Indirect arc furnaces are primarily used for melting metals, particularly in scenarios where precise temperature control and minimal contamination are critical. These furnaces are well-suited for melting high-quality alloys, refractory metals, and specialty materials like stainless steel, heat-resistant steel, and superalloys. The indirect arc design ensures that the electric arc does not directly contact the charge, reducing contamination and allowing for uniform heating. This makes them ideal for applications in research, laboratory settings, and industries requiring high-purity metals, such as aerospace, tool manufacturing, and advanced materials production.
Key Points Explained:
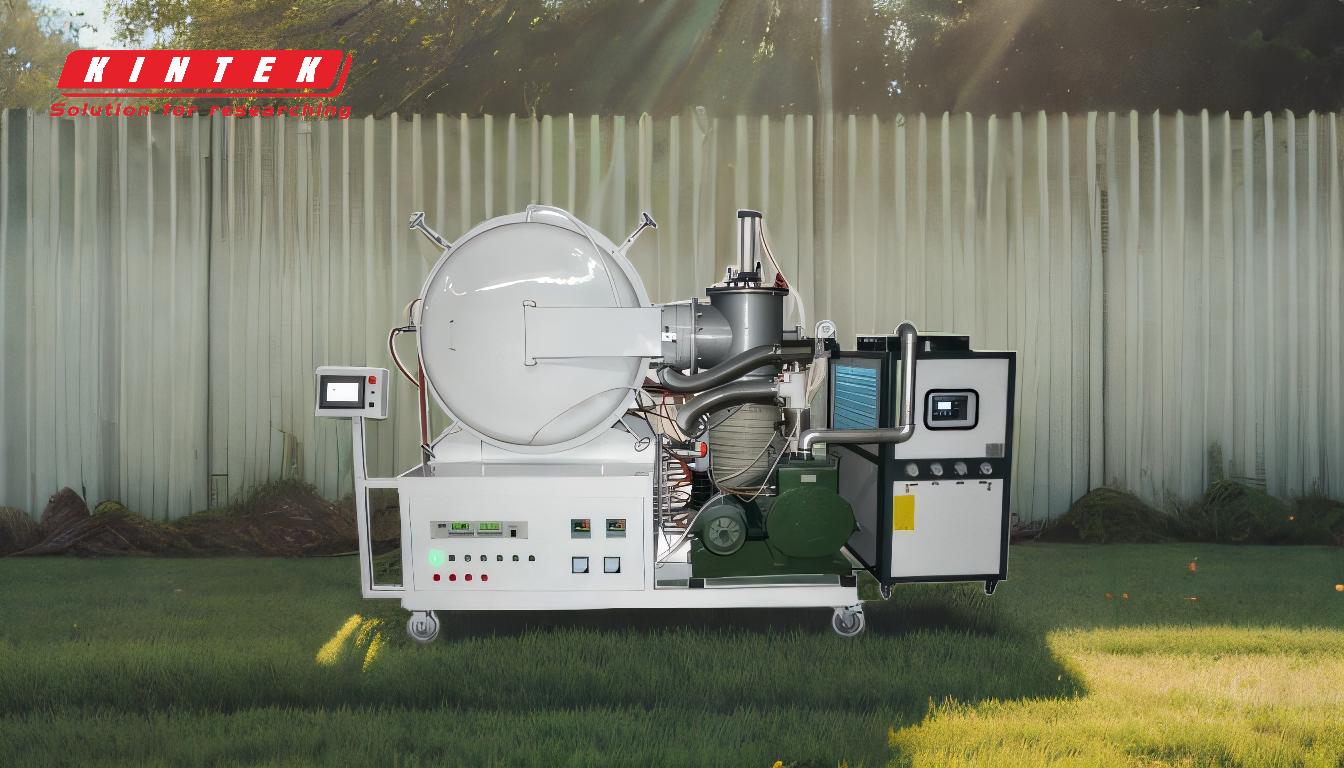
-
Primary Application of Indirect Arc Furnaces:
- Indirect arc furnaces are primarily used for melting metals, especially those requiring high purity and precise temperature control. This includes materials like stainless steel, heat-resistant steel, and superalloys (e.g., nickel base, cobalt base, and iron base alloys).
- The indirect arc design ensures that the arc does not directly contact the charge, minimizing contamination and enabling uniform heating.
-
Design and Heating Mechanism:
- In an indirect arc furnace, the electric arc is struck between two electrodes, and heat is transferred to the charge through radiation and conduction.
- The arc heats the top surface of the charge, and the heat is then conducted to the lower layers, ensuring even melting without direct contact between the arc and the material.
-
Advantages of Indirect Arc Furnaces:
- Minimal Contamination: Since the arc does not touch the charge, there is less risk of impurities being introduced into the molten metal.
- Precise Temperature Control: The indirect heating mechanism allows for better control over the melting process, which is crucial for high-quality alloys and specialty metals.
- Uniform Heating: The conduction of heat from the top surface to the bottom layers ensures consistent melting throughout the charge.
-
Common Materials Melted:
- Stainless Steel: Used in applications requiring corrosion resistance and durability.
- Heat-Resistant Steel: Essential for high-temperature environments, such as aerospace and power generation.
- Superalloys: Nickel, cobalt, and iron base alloys are melted for use in extreme conditions, such as jet engines and gas turbines.
- Refractory Metals: Materials like tungsten and molybdenum, which have high melting points, are often processed in indirect arc furnaces.
-
Applications in Industry and Research:
- Laboratory Research: Indirect arc furnaces are used in research settings to study the properties of refractory metals and metal carbides.
- Aerospace and Defense: High-purity metals and alloys are required for critical components in these industries.
- Tool Manufacturing: Tool steels and bearing steels are melted to produce durable and high-performance tools.
- Advanced Materials: Magnetic materials, elastic alloys, and expansion alloys are processed for specialized applications.
-
Comparison with Other Furnace Types:
- Induction Furnaces: While induction furnaces are also used for melting metals, they rely on electromagnetic induction to generate heat. Indirect arc furnaces are preferred when direct contact with the charge must be avoided.
- Vacuum Induction Furnaces: These are used for melting high-performance materials like superalloys but operate under vacuum conditions to further reduce contamination.
-
Energy Efficiency and Flexibility:
- Indirect arc furnaces are energy-efficient due to their precise heating mechanism, which minimizes heat loss.
- They offer flexibility in processing a wide range of materials, from common metals like aluminum and copper to advanced alloys and refractory metals.
In summary, indirect arc furnaces are specialized equipment designed for melting high-quality metals and alloys with minimal contamination. Their unique heating mechanism and precise temperature control make them indispensable in industries that demand high-purity materials, such as aerospace, tool manufacturing, and advanced materials research.
Summary Table:
Aspect | Details |
---|---|
Primary Application | Melting metals requiring high purity and precise temperature control. |
Design Mechanism | Electric arc between two electrodes heats charge via radiation/conduction. |
Advantages | Minimal contamination, precise temperature control, and uniform heating. |
Common Materials | Stainless steel, heat-resistant steel, superalloys, and refractory metals. |
Applications | Aerospace, tool manufacturing, laboratory research, and advanced materials. |
Energy Efficiency | Precise heating minimizes heat loss, making it energy-efficient. |
Need a solution for high-purity metal melting? Contact our experts today to learn more about indirect arc furnaces!