The maximum temperature a tube furnace can achieve depends on its heating elements and design. Common heating elements like HRE resistance wire allow temperatures up to 1200°C, silicon carbon rods enable 1400°C, and silicon-molybdenum rods can reach 1600°C. Some advanced tube furnaces with multiple heating zones can achieve temperatures as high as 1800°C. These high temperatures make tube furnaces suitable for applications such as sintering, calcination, and heat treatment in industries like metallurgy, glass, and new energy. Proper usage, including adherence to rated temperatures and avoiding overheating, is crucial for maintaining performance and longevity.
Key Points Explained:
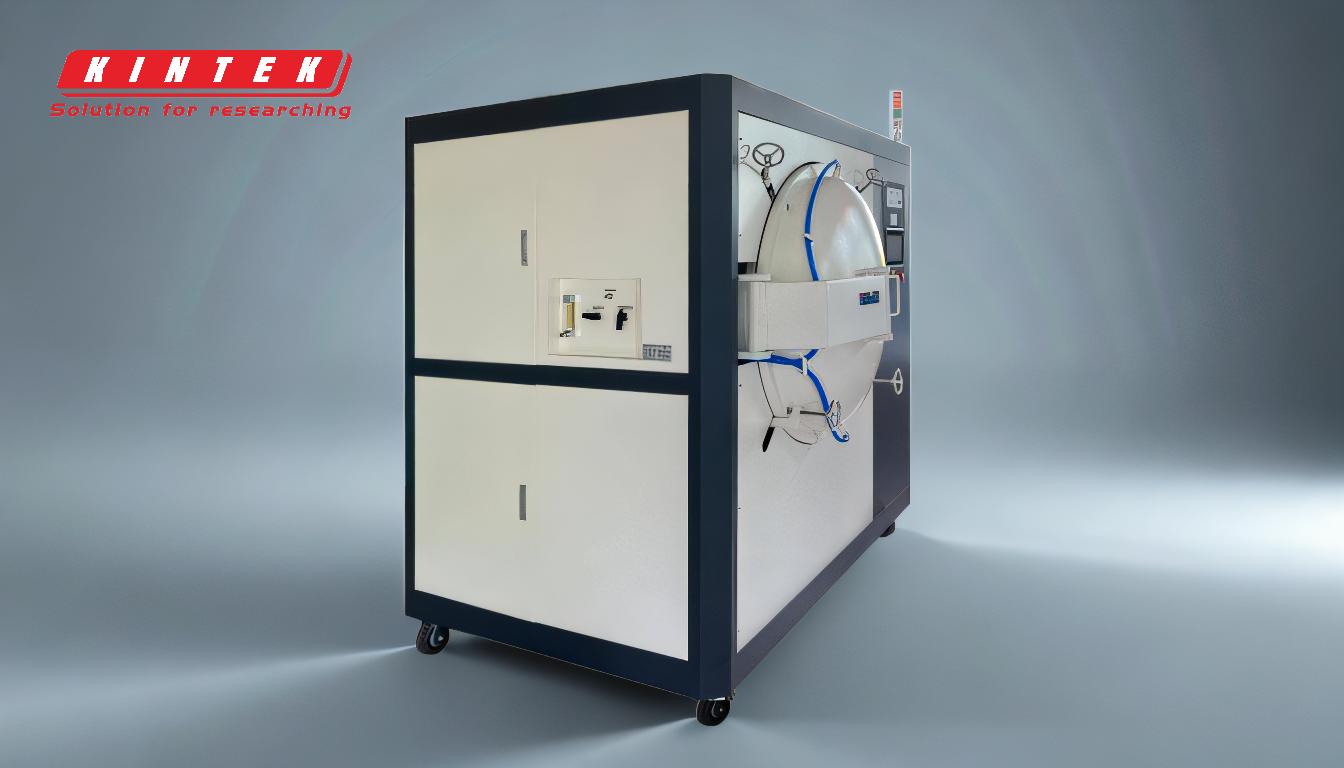
-
Heating Elements and Maximum Temperature
- The maximum temperature of a tube furnace is determined by its heating elements.
- HRE Resistance Wire: Allows temperatures up to 1200°C.
- Silicon Carbon Rods: Enable temperatures up to 1400°C.
- Silicon-Molybdenum Rods: Can achieve temperatures up to 1600°C.
- Advanced tube furnaces with multiple heating zones can reach temperatures as high as 1800°C, making them suitable for high-temperature applications.
- The maximum temperature of a tube furnace is determined by its heating elements.
-
Design and Structure
- A tube furnace typically consists of a cylindrical cavity surrounded by heating coils embedded in a thermally insulating matrix.
- It may include a working tube or vessel to expose materials to controlled temperatures for specific durations.
- The temperature is regulated using feedback from a thermocouple, ensuring precise control.
-
Applications and Industries
- Tube furnaces are widely used in industries such as metallurgy, glass, heat treatment, and new energy.
- They are ideal for high-temperature sintering, calcination, and heat treatment experiments due to their ability to maintain consistent high temperatures.
-
Advantages of Tube Furnaces
- High Thermal Efficiency: Mature technology and simple furnace structure result in low power consumption and high efficiency.
- Ease of Operation: Easy to control and capable of continuous production.
- Versatility: Suitable for a wide range of raw materials and scalable for large-scale production.
- Recovery of Gases: Most cracked gas and flue gas can be recovered, enhancing sustainability.
-
Operational Guidelines
- Tube furnaces should be used according to their rated temperature specifications to avoid overheating or overloading.
- Proper maintenance and adherence to operational limits ensure optimal performance and longevity.
-
Sample Handling and Configuration
- Tube furnaces are designed to heat tubes typically 50 cm to 100 cm in length and 25 mm to 100 mm in diameter.
- Samples are placed inside the tube using ceramic or metal boats and a long push rod, ensuring even exposure to heat.
By understanding these key points, purchasers can select the appropriate tube furnace based on their specific temperature requirements and operational needs.
Summary Table:
Heating Element | Maximum Temperature |
---|---|
HRE Resistance Wire | Up to 1200°C |
Silicon Carbon Rods | Up to 1400°C |
Silicon-Molybdenum Rods | Up to 1600°C |
Advanced Multi-Zone Design | Up to 1800°C |
Need a tube furnace tailored to your high-temperature needs? Contact us today to find the perfect solution!