Isostatic pressing is a manufacturing process that applies uniform hydrostatic pressure to a powder material enclosed in a flexible mold, compacting it into a desired shape. This method is particularly effective for creating complex geometries and ensuring uniform density throughout the material. There are two main types: cold isostatic pressing (CIP), performed at ambient temperatures, and hot isostatic pressing (HIP), conducted at elevated temperatures to fully consolidate parts. CIP is further divided into the wet bag and dry bag methods, each with specific applications and advantages. The process is widely used in industries requiring high-density, uniform components, such as aerospace, automotive, and medical device manufacturing.
Key Points Explained:
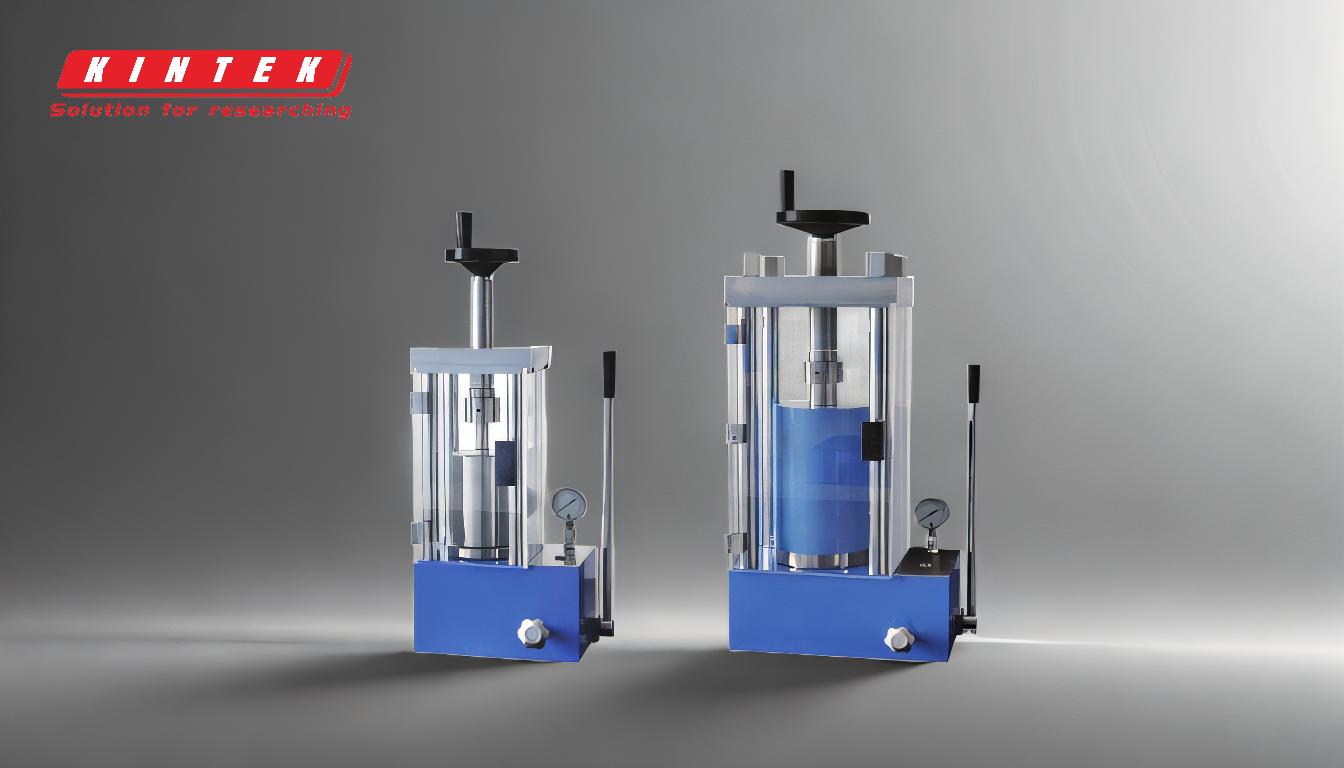
-
Definition of Isostatic Pressing:
- Isostatic pressing involves applying uniform hydrostatic pressure to a powder material enclosed in a flexible mold, typically made of rubber or plastic. This pressure is transmitted through the mold walls to compact the powder into a dense, uniform shape. The process is highly effective for producing complex geometries and ensuring consistent material properties.
