A hydraulic press operates on the principle of Pascal's Law, which states that pressure applied to a confined fluid is transmitted equally in all directions. This mechanism involves two interconnected cylinders filled with hydraulic fluid: a larger cylinder (Ram) and a smaller cylinder (Plunger). When force is applied to the Plunger, it creates pressure in the hydraulic fluid, which is then transmitted to the Ram, amplifying the force due to the difference in surface areas. This amplified force is used to compress or shape materials. In the context of a hydraulic hot press machine, this mechanism is combined with heating elements and vacuum systems to process materials under controlled high pressure and temperature, ensuring minimal deformation and high-quality output.
Key Points Explained:
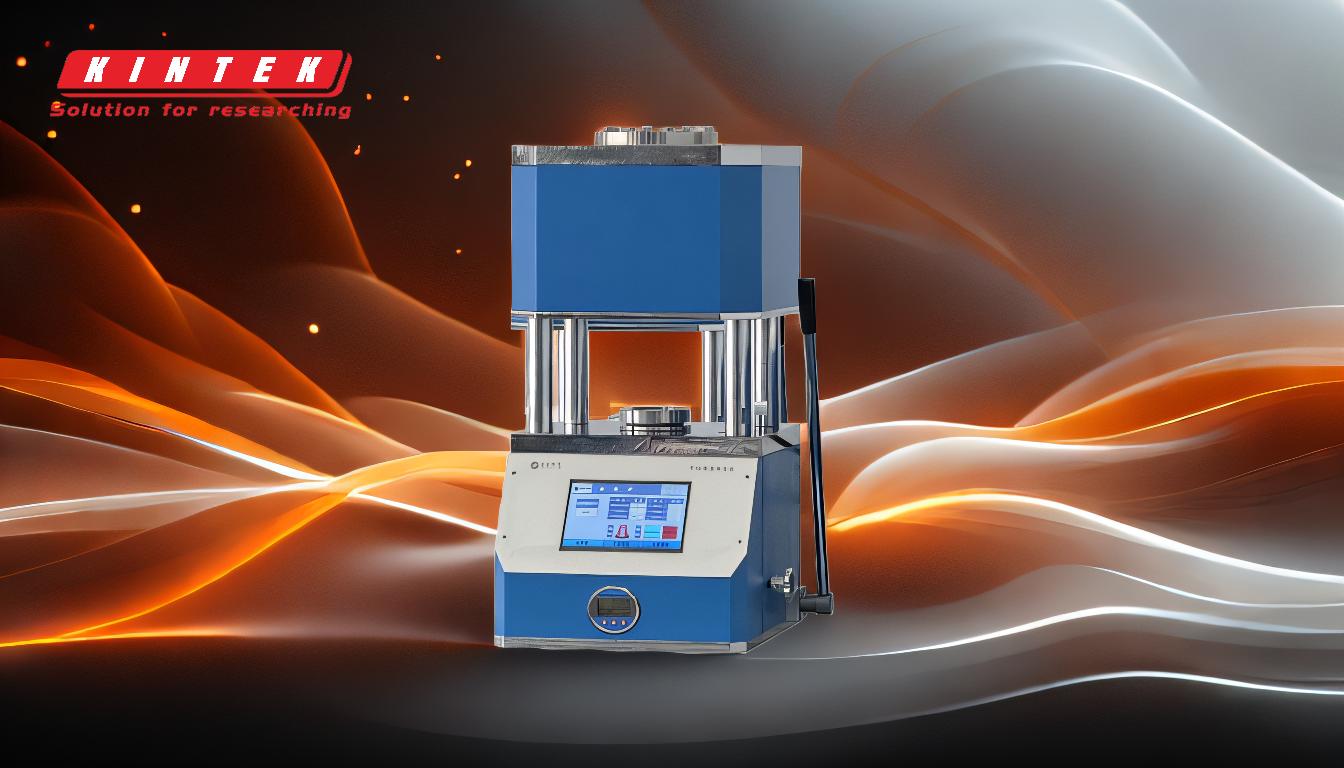
-
Pascal's Law and Hydraulic Mechanism:
- Hydraulic presses operate based on Pascal's Law, where pressure applied to a confined fluid is uniformly distributed.
- The system consists of two cylinders: the Plunger (smaller cylinder) and the Ram (larger cylinder). When force is applied to the Plunger, it generates hydraulic pressure, which is transmitted to the Ram, resulting in a significantly amplified force due to the larger surface area of the Ram.
-
Components of a Hydraulic Press:
- Hydraulic Fluid: Acts as the medium to transmit pressure between the Plunger and Ram.
- Plunger: The smaller cylinder where the initial force is applied.
- Ram: The larger cylinder that delivers the amplified force to the workpiece.
- Pump: Generates the hydraulic pressure required for the system.
- Control Valves: Regulate the flow and pressure of the hydraulic fluid.
-
Application in Hydraulic Hot Press Machines:
- A hydraulic hot press machine integrates the hydraulic press mechanism with heating elements and vacuum systems.
- The machine applies high pressure and controlled temperature to materials, often in a vacuum environment, to facilitate processes like sintering, phase transformation, or solid-phase reactions.
- This combination ensures minimal deformation, improved material properties, and high-quality output.
-
Working Process:
- Heating: The machine heats the material to a specific temperature to make it malleable.
- Vacuuming: A vacuum environment is created to eliminate air pockets and ensure uniform pressure distribution.
- Pressing: Hydraulic pressure is applied to shape or compress the material.
- Forming and Demolding: After the process, the material is cooled and removed from the mold.
-
Advantages of Hydraulic Hot Press Machines:
- High Precision: The hydraulic mechanism ensures consistent and precise pressure application.
- Reduced Deformation: Controlled temperature and pressure minimize workpiece deformation.
- Automation: Many machines are automated, reducing manual intervention and improving efficiency.
- Versatility: Suitable for a wide range of materials and applications, including composites, metals, and ceramics.
-
Applications:
- Used in industries like aerospace, automotive, and electronics for manufacturing components with high strength and precision.
- Ideal for processes like laminating, molding, and bonding materials.
By combining hydraulic force with controlled heating and vacuum environments, hydraulic hot press machines provide a reliable and efficient solution for high-quality material processing.
Summary Table:
Key Component | Function |
---|---|
Hydraulic Fluid | Transmits pressure between the Plunger and Ram. |
Plunger | Applies initial force, generating hydraulic pressure. |
Ram | Delivers amplified force to the workpiece due to its larger surface area. |
Pump | Generates the hydraulic pressure required for the system. |
Control Valves | Regulate the flow and pressure of the hydraulic fluid. |
Unlock the potential of hydraulic press technology—contact us today to learn more!