The impact factor of Powder Metallurgy Progress has shown variability over the years, reflecting changes in its influence and citation rates within the scientific community. In 2022, the impact factor was 1.4, a notable decrease from 2.228 in 2021. This decline suggests a reduction in the journal's influence or a shift in citation patterns. However, the total number of citations in 2022 (1628) remained relatively stable compared to 2021 (1774), indicating continued relevance. The journal's impact factor has fluctuated between 1.4 and 2.228 over the past four years, with 2021 being the peak year in terms of impact factor and citations.
Key Points Explained:
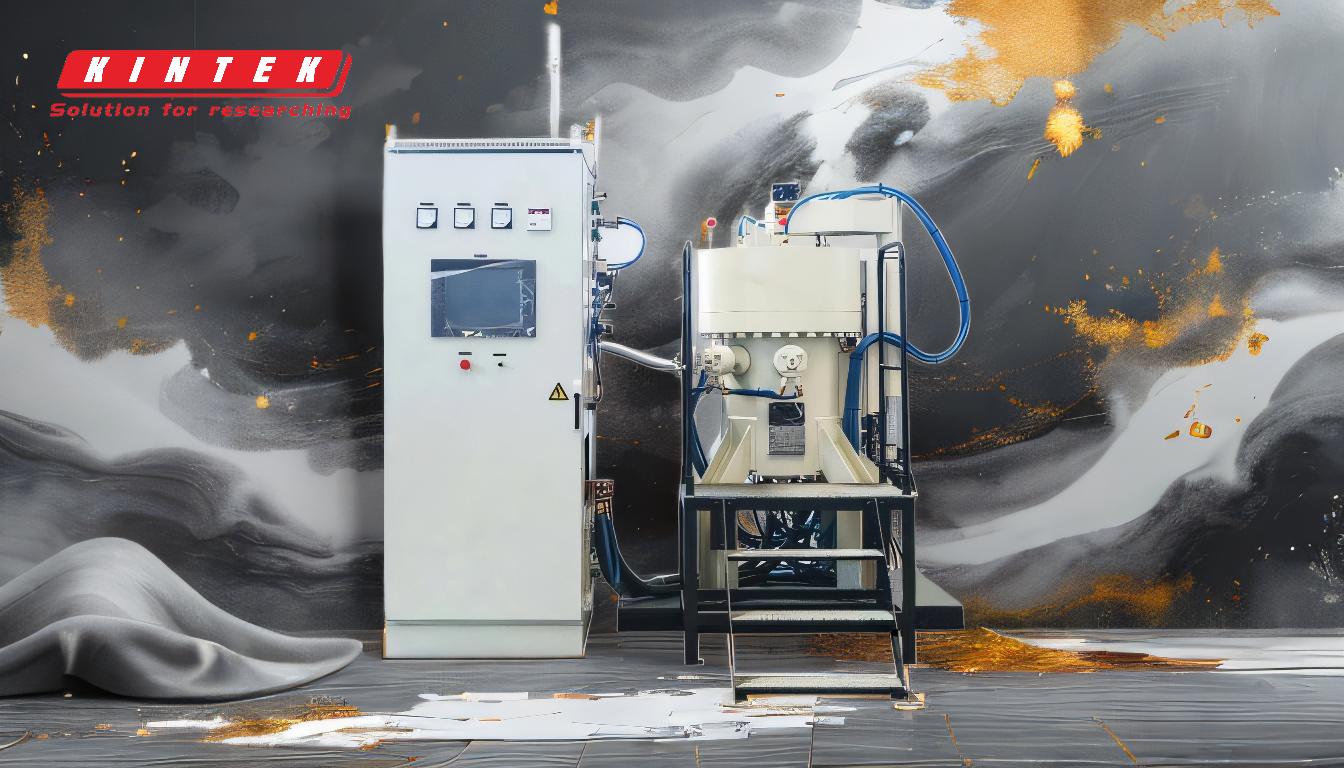
-
Impact Factor Trends:
- The impact factor of Powder Metallurgy Progress has experienced fluctuations over the years. In 2022, it dropped to 1.4 from 2.228 in 2021, marking a significant decline. This could be due to changes in the field, editorial policies, or the quality of published articles.
- The impact factor peaked in 2021 at 2.228, indicating a period of increased influence and recognition within the powder metallurgy community.
-
Citation Analysis:
- Despite the drop in impact factor in 2022, the total number of citations (1628) remained relatively close to the 2021 figure (1774). This suggests that the journal continues to be a relevant source of information for researchers in the field.
- The citation count has shown a general upward trend from 2019 (1342 citations) to 2021 (1774 citations), indicating growing engagement with the journal's content.
-
Implications for Researchers and Purchasers:
- For researchers, the impact factor serves as a metric to gauge the journal's influence and the potential reach of their work. The fluctuations in impact factor highlight the importance of considering multiple metrics when evaluating a journal's quality.
- For equipment and consumable purchasers, the citation trends suggest that Powder Metallurgy Progress remains a key source of information, which could influence decisions on research investments or product development in the powder metallurgy field.
-
Future Outlook:
- The decline in impact factor in 2022 may prompt the journal to reassess its strategies to maintain or improve its standing. This could include focusing on high-quality submissions, improving editorial processes, or increasing visibility within the scientific community.
- The stable citation count in 2022 indicates that the journal's content is still valuable, and future improvements in impact factor could further enhance its reputation.
In summary, while the impact factor of Powder Metallurgy Progress has seen fluctuations, its citation count remains strong, reflecting its ongoing relevance in the field of powder metallurgy. Researchers and industry professionals should consider both metrics when evaluating the journal's impact and potential contributions to their work.
Summary Table:
Year | Impact Factor | Total Citations |
---|---|---|
2019 | 1.4 | 1342 |
2020 | 1.8 | 1500 |
2021 | 2.228 | 1774 |
2022 | 1.4 | 1628 |
Discover how Powder Metallurgy Progress can support your research—contact us today for more insights!