-
Cold Isostatic Pressing (CIP):
- CIP is performed at ambient temperatures and is divided into two methods:
- Wet Bag Method: The powder is placed in a flexible mold, which is then submerged in a liquid medium (often an oil-water mixture) inside a high-pressure chamber. The liquid is pressurized, applying uniform pressure to the mold and compacting the powder.
- Dry Bag Method: The mold is fixed within the pressure chamber, and the liquid medium is pumped directly around the mold. This method is more suitable for high-volume production as it eliminates the need to remove and reload the mold after each cycle.
- CIP is performed at ambient temperatures and is divided into two methods:
-
Hot Isostatic Pressing (HIP):
- HIP is conducted at elevated temperatures, typically using inert gases like argon as the pressure medium. The combination of high temperature and pressure allows for solid-state diffusion, fully consolidating the powder into a dense, homogeneous material. HIP is often used for materials that require high strength and integrity, such as those used in aerospace and medical applications.
-
Applications of Isostatic Pressing:
- Isostatic pressing is widely used in industries that require high-density, uniform components. Common applications include:
- Aerospace: Manufacturing turbine blades, engine components, and structural parts.
- Automotive: Producing high-strength, lightweight components.
- Medical Devices: Creating implants and prosthetics with precise geometries and uniform material properties.
- Electronics: Fabricating ceramic substrates and other components with high dimensional accuracy.
- Isostatic pressing is widely used in industries that require high-density, uniform components. Common applications include:
-
Advantages of Isostatic Pressing:
- Uniform Density: The hydrostatic pressure ensures that the material is compacted uniformly, resulting in consistent density throughout the part.
- Complex Geometries: The flexible mold allows for the production of complex shapes that would be difficult or impossible to achieve with other methods.
- Material Versatility: Isostatic pressing can be used with a wide range of materials, including metals, ceramics, and composites.
-
Equipment Used in Isostatic Pressing:
- The key equipment used in isostatic pressing includes:
- Pressure Chambers: Designed to withstand high pressures, often up to 100,000 psi in the case of CIP.
- Flexible Molds: Made from rubber or plastic, these molds conform to the shape of the powder and transmit the pressure uniformly.
- Pumps and Controls: Used to regulate the pressure and temperature during the pressing process.
For more information on the equipment used in cold isostatic pressing, you can refer to the cold isostatic pressing machine.
- The key equipment used in isostatic pressing includes:
-
Challenges and Considerations:
- Mold Design: The design of the flexible mold is critical to achieving the desired shape and density of the final product.
- Material Selection: The choice of material for the mold and the powder must be carefully considered to ensure compatibility with the pressing process.
- Process Control: Precise control of pressure, temperature, and time is essential to achieve consistent results.
In summary, isostatic pressing is a versatile and effective method for producing high-density, uniform components with complex geometries. The process is divided into cold and hot isostatic pressing, each with its own set of applications and advantages. The use of flexible molds and uniform hydrostatic pressure ensures that the material is compacted evenly, resulting in parts with consistent properties and high performance.
Summary Table:
Aspect | Details |
---|---|
Definition | Uniform hydrostatic pressure applied to powder in a flexible mold. |
Types | Cold Isostatic Pressing (CIP) and Hot Isostatic Pressing (HIP). |
CIP Methods | Wet Bag (submerged in liquid) and Dry Bag (fixed mold with direct pressure). |
HIP Process | High temperature and pressure using inert gases for full consolidation. |
Applications | Aerospace, automotive, medical devices, and electronics. |
Advantages | Uniform density, complex geometries, and material versatility. |
Key Equipment | Pressure chambers, flexible molds, pumps, and controls. |
Discover how isostatic pressing can transform your manufacturing process—contact us today for expert guidance!