and can bond or clad materials. The cycle concludes with controlled depressurization and cooling to ensure safe removal of the processed parts. HIP is widely used in industries like aerospace, automotive, and additive manufacturing to address issues such as porosity, poor layer adhesion, and thermal stresses.
Key Points Explained:
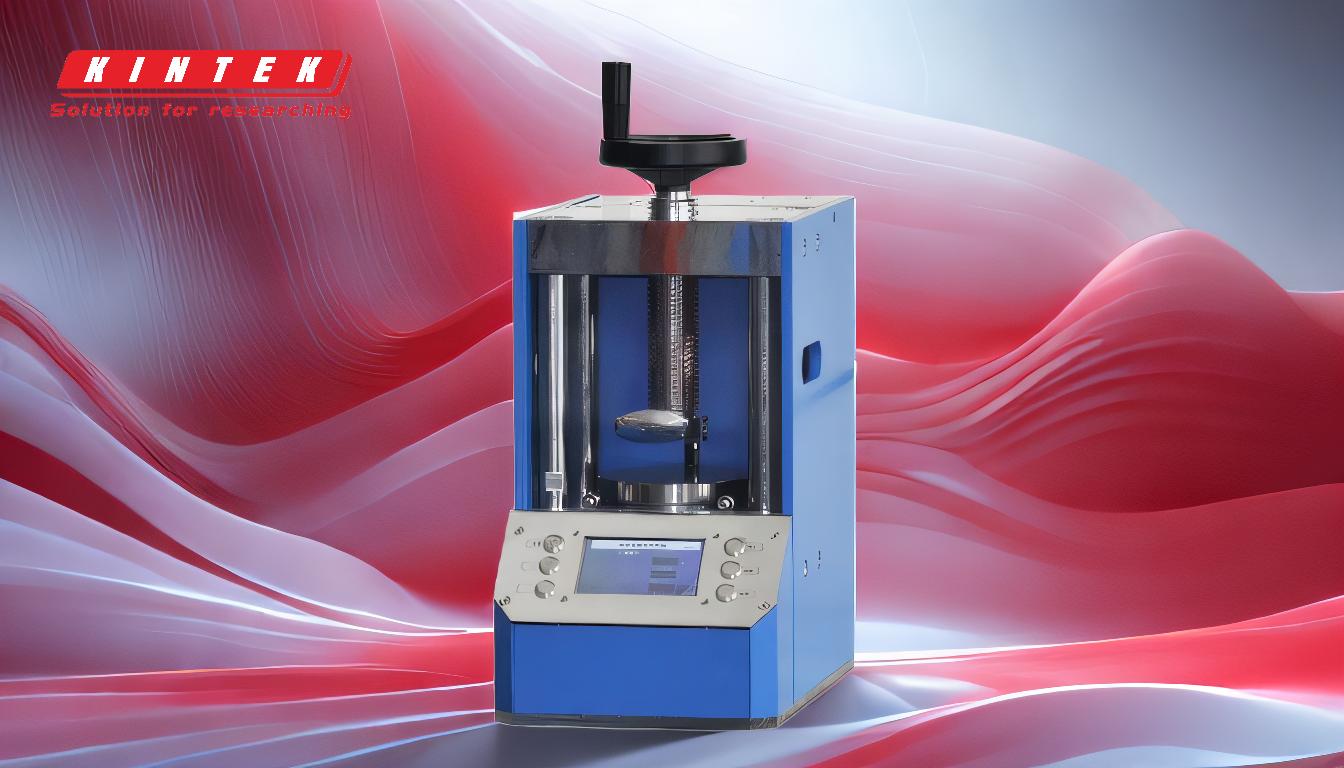
-
Uniform Pressure Application:
- HIP applies pressure uniformly from all directions using an inert gas like argon. This ensures that the material is compressed evenly, eliminating internal voids or pores.
- The uniform pressure helps achieve a denser and more homogeneous material structure, which is critical for improving mechanical properties like strength and fatigue resistance.
-
Temperature and Pressure Control:
- The process involves heating the material below its melting point while applying high pressure. This combination of heat and pressure is carefully monitored and controlled to achieve the desired material properties.
- Temperature control ensures that the material does not melt but reaches a state where it can be reshaped or densified. Pressure is typically applied in the range of 100 to 200 MPa, depending on the material and application.
-
Elimination of Porosity:
- One of the primary benefits of HIP is its ability to eliminate porosity in materials. Porosity, or small gaps within the material, can weaken its structural integrity.
- By applying heat and pressure, HIP closes these gaps, resulting in a denser and more uniform material composition. This is particularly beneficial for cast, sintered, and additively manufactured parts.
-
Bonding and Cladding:
- HIP can bond or clad two or more materials together, either in solid or powder form. This capability is useful for creating composite materials with enhanced properties.
- The process ensures a strong bond between materials, improving the overall performance of the final product.
-
Improvement of Material Properties:
- HIP enhances material properties such as density, ductility, and fatigue resistance. It also relieves thermal stresses that may arise during manufacturing processes like casting or 3D printing.
- For 3D printed parts, HIP addresses issues like poor layer adhesion and porosity, resulting in a more uniform microstructure and better mechanical performance.
-
Consolidation of Manufacturing Steps:
- HIP combines multiple manufacturing steps, such as heat treatment, quenching, and aging, into a single process. This reduces production time and costs while improving the quality of the final product.
- The integration of these steps ensures that the material undergoes all necessary treatments in a controlled environment, leading to consistent and reliable results.
-
Process Cycle:
- The HIP cycle begins with loading the parts or components into a heating chamber. Inert argon gas is then introduced, and the chamber is heated to the desired temperature.
- Pressure is applied uniformly, and the temperature, pressure, and total process time are closely monitored. The cycle ends with a controlled depressurization phase and a cool-down period to ensure the parts are safe to remove.
-
Applications in Additive Manufacturing:
- HIP is particularly valuable in additive manufacturing, where it addresses common issues like porosity and poor layer adhesion. By creating a uniform microstructure, HIP improves the mechanical properties of 3D printed parts.
- This makes HIP an essential post-processing step for high-performance applications in industries like aerospace and automotive.
In summary, the hot isostatic pressing cycle is a highly controlled process that combines heat and pressure to improve material properties, eliminate defects, and consolidate manufacturing steps. Its applications span various industries, making it a critical technology for producing high-quality, reliable components.
Summary Table:
Key Aspect | Description |
---|---|
Uniform Pressure | Applies pressure uniformly from all directions using inert gas (e.g., argon). |
Temperature Control | Heats material below melting point while applying 100-200 MPa pressure. |
Porosity Elimination | Closes internal voids, creating denser and more uniform materials. |
Bonding & Cladding | Bonds or clads materials for enhanced composite properties. |
Material Property Boost | Improves density, ductility, fatigue resistance, and relieves thermal stresses. |
Process Cycle | Includes loading, heating, pressurization, depressurization, and cooling. |
Applications | Widely used in aerospace, automotive, and additive manufacturing industries. |
Discover how HIP technology can transform your manufacturing process—contact our experts today!