The lining material for an induction furnace is crucial for its performance and longevity. It serves to contain molten metal, isolate it from the furnace's outer structure, and protect the furnace body during operation. The materials used for lining must withstand high temperatures, thermal shocks, and chemical corrosion. Common materials include high-purity alumina fiber, vacuum-formed fiber materials, and light hollow aluminum oxide plates. These materials offer high service temperatures, rapid heat and cold resistance, and excellent thermal insulation. Special linings are required for specific applications, such as aluminum melting furnaces, due to the unique challenges posed by molten aluminum. Proper lining ensures efficient production and extends the furnace's operational life.
Key Points Explained:
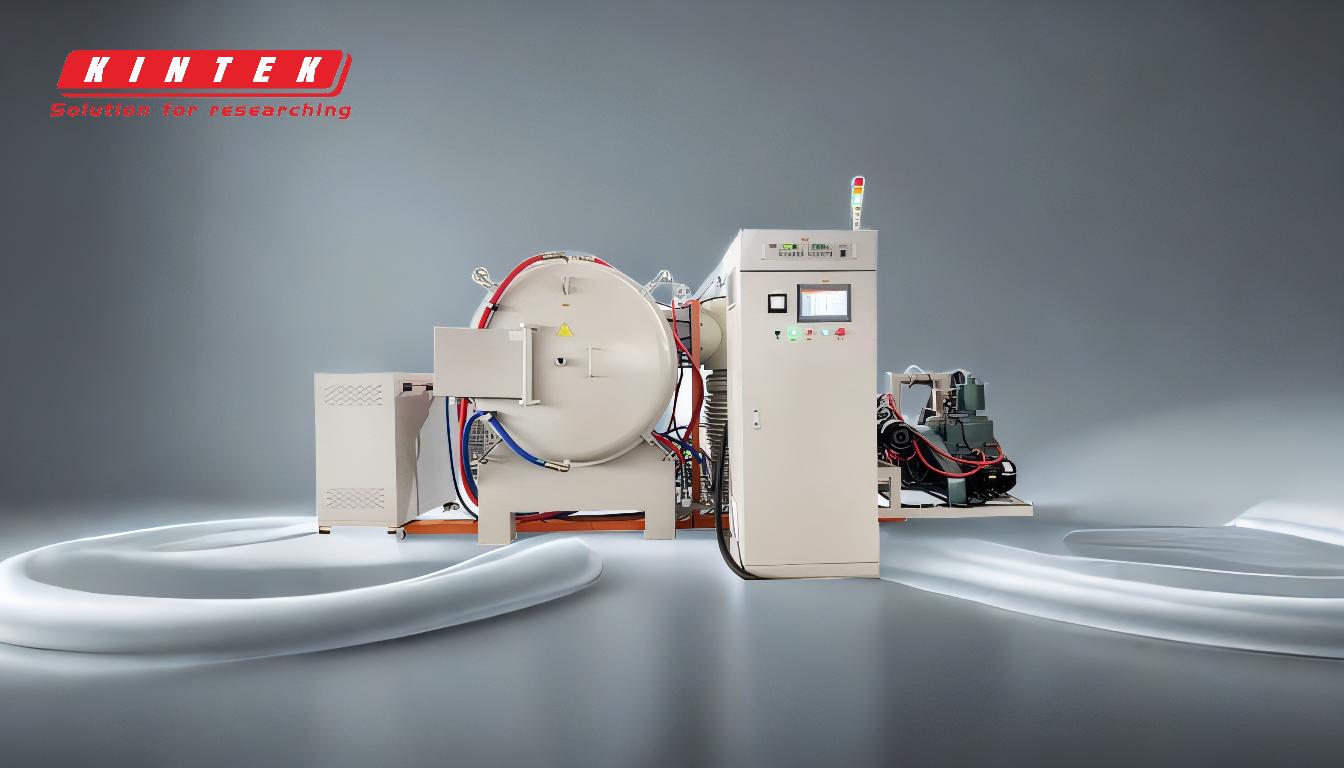
-
Purpose of the Induction Furnace Lining:
- The lining is designed to contain molten metal, isolating it from the furnace's outer structure, such as the coil.
- It protects the furnace body during operation, ensuring smooth and efficient performance.
- The lining is a critical component, directly impacting the furnace's durability and metallurgical performance.
-
Materials Used for Induction Furnace Linings:
- High-purity alumina fiber: Known for its high service temperature and excellent thermal insulation properties.
- Vacuum-formed fiber materials: Provide rapid heat and cold resistance, ensuring durability under thermal stress.
- Light hollow aluminum oxide plates: Offer small heat storage capacity and resistance to cracking or slag falling.
- These materials are chosen for their ability to withstand extreme conditions, ensuring long service life and minimal maintenance.
-
Special Considerations for Aluminum Melting Furnaces:
- Aluminum melting furnaces require specialized linings due to the high frequency of operation, strong penetrability of molten aluminum, and high vibration frequency.
- Linings for aluminum furnaces must be designed to handle these unique challenges, typically lasting for more than 300 heat cycles before needing replacement.
-
Degradation and Operational Life:
- Refractory linings degrade over time due to thermal cycling, chemical corrosion, and mechanical stress.
- The operational life, or lining life, is measured by the number of heat cycles the lining can sustain before requiring repair or replacement.
- Proper maintenance and material selection can significantly extend the lining's operational life.
-
Importance of Proper Lining Procedure:
- The lining procedure directly affects the quality of the furnace and the efficiency of the production process.
- A well-installed lining ensures optimal containment of molten metal, thermal insulation, and protection of the furnace body.
- Improper lining can lead to premature failure, reduced efficiency, and increased operational costs.
-
Advantages of Modern Lining Materials:
- High service temperature: Ensures the lining can withstand the extreme heat of molten metals.
- Rapid heat and cold resistance: Prevents cracking and damage during temperature fluctuations.
- Thermal insulation: Reduces heat loss, improving energy efficiency.
- Durability: Minimizes the need for frequent repairs or replacements, reducing downtime and costs.
By understanding these key points, purchasers and operators of induction furnaces can make informed decisions about lining materials, ensuring optimal performance and longevity of their equipment.
Summary Table:
Key Factor | Details |
---|---|
Purpose | Contains molten metal, isolates from outer structure, protects furnace body |
Common Materials | High-purity alumina fiber, vacuum-formed fiber, light hollow aluminum oxide |
Key Properties | High service temperature, rapid heat/cold resistance, thermal insulation |
Special Applications | Aluminum melting furnaces require specialized linings |
Operational Life | Measured by heat cycles; proper maintenance extends lifespan |
Advantages | Durability, energy efficiency, reduced downtime, and maintenance costs |
Optimize your induction furnace's performance—contact our experts today for tailored solutions!