The industrial brazing process is a versatile and widely used method for joining metals and ceramics by melting a filler material with a lower melting point than the base materials. It relies on capillary action to draw the molten filler into the joint, creating a strong and durable bond upon cooling. This process is suitable for precision, complex, and multi-material components, offering minimal deformation and smooth, aesthetically pleasing joints. Industrial brazing can be performed using various methods, including furnace brazing, vacuum brazing, and controlled atmosphere brazing, each tailored to specific applications and materials. The process involves careful preparation, precise temperature control, and thorough inspection to ensure high-quality results.
Key Points Explained:
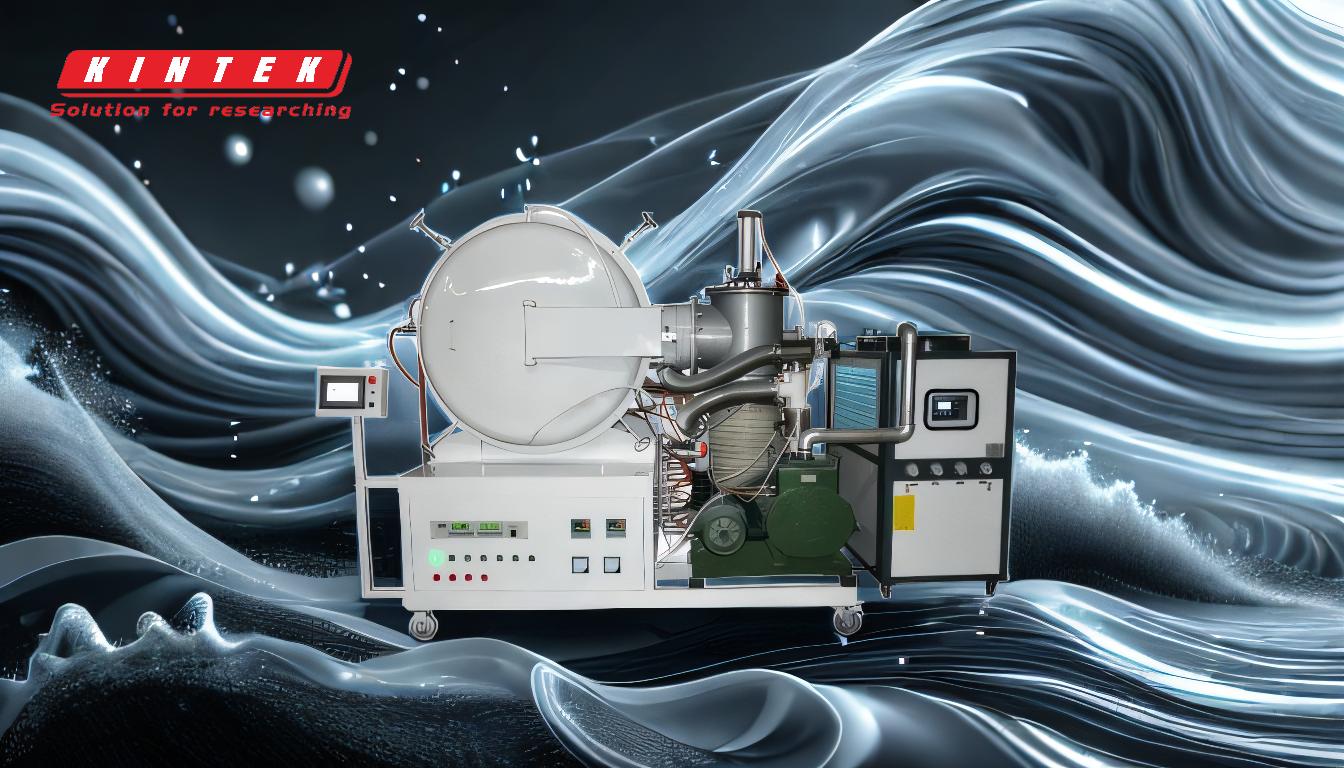
-
Definition and Principle of Brazing:
- Brazing is a joining process that uses a filler material with a lower melting point than the base materials to create a bond.
- The filler material melts and flows into the joint via capillary action, forming a strong connection upon cooling.
- This method is suitable for joining similar or dissimilar materials, including metals and ceramics.
-
Types of Industrial Brazing Processes:
-
Furnace Brazing:
- The entire assembly is heated in a furnace to a temperature where the filler material melts and flows into the joint.
- Suitable for mass production, as it allows for the simultaneous creation of thousands of joints.
- Steps include joint fit checking, surface cleaning, assembly alignment, furnace heating, and post-brazing cleaning.
-
Vacuum Brazing:
- Particularly used for materials like stainless steel, this process involves brazing in a vacuum environment to prevent oxidation.
- Key steps include pre-brazing preparation, assembly and filler metal placement, and post-brazing inspection.
-
Controlled Atmosphere Brazing (CAB):
- Conducted in a furnace with an oxygen-free atmosphere (e.g., nitrogen or hydrogen) to prevent oxidation and contamination.
- Steps include component cleaning, pre-assembly, filler material application, heating, brazing, and cooling.
-
Furnace Brazing:
-
Advantages of Brazing:
- Minimal Deformation: The lower temperatures used in brazing reduce thermal stress and distortion in the base materials.
- Aesthetic Joints: Brazing produces smooth and clean joints, making it ideal for applications where appearance matters.
- Versatility: Suitable for joining dissimilar materials and complex geometries, such as carbide tools and printed circuit boards.
- Scalability: Processes like furnace brazing enable high-volume production with consistent quality.
-
Key Steps in the Brazing Process:
- Preparation: Clean the metal surfaces to remove contaminants like oil, grease, or oxides, ensuring proper wetting of the filler material.
- Assembly: Align the parts precisely and secure them using clamps or fixtures to maintain the correct joint gap.
- Heating: Heat the assembly to the required temperature, ensuring the filler material melts and flows into the joint.
- Cooling: Allow the assembly to cool, solidifying the filler material and creating a strong bond.
- Inspection: Check the brazed joint for quality, ensuring it meets the required standards.
-
Applications of Industrial Brazing:
- Brazing is widely used in industries such as aerospace, automotive, electronics, and tool manufacturing.
- It is ideal for joining precision components, such as those in printed circuit boards, and for creating strong, leak-proof joints in heat exchangers and refrigeration systems.
-
Considerations for Equipment and Consumable Purchasers:
- Filler Material Selection: Choose a filler material compatible with the base materials and the intended application.
- Furnace Type: Select the appropriate furnace (e.g., vacuum, controlled atmosphere) based on the materials and production volume.
- Temperature Control: Ensure the equipment provides precise temperature control for consistent brazing results.
- Inspection Tools: Invest in quality inspection tools to verify the integrity of brazed joints.
By understanding these key points, equipment and consumable purchasers can make informed decisions to optimize the brazing process for their specific needs.
Summary Table:
Topic | Details |
---|---|
Definition | Joining process using a filler material with a lower melting point. |
Types | Furnace brazing, vacuum brazing, controlled atmosphere brazing. |
Advantages | Minimal deformation, aesthetic joints, versatility, scalability. |
Key Steps | Preparation, assembly, heating, cooling, inspection. |
Applications | Aerospace, automotive, electronics, tool manufacturing. |
Considerations | Filler material, furnace type, temperature control, inspection tools. |
Optimize your brazing process with expert guidance—contact us today!