The maximum service temperature for brazed joints is a critical factor in determining their suitability for high-temperature applications. Brazed joints are widely used in industries such as aerospace, automotive, and power generation, where they must withstand extreme conditions. The strength and durability of these joints depend on several factors, including the design, surface finish, flatness, and material preparation. Proper wetting and capillary action ensure the flow of brazing material, resulting in joints that are stronger than the base material. However, the maximum service temperature is primarily influenced by the brazing filler material and the base metals involved.
Key Points Explained:
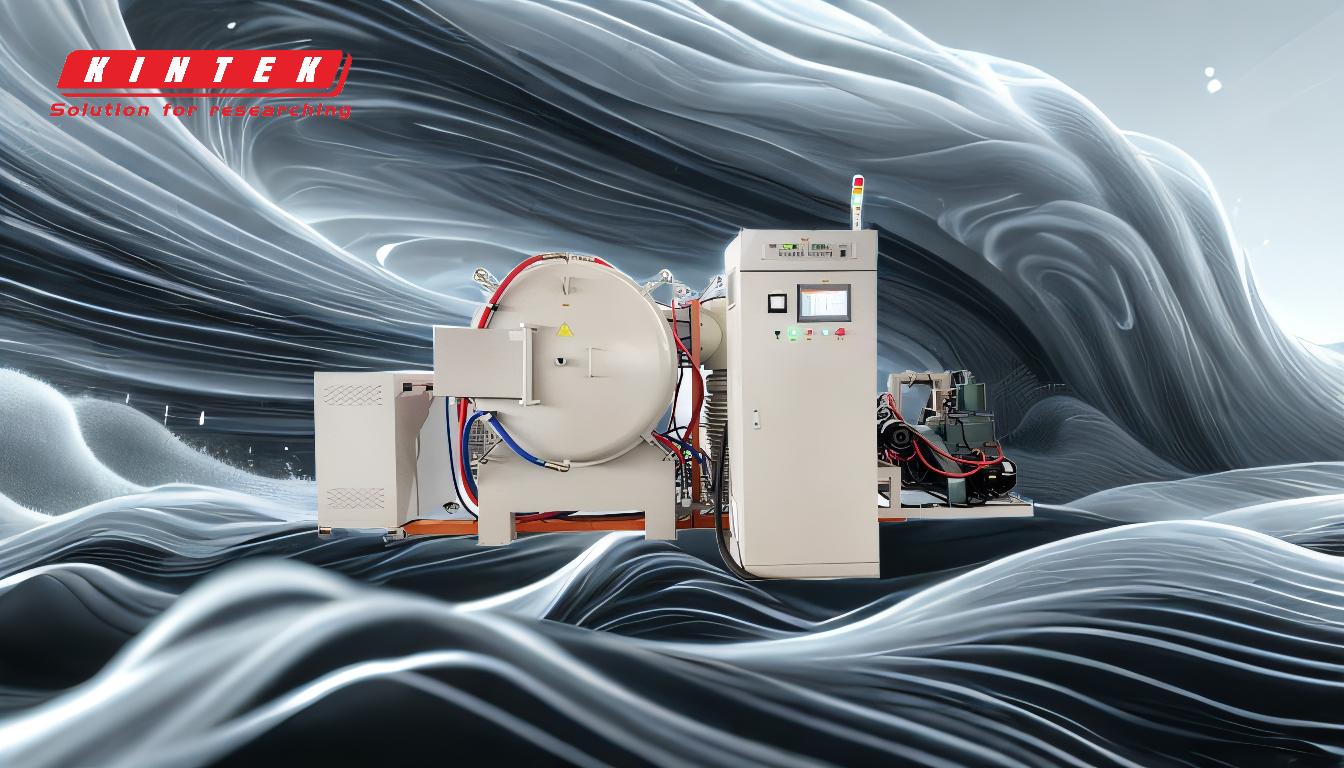
-
Factors Affecting Maximum Service Temperature:
- The maximum service temperature of brazed joints is determined by the melting point and thermal stability of the brazing filler material and the base metals.
- Common brazing filler materials include silver-based alloys, copper-based alloys, and nickel-based alloys, each with different temperature limits.
- The base metals also play a crucial role, as their thermal expansion coefficients and melting points must be compatible with the filler material.
-
Common Brazing Filler Materials and Their Temperature Limits:
- Silver-Based Alloys: These are typically used for low to medium-temperature applications, with maximum service temperatures ranging from 600°C to 800°C (1112°F to 1472°F).
- Copper-Based Alloys: These are suitable for higher-temperature applications, with maximum service temperatures up to 1100°C (2012°F).
- Nickel-Based Alloys: These are used for the highest-temperature applications, with maximum service temperatures exceeding 1100°C (2012°F), often up to 1200°C (2192°F) or more.
-
Influence of Base Metals:
- The base metals must be able to withstand the brazing temperature without melting or degrading.
- Metals such as stainless steel, titanium, and nickel alloys are commonly used in high-temperature brazing applications due to their high melting points and thermal stability.
-
Design and Preparation Considerations:
- Proper joint design is essential to ensure even distribution of the brazing material and to minimize stress concentrations.
- Surface finish and flatness are critical for achieving good wetting and capillary action, which are necessary for strong and durable joints.
- Material preparation, including cleaning and flux application, is vital to remove oxides and contaminants that can impede the brazing process.
-
Applications and Industry Standards:
- In aerospace, brazed joints are used in turbine engines and heat exchangers, where they must withstand temperatures up to 1000°C (1832°F) or higher.
- In the automotive industry, brazed joints are found in exhaust systems and catalytic converters, where temperatures can reach up to 800°C (1472°F).
- Power generation applications, such as gas turbines and nuclear reactors, require brazed joints that can operate at temperatures exceeding 1000°C (1832°F).
-
Testing and Quality Assurance:
- Brazed joints are subjected to rigorous testing to ensure they meet the required temperature and strength specifications.
- Non-destructive testing methods, such as ultrasonic and radiographic testing, are commonly used to detect defects and ensure joint integrity.
- Thermal cycling tests are performed to evaluate the joint's performance under repeated heating and cooling cycles.
In summary, the maximum service temperature for brazed joints is influenced by the choice of brazing filler material, the base metals, and the design and preparation of the joint. Understanding these factors is essential for selecting the appropriate materials and processes to ensure the reliability and durability of brazed joints in high-temperature applications.
Summary Table:
Brazing Filler Material | Maximum Service Temperature |
---|---|
Silver-Based Alloys | 600°C to 800°C (1112°F to 1472°F) |
Copper-Based Alloys | Up to 1100°C (2012°F) |
Nickel-Based Alloys | Exceeding 1100°C (2012°F) |
Need expert advice on brazed joints for high-temperature applications? Contact us today to ensure reliability and performance!