The lining of an induction furnace is a critical component made of refractory materials, designed to contain molten metal, isolate it from the furnace's outer structure, and protect the furnace body during operation. It is essential for maintaining the efficiency and longevity of the furnace, especially when melting metals like aluminum, which require specialized linings due to their high frequency, vibration, and penetrability. The lining's quality directly impacts the furnace's performance, and its lifespan is measured by the number of heat cycles it can endure before requiring repair or replacement.
Key Points Explained:
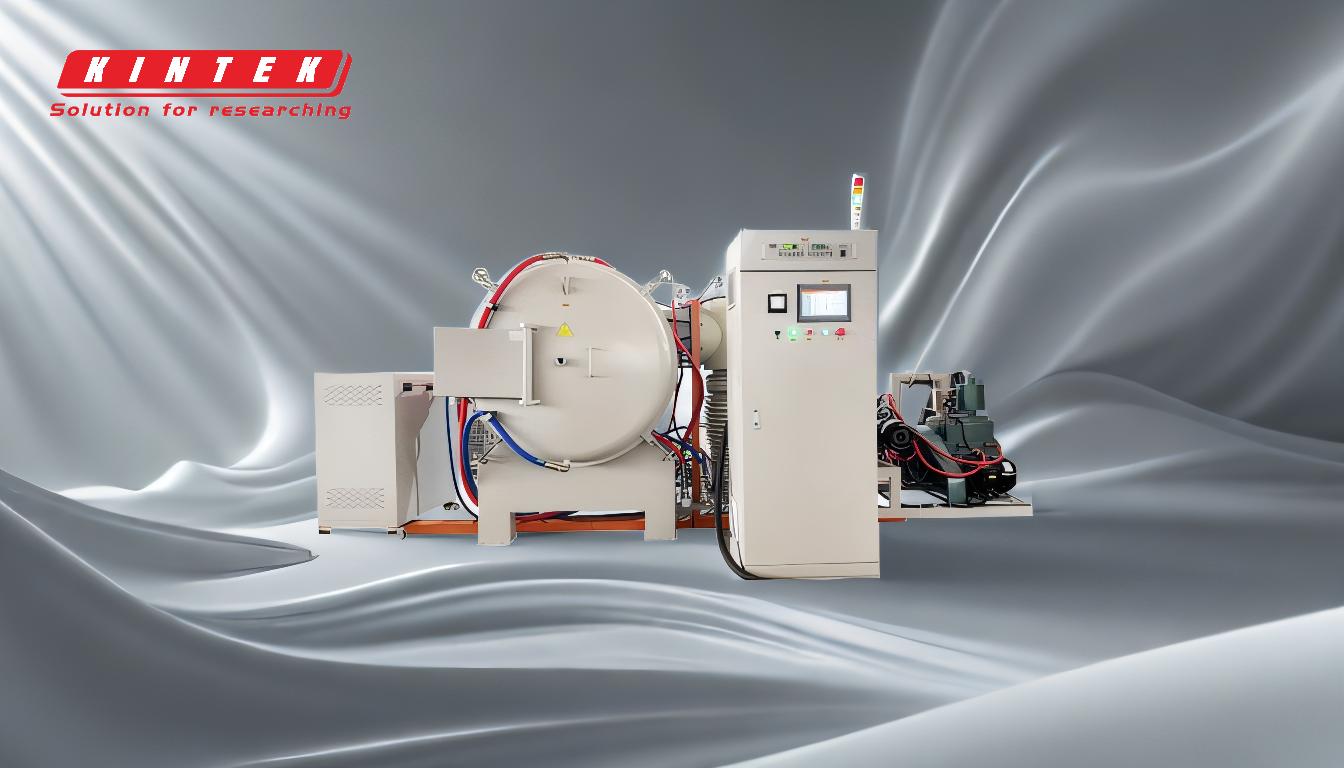
-
Purpose of the Lining:
- Containment of Molten Metal: The primary role of the lining is to hold the molten metal securely within the crucible, preventing leaks and ensuring safe operation.
- Isolation from Outer Structure: The lining acts as a barrier, preventing direct contact between the molten metal and the furnace's outer components, such as the induction coil, which could otherwise be damaged.
- Protection of Furnace Body: By insulating the furnace body from extreme temperatures and chemical reactions, the lining prolongs the furnace's operational life.
-
Composition and Materials:
- Refractory Materials: The lining is typically made from high-quality refractory materials that can withstand extreme temperatures and chemical corrosion. These materials are chosen based on the type of metal being melted.
- Specialized Linings for Aluminum: Due to the unique properties of aluminum (high frequency, vibration, and penetrability), special linings are required for aluminum melting furnaces. These linings are designed to endure more than 300 heat cycles.
-
Importance in Induction Furnaces:
- Critical Component: The lining is considered the most important part of the induction furnace, as its quality directly affects the furnace's efficiency and the quality of the molten metal.
- Operational Life: The lining's lifespan, known as lining life, is a key performance metric. It indicates the number of heat cycles the lining can sustain before it degrades and needs repair or replacement.
-
Degradation and Maintenance:
- Degradation Over Time: Refractory linings degrade due to thermal stress, chemical reactions, and mechanical wear. Regular monitoring and maintenance are essential to ensure optimal performance.
- Repair and Replacement: When the lining reaches the end of its operational life, it must be repaired or replaced to maintain the furnace's efficiency and safety.
-
Impact on Production Efficiency:
- Quality of Lining: A high-quality lining ensures smooth operation, reduces downtime, and improves the overall efficiency of the production process.
- Cost Considerations: While high-quality linings may have a higher initial cost, they offer better performance and longer lifespans, leading to cost savings in the long run.
In summary, the lining of an induction furnace is a vital component that ensures the safe and efficient melting of metals. Its design, material selection, and maintenance are crucial for achieving optimal furnace performance and extending its operational life.
Summary Table:
Key Aspect | Details |
---|---|
Purpose | Contains molten metal, isolates it from outer structure, protects furnace body. |
Materials | High-quality refractory materials; specialized linings for aluminum. |
Importance | Critical for furnace efficiency, quality of molten metal, and lining life. |
Degradation & Maintenance | Degrades due to thermal stress, chemical reactions; requires regular upkeep. |
Impact on Production | High-quality linings reduce downtime, improve efficiency, and save costs. |
Optimize your furnace's performance with the right lining—contact our experts today!